Крепление режущей части инструмента
При напайке инструмента на высокочастотных установках нельзя крепить пластинки к корпусу проволокой, поскольку в местах касания проволоки на них смогут появиться трещины.
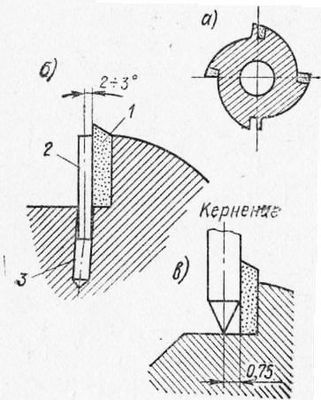
Рис. 1.
В качестве флюса применяют обезвоженную буру, борный их смеси и ангидрид. При пайке режущих инструментов, оснащенных жёсткими сплавами группы ТК либо ТТК, для лучшего растворения окислов титана во флюс вводят фториды кальция, натрия, калия либо лития.
Создан флюс, содержащий 69…73,2% буры, 21…22,8% фтористого кальция и 5… 10% борного ангидрида. Для улучшения производительности и повышения пайки ее качества используют припой в виде пилюль, что складывается из 75…80% припоя и 20…25% флюса.
Пайка режущих инструментов производится в печах и с нагревом токами высокой частоты. Пайка в печах с безокислительной средой — более прогрессивный метод, чем пайка в простых печах.
Электрическая печь складывается из камеры нагрева, где поддерживается температура 100° С, камеры охлаждения, наружные стены которой охлаждаются проточной водой, выпускной камер и приёмной. Для в печи безокислительной газовой среды употребляется очищенный от примесей водород или азот, полученный пои диссоциации аммиака, печь снабжена контрольной’аппаратурой.
Пайка с индукционным нагревом на высокочастот-ных установках — самый распространенный и высокопроизводительный метод. При изготовлении многочисленных партий однотипных инструментов их помещают в многоместный индуктор и реализовывают постоянную напайку режущих пластинок с подачей инструментов без снятия напряжения с индуктора.
При маленьких партиях инструментов напайку пластинок создают в одноместных индукторах. Форма индуктора зависит от размеров и формы напаиваемого инструмента.
Так, в случае если корпус инструмента имеет открытые пазы (дисковые фрезы, ножи, резцы и т. д.), то пластинки напаиваются в любой паз раздельно в петлевых индукторах. В этом случае опорную плоскость паза зуба фрезы посыпают флюсом и подогревают в индукторе до температуры 800…850 °С.
По окончании расплавления флюса поверхность паза очищают от окислов и снова посыпают флюсом, на что укладывают припой. Слой припоя снова посыпают флюсом и сверху кладут режущую пластинку.
После этого зуб фрезы вводят в индуктор для окончательного нагрева до температуры плавления припоя. По окончании расплавления при- i поя железным стержнем исправляют положение пластинки в пазу и прижимают ее к опорным плоскостям.
В случае если корпус инструмента имеет открытые и полузакрытые пазы с расстоянием между зубьями более 20 мм, то напайку пластинок создают в любой паз раздельно в петлевом либо круглом двухвитковом индукторе при эксцентричном размещении корпуса для личного нагрева каждого зуба. В случае если расстояние между зубьями менее 20 мм, .то напайку пластинок к корпусу реализовывают в один момент на всех зубьях, наряду с этим корпус устанавливается в индукторе в вертикальном положении.
По окончании напайки инструменты охлаждают в сухом пес-,е нагретом до температуры 150-200 °С, либо в камерной печи. остатки и Окалина фтса удаляются очисткой.
Крайне редко напайку пластинки совмещают с термической обработкой корпуса инструмента, поскольку повторный нагрев инструмента под закалку снижает прочность паяного шва. В случае если напайка пластинок на корпус производится при нагреве токами высокой частоты, то сразу же по окончании ее окончания рабочую часть инструмента прогревают в индукторе до температуры закалки.
Затем ее охлаждают в расплавленной селитре так, дабы пластинки пребывали на зеркале ванны. При охлаждении рабочей части корпуса до температуры 500 °С инструмент всецело погружают в ванну, а после этого подвергают отпуску.
Рис. 2. Типы индукторов.
Контроль качества пайки реализовывают внешним осмотром, и посредством особых приборов и инструментов. При осмотре контролируют правильность размещения пластинки на державке, удостоверяются в отсутствии неотёсанных забоин и завалов на режущих кромках, выколов и трещин.
Небольшие недостатки пайки тяжело найти невооруженным глазом, исходя из этого паяные соединения осматриваются посредством микроскопа КМ-60. Для обнаружения трещин употребляется метод и люминесцентный метод цветных красок.
Крепление ножей к корпусу фрезы. Слесарю-инструменталыцику значительно чаще приходится заниматься сбор, кой торцевых фрез.
Стандартами предусмотрены следующие типы крепления ножей к корпусу фрезы: плоским клином; посредством плоского клина и рифлений; рифельно-клиновое (нож имеет рифли и сделан в форме клина).
