Отливки из алюминиевых сплавов
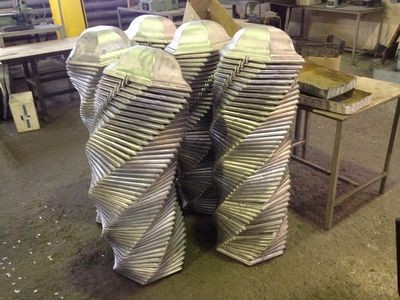
Для изготовления отливок применяют пять групп алюминиевых сплавов: 1) на базе совокупности алюминий-кремний; 2) алюминий-медь; 3) алюминий-магний; 4) совокупности алюминий-кремний-медь; 5) другие сплавы.
Алюминиевые сплавы имеют большую удельную прочность при обычной температуре, прекрасно противостоят коррозии в атмосферных условиях, владеют высокими литейными особенностями.
Громаднейшее использование в индустрии взяли сплавы первой и четвертой групп.
Сплавы совокупности алюминий-кремний (силумины) активно используются в авиационной, автомобильной, приборостроительной, машиностроительной, судостроительной и в электротехнической индустрии. По содержанию кремния они близки к эвтектическим и исходя из этого владеют лучшими, чем другие сплавы, литейными особенностями.
Двойные доэвтектические сплавы алюминия с кремнием имеют низкую прочность. Исходя из этого в состав их вводят магний, образующий с кремнием химическое соединение Mg2Si, упрочняющее сплав в ходе термической обработки.
самая вредной примесью для силуминов есть железо. Образуя хрупкие тройные (Al-Fe-Si) и более сложные фазы, кристаллизующиеся в виде пластин, железо значительно снижает пластические особенности сплавов.
Для нейтрализации вредного влияния железа в сплав вводят марганец. Десятые доли марганца содействуют переводу выделений железистой составляющей в более благоприятную (компактную) форму.
При литье в песчано-глинистые формы легирование силуминов марганцем и магнием не снабжает еще получения нужных механических особенностей из-за неотёсанного выделения кремния в эвтектике. Исходя из этого при литье в разовые, низкотеплопроводные формы сплавы совокупности алюминий-кремний, которые содержат не меньше 6% Si, подвергают модифицированию.
Для данной цели в расплав вводят 0,01-0,1% Na. В присутствии натрия эвтектический кремний выделяется в виде тонкодисперсных пластин, что благоприятно отражается на пластических особенностях. Подобное влияние оказывают на структуру калия присадки и сплава кальция, окислов щелочных металлов, сурьма, висмут, литий бор и т. д.
Сплавы на базе совокупности алюминий-медь владеют низкой коррозионной недостаточной пластичностью и стойкостью. В отличие от сплавов первой группы они прекрасно обрабатываются резанием.
Благодаря широкого промежутка кристаллизации сплавы данной совокупности склонны к образованию усадочных трещин и рассеянной усадочной пористости. Отличительной изюминкой алюминиевомедных сплавов есть их теплопрочность.
Механические и эксплуатационные особенности сплавов улучшают присадками титана и марганца (сплав АЛ 19) и термической обработкой.
Сплавы алюминия с кремнием и медью обширно применяют для того чтобы, владеющих прочностью и достаточной твёрдостью, сохраняющих постоянство размеров в ходе эксплуатации и отвечающих требованиям по чистоте обработанной поверхности (корпусы разных устройств, автомобильные и тракторные поршни, детали авиационных двигателей). Среди сплавов данной группы самые благоприятными особенностями владеет АЛ7-4.
Сплавы совокупности алюминий-магний отличаются низкой плотностью и высокими прочностью и коррозионной стойкостью; их применяют для того чтобы изготовить присадку, испытывающих громадные вибрационные нагрузки либо подвергающиеся действию морской воды (АЛ8, АЛ22).
Благодаря повышенной склонности к окислению, образов а-нию усадочных трещин и рыхлот, сотрудничеству с влагой формы, пониженной жидкотекучести — изготовление отливок из сплавов совокупности алюминий-магний приводит к технологическим трудностям.
Сплавы, не входящие в рассмотренные совокупности, относятся к группе сложнолегированных, и используются для того чтобы, действующий при давлениях АЛ и повышенных (температурах 1), требующих повышенной стабильности размеров (ВАЛ4), для изготовления сварных конструкций (ВАЛ4) и подробностей, прекрасно обрабатывающихся резанием (АЛ11).
В зависимости от специфики и масштаба производства плавку алюминиевых сплавов в литейных цехах реализовывают в печах: электрических тигельных и отражательных; в тигельных, трудящихся на жидком и газообразном горючем, и в индукционных.
