Краткие сведения по истории древесномассного производства
До века и середины единственным сырьем для производства бумаги в Европе было тряпье. Возросшая потребность в бумаге, в особенности по окончании изобретения печатного пресса, привёдшего к значительному удешевлению газет и книг, не могла быть удовлетворена благодаря ограниченных ресурсов этого вида сырья.
Дефицит тряпья конечно привела к сильному удорожанию его. Вследствие этого начались поиски нового сырья, более недорогого и распространенного.
Таким сырьем явилась древесина.
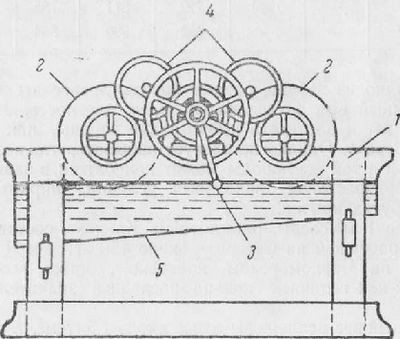
Рис. 1. Первый дефибрер: 1 — рама; 2 — дефибрерный камень; 3 — рукоятка для вращения камня; 4 — шестеренная передача от рукоятки к камням; 5 — ванна
Громадное значение для предстоящего развития бумажного производства купил изобретенный в середине XIX века метод получения древесной массы методом истирания древесины на вращающемся камне, обильно смачиваемом водой. Одна из первых конструкций аппарата, так именуемого дефибрера, продемонстрирована на рис.
1. Данный дефибрер имел маленькой камень диаметром 500 мм и шириной 300 мм. На рис.
2 продемонстрирован пятипрессовый дефибрер более поздней конструкции с механическим прижимом древесины к вращающемуся камню.
Древесину в виде маленьких бревен загружали в прессовые коробки; прижим их к вращающемуся камню достигался при помощи особой чугунной плиты, прикрепленной к зубчатой рейке, перемещавшейся в прессовой коробке над камнем. подъём и Опускание плиты осуществлялись через нескончаемую цепь, вращавшую шестеренки, каковые со своей стороны имели зацепление с зубчатой рейкой.
У первых цепных дефибреров прижимная плита опускалась и прижималась через цепную передачу при вращении вручную маховика, что приводило к большим затруднениям в эксплуатации автомобили. Позднее привод цепного дефибрера был механизирован, что существенно облегчило обслуживание дефибреров.
Показавшийся с введением дефибреров новый, относительно недорогой полуфабрикат — древесную массу в связи с острым недочётом сырья для бумажного производства стали обширно использовать без проверки его качества, и скоро обнаружилось, что бумага, содержащая лишь древесную массу, получалась весьма не сильный, относительно быстро желтела, становилась хрупкой, ломкой и негодной для долгого хранения. Эти недочёты усиливались тем, что древесная масса не подвергалась предварительному сортированию.
В следствии было нужно ограничиться применением маленького количества древесной массы для производства лишь низких сортов бумаги. Все это продемонстрировало, что древесная масса не имеет возможности заменить тряпичного волокна в бумаге всех видов и ее возможно использовать только в пределах 25— 50% в композиции для сортов бумаги, не требующих долгого хранения (газетной и т. п.).
Рис. 2. Пятипрессовый дефибрер: 1 — дефибрерный камень; 2 — чугунная плита; 3 —зубчатая рейка; 4— прессовая коробка; 5 — нескончаемая цепь; 6 — шестеренки
Последующие изучения продемонстрировали, что тряпичное волокно с успехом возможно заменено волокнами целлюлозы, поскольку они более близки по своим особенностям к волокнам, взятым из тряпья.
В древесной массе, к примеру из еловой древесины, целлюлозы содержится лишь около 55%, а другое количество составляют вещества неволокнистые (лигнин, сахар), присутствие которых и вызывает с течением времени понижение и пожелтение бумаги ее качества.
В будущем, с усовершенствованием дефибреров, другого оборудования и сортировок, производство древесной массы все более развивалось. На данный момент древесная масса есть наровне с целлюлозой самый распространенным полуфабрикатом, входящим в состав бумаги большинства сортов (газетной, печатной, писчей и др.) в пределах от 30 до 90%.
Производительность первых древесномассных фабрик составляла 1—2 т в день, а современные фабрики производят ежесуточно пара сот и до тысячи тысячь киллограм отличной по качеству древесной массы. Первые дефибреры были производительностью менее 1 т в день, а современные дают в день до 50 и более тысячь киллограм древесной массы.
Известна древесная масса трех видов:
а) белая, получающаяся при механическом истирании древесины на дефибрерах с последующим ее сгущением и сортированием;
б) бурая, получающаяся кроме этого методом истирания на дефибрерах древесины, предварительно пропаренной в особых котлах, и
в) химическая, вырабатываемая на дефибрерах из балансов, предварительно обработанных химикалиями.
Помимо этого, древесная масса получается методом измельчения балансов в щепу, пропарки ее и истирания на особых аппаратах (быстроходных рафинерах, дефибраторах и др.).
Бурая древесная масса владеет пара большей механической прочностью и идет на изготовление обёртки и бурого картона.
На рис. 3 продемонстрирована схема производства древесной массы. Балансы в навигационный период сразу после окорки поступают по совокупности транспортёров и конвейеров либо по гидролоткам в дефиб-перный отдел.
Зимой балансы поступают на производство не с воды, а с лесной биржи — из куч либо штабелей, в которых хранят требуемые запасы древесины.
Рис. 3. Схема производства древесной массы
Подача балансов до завода гидравлическим методом имеет последовательность преимуществ если сравнивать с подачей транспортерами.
При транспортировке конвейерами либо транспортерами, и при хранении, в особенности в кучах, и наличии у бревен размочаленных торцов древесина загрязняется. Зимний период бревна промерзают, поскольку вода, содержащаяся в древесине, при температуре воздуха ниже 0° преобразовывается в лед, а переработка на дефибрерах промерзшего баланса нежелательна, о чем подробнее будет сообщено ниже.
Поступление древесины к древесномассному заводу по гидравлическим лоткам (цементным, древесным либо из листового железа) содействует очистке бревен от приставшей к ним грязи, а зимой — стремительному оттаиванию бревен, что положительно оказывает влияние на работу дефибреров.