Древеснослоистые материалы
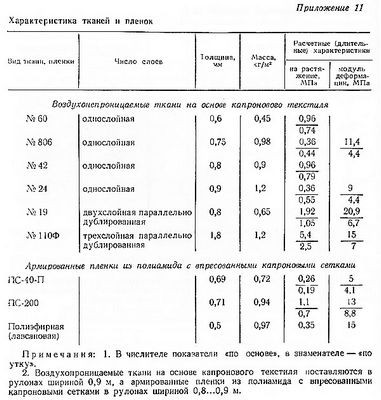
Неспециализированные понятия
К древеснослоистым материалам, занимающим промежуточное положение между фанерой и пластиками, относятся древеснослоистые пластики (ДСПК-1), изготавливаемые на протеиновых клеях: заготовки челночные, погонялки для ткацких станков, ба-келизированная фанера и беролит.
Эти материалы возможно причислить к слоистым пластикам, но необходимо иметь в виду, что пьезотермическая обработка их, за исключением пластика марки ДСПК-1, производится при пониженных удельных давлениях и при меньшей длительности обработки.
Древесина при этих условиях пластифицируется (уплотняется) меньше, чем при производстве слоистых пластиков, исходя из этого у всех древеснослоистых материалов, не считая пластика марки ДСПК-1, объемный вес немного ниже, чем у древеснослоистых пластиков, и находится в пределах 1—1,2.
Помимо этого, клеевые вещества, используемые при изготовлении древеснослоистых материалов, создают в основном прочную клеевую прослойку, соединяющую отдельные слои древесины между собой.
Это пониженные давления и обстоятельство при прессовании являются основанием для применения более вязких и концентрированных нанесения и клеевых веществ их на поверхность шпона в виде узких клеевых прослоек.
Исходя из этого клеевые растворы наносятся на шпон самый простым методом при помощи клеевых вальцов.
Древеснослоистые материалы используются в изделиях, где при большой прочности склейки и довольно достаточной влагостойкости требуется иметь изделия меньшего веса, чем древеснослоистые пластики.
Черта древеснослоистых материалов
Древеснослоистые пластики марки ДСПК-1. Древеснослоистые пластики марки ДСПК-1 являются многослойные плиты, изготовленные из шпона, намазанного протеиновыми клеями растительного либо животного происхождения и склеенного между собой в ходе термической обработки под большим давлением.
Пьезотермическая обработка древесины, как указывалось ранее, существенно полнее происходит, в то время, когда материал состоит не из толстых, а из более узких слоев древесины.
Помимо этого, преимущество пластификации слоистой древесины в виде страниц либо плит перед цельной древесиной содержится в том, что при одной и той же конечной толщине материала быстро снижается влияние недостатков древесины (сучки, завитки, трещины и т. д.) на показатели прочности по окончании ее пьезотермообра-ботки.
Эти события наровне с простотой технологических процессов производства древеснослоистых пластиков и более высокими их физико-механическими особенностями если сравнивать с пластифицированной древесиной в брусках послужили обстоятельством к резкому сокращению производства последней.
Но для изготовления древеснослоистых пластиков используются дефицитные фенол- либо крезол-формальдегидные смолы, каковые не для всех видов слоистых материалов являются необходимыми.
Работами ЦНИИФМ была установлена возможность изготовления древеснослоистых пластиков с применением в качестве связующих протеиновых клеев растительного либо животного происхождения.
Данный вид древеснослоистых материалов владеет более высокими физико-механическими особенностями, чем у пластифицированной древесины в брусках, и намного более высокими, чем показатели фанерных плит. Это разрешает вычислять эти слоистые материалы промежуточными между фанерными плитами и древеснослоистыми пластиками, изготовленными на фе-нол-формальдегидных смолах.
Древеснослоистые пластики марки ДСПК-1 выпускаются в виде плит шириной и длиной до 1500 X 1200 мм и толщиной от 15 до 50 мм.
Заготовки челночные. Заготовки челночные изготавливаются в виде брусков методом разрезки плит, склеенных синтетическими смолами методом тёплого прессования из шпона с параллельным размещением волокон в смежных слоях.
Заготовки челночные предназначаются для изготовления ткац-ких челноков в текстильной индустрии.
Предел прочности челночных заготовок при сжатии на протяжении волокон и при влажности 5% образовывает 1200 кг/см2, при скалывании по плоскости склейки — не меньше 140 кг/см2. Линейное набухание в направлении, обратном прессованию, равняется не более 30%.
Объемный вес находится в пределах 1,15—1,25 г/см3, влажность не выше 12%.
Клееные заготовки для погонялок ткацких станков. Клееные заготовки для погонялок ткацких станков изготавливаются в виде планок клиновидного сечения методом разрезки плит, склеенных синтетическими смолами из шпона с параллельным направлением волокон в смежных слоях.
Клееные заготовки для погонялок имеют объемный вес в основании вершины не меньше 0,9 г/см3, а в средней части — не меньше 0,7 г/см2. Влажность их не более 12%, линейное разбухание в направлении прессования не более 30%.
Предел прочности при сжатии на протяжении волокон равен не меньше 1100 кг/см2, а при скалывании параллельно плоскости склейки — не меньше 115 кг/см2.
Беролит. Беролит создан А. А. Берлиным и выпускается Двух марок: марки Ф из простого шпона, пропитанного дициан-диамидом, и марки Б из шпона, предварительно выщелоченного, после этого пропитанного дициандиамидом.
Беролит изготавливается толщиной 1,5; 2; 3; 4 и 6 м.
Объемный вес беролита находится в пределах 1,3—1,35 г/см3.
Беролит в следствии обработки шпона дициандиамидом способен принимать при нагревании любую форму, которую он сохраняет и по окончании остывания.
Благодаря этим особенностям беролит относится к термогибким материалам.
Беролит марки Ф имеет более низкую термопластичность и может гнуться при малых радиусах изгиба, владеет большей влагостойкостью, повышенными механическими особенностями и имеет олее большую температуру начала размягчения (110—120°).
Беролит марки Б имеет низкую температуру начала размягчения (80—90°).
Бакелизированная фанера. Бакелизированная фанера складывается из нечетного числа слоев березового шпона толщиной не более 1,5 мм, пропитанного либо намазанного смолой и склеенного при взаимноперпендикулярном размещении волокон в смежных слоях.
Бакелизированная фанера изготавливается в виде страниц длиной от 1550 до 7700 мм, шириной от 1200 до 2000 мм и толщиной 5; 7; 10; 12; 14 и 16 мм.
В зависимости от вида смолы, которой намазываются либо пропитываются рубашки и серединки, бакелизированная фанера разделяется на сорта:
БФС — с серединками и рубашками на спиртовой смоле;
БВФ-1—с рубахами на спирторастворимой и с серединками на растворимой смолах;
БФВ-2 — с серединками и рубашками на растворимой смоле.
Влажность фанеры должна быть в пределах 8 + 2%.