Структура технологической операции
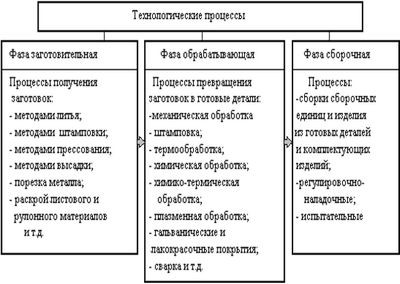
В серийном производстве либо при изготовлении важных подробностей по окончании разработки технологического маршрута детально проектируют каждую операцию. Для каждой операции устанавливают нужное число переходов и их рациональную последовательность, выбирают рациональные приемы обработки, назначают припуски на обработку каждой поверхности, определяют нормы и технологические режимы времени на операцию.
Наиболее неотъемлемой частью каждой операции, определяющей ее структуру, есть переход. Технологическим переходом именуют законченную часть технологической операции, делаемую одними и теми же средствами технологического оснащения при постоянных установке и технологических режимах.
Под установкой знают часть технологической операции, делаемой при неизменном закреплении обрабатываемой заготовки либо собираемой сборочной единицы. Наровне с технологическим переходом ответственную составляющую часть операции имеет вспомогательный — законченная часть технологической операции, складывающаяся из действий человека либо оборудования, которая не сопровождается трансформацией особенностей предмета труда, но нужна для исполнения технологического перехода.
Примерами запасного перехода являются такие действия слесаря, как закрепление заготовки, смена инструмента и др.
Наровне с технологическими и запасными переходами элементами операции являются вспомогательный ход и рабочий. Рабочим ходом именуют законченную часть технологического перехода, складывающуюся из однократного перемещения инструмента относительно заготовки, сопровождающуюся трансформацией формы, размера, свойств и качества материала заготовки.
Запасным ходом именуют законченную часть технологического перехода, нужную для подготовки рабочего хода.
последовательность и Число технологических и запасных переходов, вспомогательных ходов и рабочих определяют структуру операции. Эти элементы определяют затраты времени и средств на операцию.
Затраты времени на операцию принято характеризовать штучным временем. Под штучным временем знают отношение времени цикла технологической операции к числу в один момент изготовляемых изделий.
В случае если на данной операции обрабатывают одну заготовку, то штучное время определяется временем ее обработки. В случае если же, к примеру, обрабатывают пакет шаблонов либо скоб, то штучным временем будет частное от деления времени цикла операции на число в один момент обрабатываемых заготовок.
Штучное время складывается из главного и запасного времени. Главное время — это часть штучного времени, затрачиваемая на трансформацию предмета труда и на последующее определение состояния этого предмета.
Так, в штучное время входят затраты времени и на контроль как в ходе обработки, так и по окончании ее окончания. Вспомогательное время — это та часть штучного времени, которая затрачивается на исполнение приемов, снабжающих контроль и предмета последующее изменение труда его состояния.
Из определения главного и вспомогательного времени видно, что они тесно связаны с характером исполнения технологического и вспомогательного переходов. Исходя из этого громадную роль в уменьшении штучного времени играется последовательности и выбор числа технологических, вспомогательных и контрольно-измерительных переходов.
Для уменьшения главного времени принципиально важно верно выбрать способ обработки, технологическое оснащение, шире применять механизированный инструмент, станочные способы обработки.
Для уменьшения вспомогательного времени направляться рационально строить приёмы обработки и вспомогательные переходы. направляться применять эргономичные приспособления, каковые облегчают стремительную и правильную установку заготовки относительно инструмента.
Довольно часто несложные приспособления позволяют быстро сократить вспомогательное время и основное в следствии совмещения во времени технологических и запасных переходов. Такое совмещение разрешает использовать одну из самых идеальных и производительных форм обработки — параллельную обработку.
Параллельно возможно обрабатывать пара заготовок либо пара поверхностей на одной заготовке.
В структуре операции кроются главные резервы увеличения производительности труда слесарной обработки. И эти резервы смогут быть реализованы на базе изобретательства и рационализации.
Исходя из этого передовые слесари-инструментальщики довольно часто разрабатывают уникальные режущие, контрольно-приспособления и измерительные инструменты, каковые быстро повышают производительность и качество обработки. Затраты времени на изготовление и разработку таких устройств всецело окупаются при их применении.
Они уменьшают затраты физических сил и утомляемость, делают работу более правильной при меньшем числе переходов а также операций.
Припуском именуют слой материала, удаляемый с поверхности заготовки в целях успехи заданных особенностей обработанной поверхности. Припуск направляться назначать в соответствии с рекомендациями, каковые приводятся в справочниках.
Недостаточные припуски приводят к браку, избыточные — к громадным неоправданным затратам времени на их удаление.
Технологические режимы для разных способов обработки характеризуются разной совокупностью параметров. При обработке резанием режим определяется скоростью резания, глубиной и подачей резания.
При операции склеивания режим определяется температурой, временем выдержки, давлением и т. д. Технологические режимы выбирают по справочной литературе в соответствии с конкретными условиями обработки.
Последним этапом проектирования технологического процесса обработки есть расчет норм времени на каждую операцию.
При изготовлении некоторых подробностей приходится делать отдельные сложные операции, от которых зависит уровень качества изделия либо безопасность труда. В таких случаях применяют маршрутно-операционное описание технологического процесса.
В нем приводят сокращенное описание операций в маршрутной карте в последовательности их исполнения с полным описанием сложных операций в других технологических документах.
При разработке технологических процессов применяют данные базисную (чертеж подробности, программа выпуска), руководящую (стандарты, инструкции, документы по безопасности труда и др.) и справочную (каталоги, паспорта, справочники, описания прогрессивных методов и способов обработки, контроля и др.).
Для реализации созданного технологического процесса его описание нужно довести до каждого рабочего места. Дабы не было неточностей либо недопонимания, его содержание нужно зафиксировать в стандартных документах.
В качестве таких документов используют технологические и операционные карты. Технологическая карта содержит все нужные для обработки сведения: наименование карты, номер и наименование чертежа подробности, число подробностей в партии, номера операций, модели станков, типы и наименование приспособлений и инструментов, наименования измерительных инструментов, технологические режимы, последовательности переходов и их наименование, нормы времени на операции.