Методы проверки микрометрических инструментов.
Проверка точности показаний микрометров осуществляется концевыми мерами длины 5-го разряда через каждые 5 мм шкалы и через 0,12 мм, т. е. через четверть оборота микровинта.
Плоскостность их измерительных поверхностей осуществляют контроль посредством плоских либо плоскопараллельных интерференционных стеклянных пластин. Отклонение от плоскостности (в зависимости от класса точности микрометров) колеблется в пределах 0,6…0,9 мкм, либо равняется трем интерференционным полосам для белого света не учитывая расстояния 0,5 мм от краев измерительной поверхности.
Параллельность измерительных поверхностей у микрометров с верхним пределом измерений до 100 мм контролируют плоскопараллельными стеклянными пластинами. Набор складывается из четырех пластин, размеры Н которых отличаются один от другого на величину перемещения микровинта при его повороте на ‘Д оборота.
По числу интерференционных полос на поверхностях контакта и по их обоюдному размещению определяют настоящее отклонение от параллельности.
Для проверки микрометров громадных размеров вместо отдельных плоскопараллельных стеклянных пластин используют набор их, составленный в виде блоков, в каждом из которых имеются две пластины и одна концевая мера.
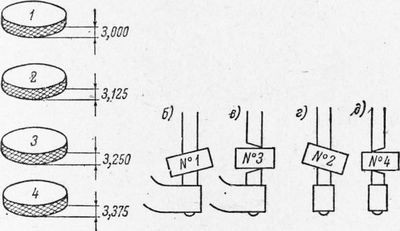
Рис. 1. Ремонт микрометра.
Микрометры с пределами измерения, превышающими 100 мм, осуществляют контроль посредством четырех особых штихмасов, размеры которых кроме этого отличаются один от другого на величину, соответствующую XU оборота микровинта. Каждым штихмасом создают диагностику в четырех положениях, поворачивая его любой раз около оси на 90°.
ремонт и Регулировка микрометров. При несовпадении нулевых шкалы шкалы барабана и штрихов стебля, и при ослаблении винта нужна регулировка микрометров.
При износе измерительных микрометрического винта и поверхностей микрометра и при ослаблении трещотки создают ремонт инструмента. При маленьком износе измерительные поверхности пасса и микрометров-метров (от 0 до 100 мм) доводятся в один момент посредством мерных цилиндрических притиров.
Набор их складывается из четырех притиров, различающихся по толщине на 0,125 мм. Торцевые рабочие плоскости притиров должны быть строго параллельны.
Доводку реализовывают в следующей последовательности. Сначала измерительные поверхности доводят притиром до получения их взаимопараллельности.
Но наряду с этим не обеспечивается перпендикулярность поверхностей к оси шпинделя, вероятнее они будут пара наклонны. Потом доводку создают притиром, что на 0,25 мм больше притира, исходя из этого при зажиме притира шпиндель провернется на пол-оборота, т. е. случится перекос и кантовка уменьшится.
После этого поверхности микрометра попеременно доводят притирами. По окончании многократной доводки всеми притирами смогут быть достигнуты перпендикулярность и параллельность поверхностей к оси шпинделя.
Рис. 2. Доводка шпинделя микрометра.
В то время, когда в ремонт поступают микрометры с таким износом измерительных поверхностей, что выявляется посредством угольника либо лекальной линейки, реализовывают пятки и раздельную доводку шпинделя. Торец шпинделя доводят в особом приспособлении.
Оно складывается из плиты, цанги, в которую вставляется шпиндель микрометра, и зажимного кольца, предназначенного для закрепления шпинделя в цанге. Нижнюю плоскость плиты доводят строго перпендикулярно относительно оси отверстия.
Шпин дель микрометра вставляют в цангу так, дабы его то рец возвышался над плоскостью плиты на 0,03…0,04 мм и по окончании закрепления зажимным кольцом доводят. Об работанный шпиндель ввертывают в микрометр и при ступают к доводке поверхности пятки.
Пятку доводят в собранном виде посредством приспособления, представляющего собой диск, выполненный за одно целое с цангой. Диск установлен по скользящей посадке на шпиндель микрометра и закрепляется кольцом.
Опорная поверхность диска доведена строго перпендикулярно оси отверстия. По окончании закрепления и установки диска на шпинделе микрометра приступают к доводке пятки; наряду с этим пасту наносят лишь на одну рабочую сторону притира, а другую шепетильно промывают и смазывают узким слоем раствора стеарина в бензине.
Рис. 3. Приспособление для доводки винтов микрометров.
Контроль обработанных измерительных поверхностей осуществляется интерференционным методом посредством комплекта плоскопараллельных стеклянных пластин. Инструмент обезжиривают в бензине, шепетильно протирают и на доведенную поверхность накладывают стеклянную пластину.
Легко прижав пластину к поверхности, замечают световые полосы, по которым и делают выводы о качестве доводки.
Для доводки поверхностей микрометрических винтов микрометров с пределом измерения 150…800 мм слесарь-лекальщик С. П. Григорьев создал приспособление, продемонстрированное на рис. 3. На основании приспособления имеются три выступа с пазами, в которых закреплены хвостовики со стеблями.
Плоскости основания пазов строго перпендикулярны.
Изготовляют приспособление следующим образом. У бывших в потреблении микрометров с пределом измерения 0…25 мм отрезают скобы и оставляют хвостовики со стеблями.
После этого хвостовики шлифуют по месту паза. Установив все три хвостовика и проверив их поверхности по стеклянной плите 4, в проушинах основания сверлят по два отверстия и запрессовывают в них штифты.
При обработке микровинтов барабаны устанавливают по нониусу в нулевое положение и реализовывают предварительную доводку поверхностей, после этого их 3—4 раза поворачивают на ‘Д оборота (на 0,12 мм) и совсем доводят. Затем микровинты снимают с приспособления, устанавливают в ремонтируемые микрометры и создают контроль.
При несовмещении нулевого деления на барабане микрометра с нулевым делением на шкале нужно отвернуть головку микрометра на 1—2 оборота и, потянув за барабан в сторону скобы, снять с корпуса шпинделя. Установив после этого барабан в верном (нулевом) положении, поворотом головки микрометра закрепляют его на шпинделе стопорным винтом.
Плавный движение микрометрического винта характеризуется отсутствием люфта и заеданий на некоторых участках. Люфт в большинстве случаев ощущается рукой, а заедания возможно выяснить, развернув винт за головку трещотки по всему диапазону шкалы микрометра.
В случае если наряду с этим трение винта в гайке на некоторых участках будет так громадно, что трещотка начнёт провёртываться вхолостую около оси, значит он имеет неравномерный износ и подлежит замене либо исправлению.
Люфт ликвидируют поворотом конусной гайки, навернутой на гайку винта. При неравномерном износе винта его исправляют доводкой особым разрезным резьбовым притиром.