Изготовление технологической оснастки
Для изготовления модельной оснастки литьевых форм (для литья по выплавляемым моделям), формовочных, гибочных и вытяжных штампов, зажимных приспособлений применяют компаунды на базе эпоксидных смол. Отлитые по мастер-подробности эпоксидные формы не требуют дополнительной механической обработки.
Трудоемкость изготовления крупногабаритных штампов из эпоксидных смол значительно уменьшается если сравнивать с трудоемкостью изготовления подобных металлических штампов на 30—40% за счет сокращения копировально-фрезерных работ. Не считая оснастки эпоксидные компаунды разрешают исправлять недостатки в пористость (и литьё раковины), коррозионные разрушения, ликвидировать трещины в подробностях, заделывать сквозные отверстия.
Главными исходными смолами для данной цели являются ЭД-5 и ЭД-6.
Режим отверждения: загрузить в сушильную камеру при 70 °С; выдержка — 2 часа. Повысить температуру от 70 до 120 °С в течение 4—6 часов; выдержка при 120 °С — 6 часов. Повысить температуру от 120 до 140 °С в течение 24 часов.
Охлаждение до комнатной температуры вместе с сушильной камерой.
Данный компаунд снабжает громаднейшую прочность при статическом изгибе (920 кгс/см2) и при сжатии (1504 кгс/см2), твердость по Бринеллю (30 кгс/мм2), теплоемкость по Мартенсу 68 °С.
Процесс изготовления подробностей оснастки из эпоксидного компаунда складывается из следующих операций:
1) подготовка и изготовление железной, древесной либо гипсовой формы для заливки эпоксидного компаунда;
2) заливка и приготовление компаунда;
3) отверждение компаунда в форме;
4) извлечение эпоксидной подробности.
Самый несложны в изготовлении гипсовые формы. В древесный коробку помещают мастер-подробность и заливают гипсовой массой. По окончании извлечения мастер-подробности заделывают неровности поверхности эпоксидным компаундом холодного отверждения (отвердитель — полиэти-ленполиамин).
Форма готова к применению.
Изготовление шаблонов из самотвердеющих пластмасс производится прессованием их по контршаблонам. По одному контршаблону возможно изготовить много а также тысячи повторяющихся шаблонов для заточки резцов, сверл и другого режущего инструмента.
Шаблоны прессуются в основном из самотвердеющей пластмассы АСТ-Т.
Последовательность изготовления шаблонов по контршаблонам следующая: порошок полиметилмета-крилат (эмульсионный с добавками пигмента и ингибитора) и жидкость (метилметакрилат с активатором) смешивают в соотношении 2:1 в стеклянном либо фарфоровом сосуде. Для набухания порошка в жидкости его оставляют в сосуде на 10—15 мин.
Для прессования изготовляют особую форму. Форма складывается из рамки, в которую помещают контршаблон и две ровные плиты. Рамку укладывают на нижнюю плиту и в середину кладут контршаблон.
Сверху загружают массу и закрывают верхней плитой. После этого форма устанавливается под пресс, и производится прессование.
Так как давление прессования пластмасс АСТ-Т не превышает 10—30 кгс/см2, то кроме того громадные шаблоны возможно прессовать на ручных винтовых прессах. Продолжительность выдержки формы под прессом при 25—30 °С образовывает 5—15 мин, по окончании чего форма разбирается и облой на шаблоне зачищается.
Изготовление кондукторной плиты. Схема изготовления кондукторной плиты с закреплением втулок быстротвердеющей пластмассой ТШ приведена на рис.
2. Процесс изготовления кондукторной плиты складывается из установки кондукторных втулок по концевым угольнику и мерам длины и заливки втулок пластмассой.
Порядок сборки кондукторной плиты следующий: к поверхности ровной железной контрольной плиты струбциной прижимают разметочный угольник, внутренние грани которого применяют как оси координат, по которым заданы горизонтальные и вертикальные оси размещения кондукторных втулок.
Дабы установить втулку в заданном положении, нужно совершенно верно измерить ее наружный диаметр и собрать блок концевых мер длины , равных размерам.
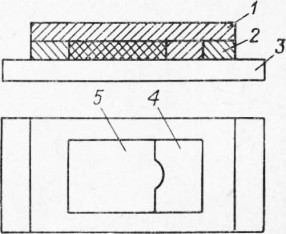
Рис. 1. Форма для прессования шаблонов
Для фиксации положения втулки ее торец смазывают жидким эпоксидным клеем и прижимают к плите. Остальные кондукторные втулки закрепляют подобным методом.
По окончании установки их на контрольной плите на втулки надевают кондукторную плиту, которая должна иметь отверстия под втулки. Диаметр отверстий должен быть больше наружного диаметра втулок на 4—6 мм.
Перед надеванием кондукторной плиты на втулки поверхности контрольной плиты смазывают разделительным составом, а стенки отверстий и поверхности втулок кондукторной плиты обезжиривают органическим растворителем.
При установке кондукторной плиты ее боковые стороны шепетильно выверяют по разметочному угольнику, прижимают к контрольной плите струбцинами и в зазоры между втулками и стенками отверстия заливают пластмассу.
По окончании отверждения пластмассы контролируют межосевое расстояние кондукторных втулок, а после этого отделяют кондукторную плиту с втулками от контрольной плиты. Излишки клея удаляют с плиты и торцов втулок шабером.
Рис. 2. Схема изготовления кондукторной плиты с закреплением втулок пластмассой
Гидропласты. В производстве приспособлений все большее использование находят композиции из полихлорвиниловой смолы, стеарата и дибутилфталата кальция.
Эти композиции взяли в инструментальном производстве наименование гидропластов.
Используется пара марок гидропластов. Самый распространенные марки гидропласта: С, СМ и МАТИ-14.
Изготовление зажимных приспособлений с гидропластом. Зажимные приспособления с гидропластом используют при чистовой обработке цилиндрических подробностей, изготовляемых с высокой точностью (до 0,01 мм).
На рис. 6 продемонстрирована оправка с гидропластом. Корпус оправки крепится к планшайбе.
На корпусе напрессована в нагретом состоянии разжимная втулка, на которой для лучшего уплотнения в местах посадки сделаны кольцевые углубления. Рабочая (узкая) часть втулки — мембрана — должна быть изготовлена с высокой точностью.
Разнотолщинность стенок втулки может привести к смещению оси обрабатываемой подробности.
В каналах корпуса и в цилиндрической полости между втулкой и корпусом находится пластическая масса (гидропласт). Под действием Давления, информируемого винтом через поршень гидропласту, втулка расширяется, центрируя и закрепляя обрабатываемую подробность.
Заполнение приспособления гидропластом производится в такой последовательности. Разрезанный на куски величиной 0,5—1 см3 гидропласт нагревают до плавления (120—130 °С) в бачке, помещенном в масляную ванну.
Приспособление перед заливкой гидропласта нагревают до 120—140 °С. Винт, плунжер и резьбовую пробку приспособления, закрывающую отверстие для выхода воздуха, удаляют и заливают расплавленный гидропласт через плунжерную камеру в рабочую полость до заполнения всей полости с избытком, пока гидропласт не потечет через отверстие для выхода воздуха.
Рис. 3. Оправка с гидропластом