Термическая и химико-термическая обработка стали
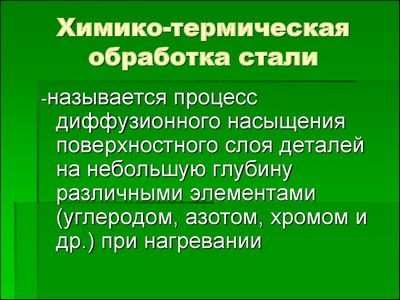
Нагревая сталь до определенной температуры и охлаждая ее с определенной скоростью, возможно значительно изменить ее структуру и, следовательно, ее свойства. Тепловая обработка сталей в жёстком состоянии, при которой под влиянием скорости охлаждения и температуры нагрева они изменяют способность и свои свойства поддаваться механической обработке, именуется их термической обработкой.
К термической обработке относятся такие процессы как отжиг, нормализация, закалка, старение и отпуск.
Дадим краткую чёрта этих процессов.
Отжиг представляет собой медленный нагрев стали до температуры 750—880° с выдержкой при данной температуре и с последующим медленным охлаждением вместе с нагревательной печью. Отжиг стали усиливает структуру и снимает ее внутренние напряжения, понижает ее твердость, облегчая механическую обработку.
Нормализация представляет собой высокий отпуск и закалку при температуре 660—720°. Она увеличивает прочность стали и усиливает ее обрабатываемость.
Приобретаемые затем вида обработки свойства стали содействуют образованию более чистой поверхности по окончании механической обработки. Нормализация как бы готовит подробность к последующей закалке, уменьшая возможность деформаций и появления трещин.
Назначение закалки пребывает в сохранении у холодной стали той структуры, которую она имеет при больших температурах. Сохранение у стали структуры больших температур вероятно лишь при таком стремительном ее охлаждении, на протяжении которого структура еще не успеет превратиться в структуру холодной стали.
Сталь с таковой насильно закрепленной структурой владеет высокой большой прочностью и твёрдостью. Температура нагрева под закалку для разных сталей находится в пределах от 750 до 1300°, а скорость охлаждения достигает до 300° в секунду.
Охлаждение на протяжении закалки производится или в воде, или в масле и время от времени в струе воздуха. Чем больше углерода и легирующих элементов в стали, тем выше температура нагрева и тем медленнее скорость охлаждения при закалке.
Не считая простой закалки сейчас все шире начинает использоваться изотермическая закалка. Такая закалка пребывает в нагреве подробности до закалочных температур и ее охлаждении сперва в тёплой закалочной среде, нагретой до температуры 320—370°, а после этого в охлаждении вне данной среды с нужной скоростью.
В этом случае закалочной средой помогает щелочь. Изотермическая закалка дает возможность приобрести большую прочность закаленной стали и, во многих случаях, избежать следующей операции — отпуска.
Отпуск стали пребывает в повторных ее нагревах от 180 до 580° (в зависимости от марки и вида стали, и заданной твердости), в продолжительных выдержках при этих температурах и в медленном охлаждении. Данный вид термической обработки разрешает перевести насильственно закрепленную при закалке структуру больших температур в более устойчивое состояние, ликвидирует появившиеся при закалке внутренние напряжения и, в большинстве случаев, увеличивает вязкость и пара снижает твердость стали.
Исключение составляют высоколегированные инструментальные стали, у которых по окончании отпуска твердость увеличивается.
Отпуск высокоуглеродистых и легированных сталей возможно произведен не только при температурах 180—580°, но и при температурах ниже нуля. Отпуск при низких температурах либо обработка холодом производится охлаждением подробностей до температуры минус 100—130° и выдержкой их при данной температуре в течение определенного времени.
На протяжении обработки холодом в стали происходят те же процессы, что и при высокотемпературном отпуске. Для охлаждения стали используется жидкий азот либо жёсткая углекислота (сухой лед).
Старение стали активизирует процесс перехода структуры закаленных сталей в более устойчивое состояние и снимает их внутренние напряжения. На протяжении перехода к более устойчивой и лишенной внутренних напряжений структуре стали, у нее изменяется количество «, подробность теряет размеры.
В инструментальном производстве процесс старения имеет особенно громадное значение, поскольку он, ликвидируя’ эти напряжения, гарантирует в последующем формы и сохранность размеров правильных инструментов.
Процесс старения влияет и на последующую обработку стали. Не прошедшие старения кое-какие инструментальные стали, как к примеру, стали марок ХВГ, ХВ5 и другие, не хорошо шлифуются: при шлифовании на их поверхности легко появляется сетка поверхностных трещин.
Старение ведется в масле, нагретом до 130—160° с выдержкой изделия при таковой температуре в течение 24—48 часов.
Особенные виды термической обработки, при которых изменяется состав поверхностного слоя стали, именуются химико-термической обработкой. Ко мне относятся: цементация, нитроцементация, азотирование и другие процессы.
Цементация стали используется чтобы повысить содержание углерода в ее поверхностном слое. При цементации подробности помещают в металлический коробку, пересыпают особым веществом — карбюризатором,— содержащим углерод, и нагревают.
В качестве карбюризатора возможно применен древесноугольный порошок с добавлением соды и мела. На протяжении продолжительного нагревания в печи при температуре 920—940° поверхность подробности насыщается углеродом на глубину 1,0—2,5 мм.
Так по окончании цементации подробность состоит как бы из двух неспешно переходящих приятель в приятеля сталей: в — вязкая и мягкая низкоуглеродистая сталь, а снаружи высокоуглеродистая сталь. Цементированные подробности возможно подвергнуть закалке.
Затем их поверхность возьмёт высокую твердость, а сердцевина останется мягкой.
Карбюризаторами при цементации смогут быть не только жёсткие вещества: цементация может производиться в расплавленных науглераживающих солях и тогда ее именуют жидкостной цементацией либо в науглераживающих газах и тогда ее именуют газовой цементацией.
Одновременное насыщение поверхности подробностей азотом и углеродом, создаваемое в газовой среде, именуется нитро цемент а-Д и е й либо цианированием. Нитроцементация осуществляется в особой установке.
Карбюризатором в этом случае помогает смесь пиролизного газа и аммиака, а процесс протекает-при температуре 530—550°. Таковой метод нитроцементации носит название низкотемпературного.
Он разрешает не только сохранить твердость закаленных быстрорежущих инструментов, но и существенно ее повысить в поверхностном слое.
Газовая нитроцементация может производиться и при температуре 750—850°, в то время, когда совмещается нагрев подробности под закалку с процессом нитроцементации. Таковой процесс именуется высокотемпературной газовой нитроцементацией.
Данный метод используется при изготовлении подробностей из конструкционных сталей.
Но процесс газовой нитроцементации требует сложных установок. Исходя из этого в инструментальных цехах машиностроительных фабрик довольно часто используется нитроцементация в жёсткой либо жидкой среде.
Нитроцементация в жёсткой среде и жидкостная нитроцементация также будут быть низкотемпературной и высокотемпературной.
Азотирование воображает.процесс химико-термического насыщения поверхностного металлического слоя азотом. Процесс азотирования осуществляется при температуре 480—600° методом нагрева, медленного охлаждения и выдержки подробностей.
В инструментальном деле азотирование используется при изготовлении измерительных инструментов сложной формы.
Такие виды обработки стали повышают поверхностную твердость и износостойкость изготовленного из нее режущего и измерительного инструмента и некоторых подробностей приспособлений, трудящихся на истирание.