Изготовление полимербетонных конструкций
Полимербетонные конструкции изготовляют в специальных цехах, имеющих отделения подготовки заполнителей, изготовление цементной смеси, твердения и формования.
В отделении подготовки заполнителей установлены сушильный барабан, цепной ковшовый элеватор, вибролотки и бункера для щебня и песка, монорельс с электроталью грузоподъемностью 1 т. Заполнители — щебень и песок подают со склада на промывку для удаления глинистых и пылевидных частиц. Песок разгружают в бункер песка, а щебень — на площадку скреперной установки.
Потом скреперные лебедки подают их к вибролоткам, после этого ковшовым элеватором заполнители перемещаются в бункер, из которого по мере необходимости поступают в сушильный барабан. По окончании сушки влажность щебня должна быть не более 1% и песка не более 0,5%.
При необходимости заполнители по окончании сушки фракционируют и после этого подают вторым ковшовым элеватором в бункера-накопители, где они остывают до температуры воздуха в цехе.
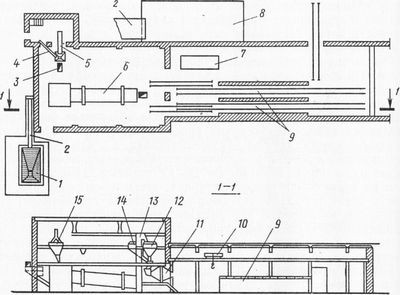
Рис. 1. Замысел цеха полимербетонных конструкций
В отделении изготовление цементной смеси имеются два бетоносмесителя принудительного действия вместимостью 500 л, цепной ковшовый элеватор, бункера-накопители, емкость с дозатором для связующего (фурановая смола ФАМ), емкость с дозатором и паровой рубашкой для отвердителя (бензолсульфокислота) и бункер с дозатором для наполнителя (андезитовая мука).
Детальная схема бетоносмесительного узла приведена на рис. 2. Наполнитель, отвердитель и смола поступают со склада в один момент с заполнителями и попадают в дозаторы, каковые попеременно загружают в бетоносмеситель С-733 все компоненты цементной смеси в определенной последовательности: сперва готовят сухую смесь щебня, наполнителя и песка, перемешивая их в течение 1 … 2 мин.
Затем загружают смолу и перемешивают ее со смесью наполнителя и заполнителей в течение 3 мин до получения однородной (по цвету) массы. В последнюю очередь в бетоносмеситель заливают отвердитель (расплав бензолсульфо-кислоты, нагретый до 35…40 °С) и продолжают перемешивание еще в течение 3 мин.
Так, неспециализированный цикл перемешивания образовывает 7… 8 мин. Температура в смесительном отделении должна быть не ниже 15 °С.
Рис. 2. Схема бетоиосмесительного узла для изготовление полимербетонной смеси на фурановом связующем: 1 — загрузочный ковш; 2 — бункер песка; 3 — бункер щебня; 4 — бункер андезитовой муки; 5 — емкость для связующего; 5 — ванна для подогревания отвердителя; 7 — емкость с от-вердителем бензосульфокислотой; 8, 16, 18, 19, 20, 22 — дозировочный цилиндр; 9 —дозатор для заполнителей; 10 — бункер сыпучих материалов; 11 — бетоносмеситель С-773; 12 — цилиндр разгрузочного люка; 13 — приемный короб; 14 — дозатор андезитовой муки; 15 — выгрузочный цилиндр; 17 — дозатор жидких компонентов; 21 — вентили
При применения полиэфирного связующего технологический процесс пара видоизменяется. Связующее делится на две равные части, в одну из них вводится инициатор (гидроперекись изопропилбензола), во вторую — ускоритель (10%-ный раствор нафтената кобальта в стироле).
В бетоносмеситель обе части связующего подают равными частями. Исходя из этого нужны две равные емкости для полиэфирной смолы, две емкости для ускорителя и раздельного хранения инициатора (яркое смешивание не допускается чтобы не было взрыва) и два смесителя для перемешивания смолы с инициатором и смолы с ускорителем.
По окончании перемешивания масса выгружается в железные формы, установленные в отделении формования конкретно, под бетоносмесителями (на схеме рис. 4.25 не продемонстрированы).
Дабы сократить разрыв между ее укладкой и приготовлением смеси, формы устанавливают вероятно ближе к бетоносмесителям, а для подачи смеси используют устройства (желоба, лотки и т. п.), ускоряющие процесс укладки. Для предотвращения прилипания бетона к поверхности форм их смазывают смесью технического мыла с графитом либо раствором битума в бензине.
Арматуру укладывают в соответствии с рабочими чертежами, оставляя промежуток для защитного слоя бетона не меньше 25 …30 мм. Уплотнение смеси в формах производится на вибростоле 7, с амплитудой 250… 300 и-1 частотой мин 2,5…3,0 мм.
Для уплотнения используют кроме этого виброплощадки и навесные вибраторы, каковые включаются в воздействие по окончании укладки каждого замеса и выключаются при появлении на поверхности полимербетона слоя жидкости.
По окончании уплотнения полимербетона формы устанавливают на особые тележки и вкатывают в камеры сухого нагревания, расположенные в отделении отверждения. Отделение оборудовано кроме этого кран-балкой с электроталью грузоподъемностью 5 т. Твердение полимербетона происходит при температуре 80 °С со скоростью снижения и подъёма температуры не более 0,5 °С в 60 секунд.
Таковой режим создается паровыми регистрами либо электронагревателями. Длительность твердения в камере 3…4 ч, после этого изделия извлекают из форм и твердение длится в цехе при температуре 18…20°С и влажности воздуха 60…70%.
По таковой разработки изготовляют балки, колонны, фундаментные блоки.
