Специальные виды кислородной резки
При простой кислородной резке, в то время, когда режущая струя направлена примерно нормально к поверхности металла, прорезается вся его толщина; тут преследуется цель отделить либо отрезать часть металла. Такая резка возможно названа разделительной.
Вероятен и второй метод применения режущей кислородной струи: она возможно направлена под малый углом к поверхности металла, практически параллельно ей (рис. 2, а).
В этом случае струя кислорода выжигает на поверхности металла канавку круглого сечения. Подобный способ именуется кислородной обработкой, время от времени кислородной строжкой либо кислородной вырубкой металла.
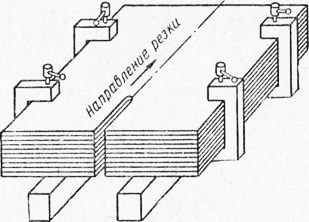
Рис. 257. Пакет страниц, подготовленный для резки
Рис. 258. Поверхности по окончании кислородной обработки
Для кислородной обработки используются особые резаки, производимые отечественной индустрией. Резак для ручной кислородной обработки типа РП-50 длиной 1200 мм весит 2,8 кг, имеет щиток для защиты руки, расположенной у тёплого металла, рычажный клапан для пуска режущего кислорода, три сменных сопла (рис.
3). Резак выбирает канавку шириной 15—50 мм, глубиной 2—20 мм со скоростью 1,5—10 м/мин, удаляя 1,0— 4,5 кг металла в 60 секунд. Расход кислорода равен 200—300 л на 1 кг удаленного металла.
Подобным резаком возможно выбирать на поверхности металла канавки круглого сечения, создавая как бы неотёсанную строжку (рис. 2, б). Повторный проход поверхности резаком со срезкой гребешков канавками сниженных размеров дает более чистую обработку.
При верной работе получается чистая и ровная поверхность канавок.
Рис. 3. Ручной резак для кислородном обработки
Кислородную обработку возможно уподобить механической обработке металла резанием, с заменой резца кислородным резаком. Соответственно процессом кислородной обработки возможно выполнить многие операции обработки резанием: строжку, обточку, расточку, нарезку неотёсанной резьбы и т. п., в то время, когда достаточно неотёсанной черновой обработки.
Вероятны кроме этого механизированные станки для кислородной строжки, обточки и т. п., требующие очень незначительной мощности для движения резака на протяжении обрабатываемой поверхности.
Рис. 4. Машина для огневой зачистки: 1 – ботинки с резаками; г – рычаги перемещения башмаков
Рис. 5. Установка автомобили при прокатном стане: 1 – прокатный стан; 2 – заготовка металла; 3 – машина для огневой зачистки: 4 — пульт управления
Рис. 6. Резка кислородным копьем
На данный момент использование на практике кислородной обработки скоро расширяется. Кислородная обработка отыскала достаточно широкое использование на металлургических фабриках для удаления и вырубки трещин, расслоений и других поверхностных недостатков в обжатых слитках.
Удаление производится не только вручную, но и механизированным методом, на особых автомобилях для огневой либо кислородной зачистки. В этом случае удаляются не отдельные недостатки, а целый наружный слой металла толщиной около 3 мм по всей боковой поверхности слитка.
Установленная в общем потоке перемещения машина для огневой зачистки имеет четыре башмака, на которых закреплены резаки для кислородной обработки. Любой резак выжигает канавку шириной около 36 мм и глубиной около 3 мм.
Тёплый слиток, имеющий температуру 950—1100° С, проходит через машину со скоростью 20—40 м/мин. Часовой расход кислорода в машине достигает 3000—4000 м3.
Необычным методом есть резка кислородным копьем, которое представляет собой толстостенную трубку достаточной длины, присоединенную к стволу либо рукоятке. Трубка скоро сгорает на протяжении работы и исходя из этого обязана легко и комфортно заменяться новой.
Внутренний диаметр трубки 2—4 мм, наружный 8—10 мм. При через чур громадном внутреннем диаметре в трубку закладывают металлические прутки, уменьшающие свободное сечение трубки и увеличивающие количество сгорающего металла копья.
Процесс резки кислородным копьем содержится в прожигании металла струей кислорода, проходящей через металлическую трубку, прижатую свободным финишем к прожигаемому металлу. Резка производится без применения газового подогревательного пламени, которое заменяется достаточно стремительным сгоранием металла самой трубки-копья до 0,5—1 м/мин.