Крепление плоским клином есть достаточно несложным. Надежное соединение в этом случае достигается за счет плотного соприкосновения сопряженных поверхностей зуба, паза и клина в корпусе.
Рифельное крепление — одно из самых распространенных. Рифления разрешают создавать перестановку зубьев на одно либо пара делений, что позволяет регулировать их положение.
Но благодаря неравномерного износа зубьев, в особенности с пластинками из жёсткого сплава, и принудительного выдвижения ножей на одно либо пара делений возрастает припуск на переточку и усложняется процесс заточки. Серьёзным недочётом есть кроме этого то, что основание зуба, опираясь на боковые плоскости рифления, не имеет надежной опоры.
Последовательность конструкций торцевых фрез (фрезерных головок), отыскавших широкое использование при скоростном фрезеровании, предусматривает возможность раздельного затачивания вставных ножей с последующей установкой их в корпусе фрезы, что в некоторых случаях может и не сниматься со станка. Необходимость в раздельной заточке ножей торцевых фрез вызывается отсутствием соответствующих заточных станков.
По мере потребителей фрез и обеспечения изготовителей особыми заточными станками потребность в раздельной заточке ножей отпадет.
Рис. 3. Сборные торцевые фрезы.
Нож имеет правильную призматическую форму. Опорная и противоположная ей плоскости обрабатываются строганием.
Резцовая державка не должна выступать из корпуса. Ножи крепятся в корпусе фрезы не меньше чем двумя винтами.
Высота корпуса принимается таковой, дабы обеспечивались достаточная опорная поверхность для ножей и размещение нужного количества винтов для их крепления. головки и Концы болтов заклиниваются.
Фреза открытого типа, у которой ножи смогут вставляться и выниматься в радиальном и осевом направлениях, продемонстрирована на рис. 2, а. У фрезы открытого типа вынуть и засунуть ножи вероятно лишь в осевом направлении.
Рис. 4. Приспособление для сборки фрез (а) и установка ножей в корпусе (б).
Сборка ножей с корпусом производится в приспособлении, которое приведено на рис. 3, а. На основании приспособления закреплены гайками и болтами стойка и колодка. Колодка помогает направляющей для губок, каковые перемещаются на протяжении колодки при повороте винта.
В губках установлены ролики, являющиеся подставкой для корпуса фрезы. Корпус фрезы с конусной оправкой закрепляется в шпинделе приспособления посредством штревеля и конусной втулки.
Благодаря наличию подшипников фреза легко поворачивается около оси корпуса приспособления. Подтяжка подшипников производится гайками.
Развертывание отверстий под сухари, нарезка резьбы под винты, установка новых ножей либо смена изношенных, крепление их винтами и сухарями производятся при горизонтальном размещении корпуса приспособления (рис. 103,6).
Для извлечения сухарей из гнезд используют железный прут с резьбой на финише. Его ввертывают в резьбовое отверстие сухаря и, ударяя выколоткой по пруту, сухарь извлекают, по окончании чего изношенный нож легко вынимается.
Крепление ножей в корпусе фрезы производится следующим образом. Нож от руки вставляют в торцевое отверстие корпуса на определенную глубину, а после этого в эти же отверстия со стороны образующей корпуса устанавливают сухари, причем так, дабы ножей и рифли сухарей вошли в зацепление между собой.
Для обеспечения надежного крепления ножей сухари досылаются ударами ручника по оправке. Дабы в ходе эксплуатации фрез не ослабло крепление ножей, сухари закрепляют винтами посредством пневматической отвертки.
Разборка фрез производится в обратной последовательности. Корпус, приспособления при разборке кроме этого находится в горизонтальном положении.
Крепление алмазов. К креплению алмазов в державках резцов предъявляются следующие требования: жёсткость и прочность крепления; возможность стремительной разборки и сборки резца; минимальный нагрев бриллианта при креплении.
Существуют два метода крепления бриллианта— пайка и механическое крепление.
Для крепления бриллианта пайкой в державке резца фрезеруется закрытый паз, в который устанавливается ‘раненый бриллиант (рис. 4,а).
После этого державка крепится в нескольких точках и бриллиант запаивается серебряным припоем ПСР-59Кд. По окончании пайки державка зачищается, езцы с напаянным бриллиантом отличаются малыми и простотой конструкции габаритами.
Помимо этого, данный спо соб крепления разрешает применять бриллианты малых размеров. К недочётам его относятся нежелательный нагрев бриллианта до большой температуры и сложность разборки резца при переточках.
Рис. 4. Крепление алмазов.
Метод механического крепления бриллианта в корпусе резца лишен этих недочётов. Для закрепления бриллианта (рис.
4,6), основание которого не шлифуется, изготовляют подушку — в пресс-форму засыпают порошковую смесь, складывающуюся из 80% меди, 15% свинца и 5% олова. Поверх данной смеси укладывают бриллиант с предварительно обработанными передними поверхностями и смесь прессуют под давлением 150 кгс/мм2. Спрессованный брикет вместе с бриллиантом спекают при температуре 650° С. Смесь наряду с этим дает малого усадку, но отпечаток по окончании спекания сохраняет