Основные свойства инструментальных материалов
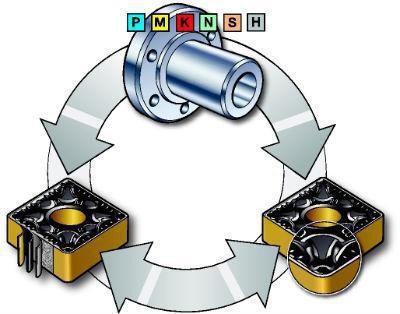
Материалы, используемые для изготовления режущих инструментов, возможно разбить на три главные группы:
1) инструментальные стали;
2) жёсткие сплавы;
3) неметаллические инструментальные материалы.
Инструментальный материал обязан владеть определенными эксплуатационными особенностями, соответствующими условиям работы режущего инструмента. прочность и Твёрдость инструментального материала должна быть выше подобных параметров обрабатываемого чугуна (и материала стали).
При резании рабочая часть инструмента нагревается до больших температур, а его режущие кромки подвергаются интенсивному износу, исходя из этого инструментальный материал обязан владеть высокими теплоустойчивостью и износостойкостью.
Инструментальные стали. Сплав железа с углеродом (содержание последнего образовывает 0,1-1,7%) именуют сталью.
Стали, которые содержат более 0,65% углерода и отличающиеся именно поэтому высокой твердостью, именуют инструментальными.
Для улучшения эксплуатационных либо технологических особенностей инструментальной стали в ее состав вводят легирующие (улучшающие) элементы. Такие стали именуют легированными и в их обозначение (марку) включают русскую букву, соответствующую заглавию легирующего элемента: X — хром (Сг); Ф — ванадий (V); Н — никель (Ni); К — кобальт (Со); Г — марганец (Mn); Т — титан (Ti); М — молибден (Мо); Б — ниобий (No); С — кремний (Si); Та — тантал (Та); В — вольфрам (W) и т. д.
Углерод в марке стали буквенного обозначения не имеет, а его содержание (в десятых долях процента) показывают в начале маркировки. Содержание легирующего элемента показывают в процентах по окончании соответствующей буквы.
К примеру, легированная хромокремни-свора сталь марки 9ХС содержит 0,9% углерода, 1% хрома и 1% кремния. В случае если содержание в стали углерода либо легирующего элемента равняется либо приблизительно равняется 1%, то единица в маркировке опускается.
К примеру, сталь марки ХВГ содержит 1% углерода, 1% хрома, 1% марганца и 1% вольфрама.
Углеродистым инструментальным сталям в зависимости от содержания углерода присваивают марки У7А, У8А, У9А, У10А, УНА, У12А, У13А. К примеру, сталь марки У7А: углеродистая (буква У), содержит 0,7% углерода (цифра 7); отличная (буква А), т. е. имеющая пониженное содержание вредных фосфора (и примесей серы).
Теплоустойчивость (QK = = 180-Ь220°С) и износостойкость углеродистых инструментальных сталей ниже, чем подобные параметры вторых инструментальных материалов. Чем выше содержание углерода, тем выше эти параметры.
Твердость (по окончании отжига) 187—207 НВ есть низкой, исходя из этого эти стали прекрасно обрабатываются резанием.
Закаленные углеродистые стали прекрасно шлифуются. Эти стали (самые дешёвые из инструментальных материалов) используют для того чтобы, трудящихся в условиях низких температур резания: деревообрабатывающих и слесарно-монтажных инструментов; шаблонов и калибров пониженной точности; напильников, шаберов, накатных роликов, метчиков и др.
К низколегированным инструментальным сталям относятся стали марок 9ХС, ХГС, ХВГ, ХВГС и др. Эти стали, которые содержат около 1% углерода, и хром (1%), марганец (1%), кремний (1%) и вольфрам (1%), характеризуются лучшей закаливаемостью, повышенными прокаливаемостью и теплоустойчивостью, меньшей склонностью к росту зерна.
Стали, которые содержат марганец, отличаются малой деформацией при термической обработке. Легирование вольфрамом и хромом повышает износостойкость и другие эксплуатационные особенности.