Начинается резка с подогрева места начала реза на металле либо, что эргономичнее, с подогрева финиша копья, к примеру сварочной горелкой либо дугой. При пропускании кислорода финиш копья скоро загорается; предстоящий подогрев не нужен, и возможно приступить к резке.
После этого копье легко прижимают к металлу и скоро углубляют в него со скоростью 0,15—0,40 м/мин, выжигая отверстие круглого сечения с ровными стенками.
Расплавленный шлак выдувается из отверстия наружу избыточным кислородом и образующимися газами. При большой глубине прожигаемого отверстия нужно ставить изделие наклонно, облегчая вытекание шлаков из отверстия под действием силы тяжести.
Копьем возможно резать не только сталь, но и чугун, цветные металлы, затвердевшие шлаки, бетон, каменные породы и т. п. В аналогичных случаях резка происходит под тепловым действием горящего копья. Диаметр прожигаемого отверстия в большинстве случаев образовывает 20—60 мм, глубина его возможно доведена до трех метров. Давление кислорода на входе копья равняется .5—7 ати, расход кислорода 30—60 м3/ч.
Расход трубки скоро растет с глубиной отверстия.
Рис. 7. Схема кислородно-флюсовой резки: 1 — флюсовый бункер; 2 — пружинная подвеска бункера; 3 — вибратор-встряхиватель бункера, трудящийся от струи режущего кислорода; 4 — предохранительный клапан; 5 — флюсовый инжектор; в — кислородный редуктор, питающий флюсовый бункер; 7 — резак
Кислородное копье находит разное использование, к примеру прожигание отверстий, леток в металлургических печах, шпуров в стальных блоках и козлах для подрыва их взрывчаткой, отверстий в бетоне и т. п. При резке кислородным копьем искры и брызги шлака разбрасываются на пара метров, что приводит к необходимости защиты рабочих и устранения опасности пожара.
Разглядим особый процесс кислородно-флюсовой резки, довольно часто дающий прекрасные результаты при резке металлов, для которых простой способ кислородной резки непригоден либо совсем негоден. Очень благоприятным для кислородной резки сочетанием физико-химических особенностей владеют технически чистое железо и простая низкоуглеродистая сталь, каковые с успехом режутся кислородом.
Но многие легированные стали не хорошо поддаются простой кислородной резке, к примеру все стали со большим содержанием хрома, что при горении стали образует тугоплавкую окись хрома Сг203, преграждающую доступ кислорода к поверхности металла. К таким сталям принадлежат хромоникелевые нержавеющие и жаростойкие стали.
Для резки чугуна, цветных металлов, для которых использование кислородной резки не нужно, создан особый процесс кислородно-флюсовой резки и создана нужная аппаратура. Сущность этого процесса пребывает в том, что вместе с режущим кислородом в зону резки вдувается порошкообразный флюс, вносимый во взвешенном состоянии струей режущего кислорода.
Флюс, подаваемый в зону резки, состоит в основном из порошка железного железа. Сгорая в струе кислорода, металлический порошок дает дополнительное количество тепла, расплавляющее тугоплавкие окислы.
Окислы железа, образующиеся при сгорании металлического порошка, сплавляясь с окислами разрезаемого металла, образуют более легкоплавкий и жидкотеку-чий шлак, легче сдуваемый с поверхности металла и открывающий к ней доступ кислорода. Для получения флюса к металлическому порошку примешивают порошкообразные флюсующие добавки, облегчающие вытекание и плавление тугоплавких окислов из полости реза.
Используются кроме этого флюсы, по большей части складывающиеся из двуокиси кремния Si02, к примеру кварцевого песка. Количество флюсующих добавок зависит от состава разрезаемого металла.
Для кислородно-флюсовой резки нужно иметь особую аппаратуру: флюсопитатель и особый кислородный резак с приспособлениями для подачи флюса. Обычный флюсопитатель, производимый отечественной индустрией, имеет маленькие размеры и весит около сорока килограмм.
Расход флюса при резке особых сталей колеблется от 1—2 кг для толщины 10 мм до 10—14 кг для толщины 200 мм на 1 пог. м реза. Флюс расходуется довольно экономнее при громадных толщинах.
Для малых толщин рекомендуется использовать пакетную резку, выбирая оптимальную неспециализированную толщину металла. Кислородно-флюсовый метод разрешает удачно резать особые стали, а также нержавеющие и жаростойкие, и цветные металлы и чугун.
Недочётом метода есть большой расход флюса, еще достаточно дорогого.