Листовые и плитные изделия толщиной 8… 25 мм изготовляют на полуавтоматической линии (рис. 4.27) по следующей разработке. Промытый песок со склада конвейером подается в сушильный барабан, после этого в охладительный барабан. Температура в первом барабане 150 °С, во втором 80 °С.
Из охладительного барабана песок элеватором направляется в бункер-накопитель, оттуда он попадает через дозатор в смеситель вместе с кварцевой мукой, подаваемой через тот же дозатор из бункера. Состав смеси 73:20 (песок: мука) по массе.
Ко мне же из хранилищ поступают эпоксидная смола и от-вердитель. Масса шепетильно перемешивается и выгружается в распределительную воронку, из которой равномерно слоем шириной около трех метров распределяется на бумажном странице, движущемся на металлической плите.
После этого масса калибруется двумя парами валков и обжимается третьей парой валков с удельным давлением 16 МПа. Отформованный лист попадает в камеру, в которой при температуре 150°С в течение 1,5 …2 ч происходит термообработка изделия для ускорения твердения связующего.
Пройдя участок охлаждения, лист попадает на должность продольной и поперечной распиловки, где алмазными пилами разрезается на плиты нужных размеров. Плиты подсушивают на установке 15 и посредством вакуумных захватов снимают с конвейера.
При скорости конвейера 1…2 м/мин и ширине страницы 2,7 м производительность линии образовывает 160… 320 м2 изделий в час.
Приобретаемые плиты при плотности 2,2 т/м3 имеют прочность при сжатии 120… 150 МПа, при изгибе 27 …40 МПа, при растяжении 12…27 МПа. Водопоглощение плит не более 6%.
Плиты применяют в качестве наружных обшивок трехслойных панелей и как материал для несущих элементов таврового либо коробчатого сечения.
Для изготовления плитных изделий из полиэфирного полимер-оетона на полуавтоматической линии применяют разные виды песка — барханный, речной, мелкозернистый. Песок ушат при 120 °С, просеивают и распределяют в букера-накопи-тели по фракциям.
После этого разные фракции смешивают для получения сухих смесей и подают на установку для изготовление цементной смеси. Полиэфирная смола, метилметакрилат, сухая смесь сыпучих компонентов, ускоритель и инициатор полимеризации, отбеливающие и пигментная пасты последовательно загружаются в смесительную головку, перемешиваются шнеком и подаются для заливки в формы.
Поверхность форм покрыта изнутри антиадгезионной смазкой (21%-ный раствор низкомолекулярного полиэтилена в хлористом метилене). Заполненные формы вибрируют на горизонтальном вибростоле с амплитудой 100… 200и-1 частотой мин 2… 4 мм, после этого направляют на конвейере в камеру полимеризации.
Отверждение продолжается 60 мин при 80С.
Рис. 3. Схема полуавтоматической линии для производства листового полимербетона
Рис. 4. Технологическая схема производства плит из полиэфирного полимер-бетона: 1 — приемный бункер заполнителей; 2 — ленточный конвейер; 3 — барабанная сушилка; 4, 7 И — ковшовые элеваторы; 5 — сепаратор; 6, 8—бункера; 9 — весовые дозаторы; 10 — роли ковый транспортер; 12 —. смеситель для сухих компонентов; 13, 15 — емкость для отверди теля и ускорителя; 14 — емкость для смолы; 16 — заливочная установка; 17 — бункер зали вочной установки; 18 — формы; 19, 20 — рольганги; 21 — вибростол; 22 — камера предвари тельной полимеризации; 23 — пост заливки; 24 — камеры окончательной полимеризации 25—очистки форм и пост распалубки
Рис. 5. Технологическая схема изготовление карбамидного полимербетона: 1 — склад; 2 — отделение подготовки заполнителей; 3 — то же, наполнителей; 4 — смесительный узел; 5 — склад карбамидной смолы; 6 — склад отвердителя
Разработка карбамидных полимербетонов отличается раздельным приготовлением смеси смолы с наполнителем и смеси заполнителей, каковые после этого совмещаются. Такая разработка снабжает лучшие свойства и большую однородность материала.
Наполненные карбамидные связующие приготовляют в особых быстроходных смесителях с частотой вибрации 200… 800 мин-1. Вместимость смесителя 250 л, продолжительность перемешивания 30… 40 с, производительность 20 циклов в час.
Приготовленное карбамидное связующее срочно подается в бетоносмеситель для перемешивания со смесью сухих щебня — и заполнителей песка. Употребляются бетоносмесители принудительного действия С-742, С-951.
Перемешивание продолжается 1,5 …2 мин, затем смесь нужно скоро (не более 15…30 мин) уложить в формы. Для этого применяют обычный бетоноукладчик.
Освоена разработка нового композиционного материала — бето-нополимера. Пропитку бетонов чтобы получить конструкции и изделия из бетонополимеров реализовывают низковязкими мономерами винилового последовательности с ускорителями и инициаторами радикальной полимеризации и добавками, повышающими огнестойкость конструкции.
Перед пропиткой изделия из бетона сушат до влажности не более 0,5… 1,0% по маосе способом конвективной, радиационной, вакуумной либо высокочастотной сушки. Пропитку ведут в герметичных камерах с предварительным вакуумированием до 1… 2 кПа, после этого создают избыточное давление 0,2 МПа сжатым азотом.
Длительность каждого этапа режима пропитки зависит от плотности и класса бетона. Корпус пропиточной камеры изготовляют из металлических либо алюминиевых сплавов, герметизирующие прокладки — из силиконовых каучуков, фторопласта, бензостойкой резины.
Расход пропитывающего состава контролируется по мерному стеклу либо уровнемерами дистанционного действия.