Теплоустойчивость этих сталей QK — 250-260 °С, прокаливаемость образовывает 40—50 мм, твердость (по окончании отжига) 241—255 НВ. Обрабатываемость низколегированных сталей немного хуже, чем углеродистых, они более склонны к прижогам при шлифовании.
Указанные стали применяют для того чтобы, метчиков, сверл, разверток и др., и штампов холодной штамповки.
Быстрорежущие стали используют для изготовления режущих инструментов, действующий при высоких скоростях, температурах и усилиях резания. Эти стали отличаются высокими износостойкостью, теплоустойчивостью, вязкостью и прочностью.
Быстрорежущие стали подразделяют на две группы: 1) стали, легированные молибденом и вольфрамом и которые содержат до 2% ванадия (Р18, Р12, Р9, Р6М5, Р6МЗ и др.); 2) стали, леги-, рованные кобальтом и вольфрамом и которые содержат более чем 2% ванадия (Р18Ф2, Р14Ф5, Р9Ф5, Р10Ф5К5, Р9К5, Р9КЮ и др.).
Первую группу относят к сталям обычной производительности, а вторую — к сталям повышенной производительности.
В начале маркировки этих сталей стоит буква Р (что свидетельствует быстрорежущая), следующая за ней цифра показывает среднее содержание вольфрама (), цифры и последующие буквы обозначают наименования вторых легирующих элементов и соответственно их среднее содержание (). Помимо этого, в быстрорежущих сталях находятся углерод (0,7—1,5%), хром (3—4,4%) и другие элементы, каковые в маркировке не показывают.
К примеру, быстрорежущая сталь марки Р18 содержит 0,7—0,8% углерода, 17—18,5% вольфрама, 3,8—4,4% хрома, 1 —1,4% ванадия.
Высокие эксплуатационные особенности быстрорежущих сталей обеспечиваются благодаря их легированию вольфрамом, молибденом и ванадием, каковые, соединяясь с углеродом, образуют соответствующие карбиды (WC, VC и МоС). Износостойкость быстрорежущих сталей в 3—5 раз выше, чем у углеродистых и низколегированных; теплоустойчивость образовывает 620 °С, а при легировании кобальтом 640 °С.
Наличие ванадия содействует образованию мелкозернистой структуры, что повышает прочность и снижает хрупкость стали.
Быстрорежущие стали владеют кроме этого высокими технологическими особенностями: закаливаются в нагретом масле, расплавах солей и при охлаждении на воздухе (т.е. не требуют резкого охлаждения); прокаливаются по всему поперечному сечению независимо от размера заготовки.
Недочётами этих сталей являются высокая твердость в состоянии поставки (255—269 НВ); склонность к карбидной неоднородности; пониженная шлифуемость (особенно у сталей, легированных ванадием).
Чем выше содержание редких легирующих элементов (особенно вольфрама), тем выше стойкость быстрорежущих сталей.
Самый распространенной есть сталь марки Р6М5, используемая для изготовления всех видов режущих инструментов, предназначенных для обработки (со скоростью резания до 1 —1,2 м/с) углеродистых и средне-легированных конструкционных сталей.
Жёсткие сплавы являются железные материалы, отличающиеся высокими теплоустойчивостью, износостойкостью и твердостью. твёрдость и Теплостойкость этих сплавов соответственно вдвое и 1,3—1,4 раза выше подобных параметров быстрорежущей стали марки Р18.
Исходя из этого и стойкость твердосплавных инструментов существенно выше стойкости быстрорежущих инструментов, причем это преимущество тем больше, чем выше скорость резания.
Жёсткие сплавы, изготовляемые способом порошковой металлургии (методом прессования в формах измельченных железных порошков и последующего их спекания при больших температурах), именуют металлокерамиче-скими.
Базой металлокерамических жёстких сплавов являются зерна карбидов вольфрама (WC), титана (TiC) и тантала (ТаС), каковые связаны между собой кобальтом (прочным и пластичным материалом). Размеры зерен в большинстве случаев не более 1—2 мкм.
Кобальт заполняет весь обьем между зернами, не оставляя вакуумов (пор), и цементирует их.
Жёсткие сплавы подразделяют на три группы: вольфрамовые (В); титановольфрамовые (ТВ); титанотан-таловольфрамовые (ТТВ). Сплавы группы В складываются из карбидов вольфрама, связанных кобальтом. К данной группе относят сплавы марок ВК.З, ВК4, ВК6, ВК8 и др.
Тут буква В свидетельствует вольфрамовый; К — кобальт; цифра, следующая за буквой, содержание кобальта в . К примеру, сплав марки ВК8 содержит 8 карбидов и 92% кобальта вольфрама.
Жёсткие сплавы группы ТВ складываются из карбидов вольфрама и карбидов титана, связанных кобальтом. К данной группе относят сплавы марок Т5К.Ю, Т15К8, Т15К6, Т30К4.
Сплав марки Т15К6 содержит 15% карбидов титана, 6% карбидов и 79% кобальта вольфрама.
К третьей группе относят жёсткие сплавы марок ТТ7К12, ТТ10К8, ТТ20К9 и др., складывающиеся из карбидов вольфрама, карбидов титана, карбидов тантала, связанных кобальтом. Жёсткий сплав марки ТТ7К12 содержит 12% кобальта, 7% карбидов титана и карбидов вольфрама и 81% карбидов тантала.
Твердость металлокерамических жёстких сплавов образовывает 87—92 HRA. С повышением содержания кобальта твердость и износостойкость сплавов понижаются, но в один момент возрастают их прочность и вязкость.
Теплоустойчивость сплавов первой и второй группы образовывает около 1000 °С; сплавов третьей группы — 1050— 1100 °С.
Жёсткие сплавы группы В используют при обработке заготовок из чугуна, цветных металлов и их неметаллических материалов и сплавов (пластмасс, стеклопластиков и др.); сплавы группы ТВ — при обработке углеродистых и легированных сталей; сплавы группы ТТВ — при обработке труднообрабатываемых материалов, коррозионно-стойких и сплавов и жаропрочных сталей, титановых сплавов, при фрезеровании и черновом точении металлических заготовок. Выпускаются два типа твердосплавных пластин — для напаивания на корпуса и державки инструментов и для механического закрепления на них (последний вид крепления предпочтительный).
Назначение, форма, степень и размеры точности твердосплавных пластин установлены стандартом.
Минералокерамические жёсткие сплавы складываются из огнеупорных оксидов алюминия (А1203) либо циркония (Zr02), связанных стекловидным веществом. Эти сплавы, изготовляемые способом прессования порошков указанных оксидов с последующим их спеканием, имеют высокие твердость (91—92 HRA), теплоустойчивость (1300 °С) и износостойкость, но они весьма хрупкие.
Пара менее хрупкими являются керметы — жёсткие сплавы, у которых огнеупорные окислы связаны металлами (железом, никелем, титаном и др.), Минерало-керметы и керамику используют для чистового точения (со скоростью 4—5 м/с) заготовок с равномерным припуском; наряду с этим необходимым условием есть высокая жесткость технологической оснастки и станка.
Сейчас в качестве инструментальных материалов для лезвийного инструмента (резцов, сверл, фрез) используют монокристаллы природного бриллианта и поликристаллы кубического нитрида и синтетического алмаза бора (эльбора). В зависимости от исходного сырья, легирующих технологии и добавок производства приобретают разные виды эльбора, именуемые композитами.
Алмазные лезвийные инструменты используют для высокопроизводительной чистовой и получистовой обработки (со скоростью резания 5—10 м/с) сплавов и цветных металлов, неметаллических материалов и титана.
Лезвийные инструменты из эльбора применяют для чистовой обработки (со скоростью резания 0,7—1,7 м/с) закаленных легированных и закаленных инструментальных сталей. Такая производительность неосуществима при резании вторыми инструментальными материалами.
К примеру, при обработке резцами из эльбора скорость резания достигает 7—12 м/с, т. е. приближается к скорости шлифования.