При плавке на воздухе алюминиевые сплавы окисляются и насыщаются водородом. В ходе окисления на поверхности алюминия образуется плотная и прочная окисная пленка.
При достижении толщины пленки -2000 А окисление фактически заканчивается из-за малой скорости диффузии кислорода через пленку. Легирование алюминия магнием, медью, никелем и цинком усиливает окисление, поскольку окислы этих элементов владеют меньшей плотностью, чем окислы алюминия.
Скорость окисления значительно уменьшается при легировании алюминия лантаном и церием; большая часть же легирующих элементов (Si, др и Мп.) не воздействует на скорость окисления.
Алюминиевые сплавы склонны к газопоглощению. Особенно энергично в них растворяется водород, что содействует получению отливок с раковинами и газовой пористостью.
Алюминиевые расплавы предохраняют от поглощения и окисления водорода плавкой под флюсами. В качестве покровного флюса при плавке млогих сплавов, содержащих не более 1% Mg, применяют смесь (2% от массы калия) хлоридов и шихты натрия (45% NaCl и 55% КС1).
Для обеспечения полного отделения окислов алюминия в состав флюсов вводят до 25% криолита (Na3AlF6).
Для алюминиевомагниевых сплавов в качестве покровного флюса применяют карналлит (MgCl2-KCl) с добавками хлористого бария (ВаС12) либо фтористого кальция (CaF2).
В тех случаях, в то время, когда нереально использование флюса, защиту от окисления снабжают легированием сплавов бериллием (0,03-0,05%).
Но как бы шепетильно не проводилась защита расплавов, при плавке на воздухе они постоянно оказываются загрязненными и перед заливкой в формы требуют очистки.
В зависимости от объёма производства и состава сплава рафинирование (очистку) расплавов от взвешенных водорода и неметаллических включений реализовывают продувкой инертными (Аг, N) либо активными (С1) газами, обработкой хлоридами (МпС12), ZnCl2, TiCl4, выдержкой и флюсами в вакууме.
При пропускании газов (0,2-0,8% от массы металла) через расплав они оказывают флотирующее воздействие на взвешенные включения; пузырьки рафинирующего газа выносят их на поверхность расплава. Потому, что в пузырька рафинирующего газа давление атомарного водорода равняется нулю, растворенный водород диффундирует вовнутрь пузырька рафинирующего газа и выносится за пределы расплава.
Очистка тем интенсивнее, чем мельче пузырьки рафинирующего газа и чем равномернее распределены они в количестве расплава.
Введение в расплав хлоридов марганца, других металлов и цинка сопровождается образованием хлористого алюминия, пары которого кроме этого воздействуют как хлор и аргон. Оптимальное количество хлоридов образовывает 0,1-0,3% от массы расплава.
Рафинирование алюминиевых расплавов газами реализовывают при 720-750° С в течение 1.0-12 мин в той же печи, где велось расплавление. Затем для выделения небольших газовых пузырьков расплав отстаивают в течение 15-20 мин.
Рафинирование флюсом реализовывают при 730-750° С. Флюс (0,5-1% от массы металла), предварительно переплавленный, засыпают на поверхность металла либо вводят вовнутрь его особым приспособлением. В некоторых случаях рафинирование осуществяют при разливке; флюс расплавляют, порцию его заливают в тигель, а после этого через флюс в тигель заливают металл; неметаллические “включения наряду с этим экстрагируются.
Для дегазации расплав возможно выдержан в воздухе инертного газа либо вакууме (15-20 мин при остаточном давлении 50-100 мм рт. ст.).
Рафинирование осуществляют контроль при помощи технологических проб, химического и газового анализа.
Сплавы, которые содержат более 6% Si, перед заливкой в разовые формы подвергают модифицированию. Операция модифицирования измельчает выделения кремния и повышает механические особенности сплавов.
Модифицирование реализовывают введением в расплав пара сотых долей процента натрия. Для данной цели применяют в основном смеси хлористых и фтористых солей натрия и реже чистый натрий.
Затем соли замешивают в расплав и через 3-5 мин удаляют совместно со шлаком.
Шепетильно очищенный расплав возможно снова загрязнен в ходе литья. Падение струи металла с высоты более 300 мм сопровождается образованием и вспениванием окислов, часть которых попадает в отливку.
Для алюминиевых сплавов недопустимы завихрения, образующиеся в местах удара струи о стенку формы. Воздушное пространство, захваченный вихревым потоком, загрязняет сплав окислами.
В связи с этим формы заполняют алюминиевыми сплавами с минимальной линейной скоростью перемещения струи на выходе из литников, для чего применяют расширяющиеся совокупности. Длительность заполнения форм регулируют трансформацией площади сечения литниковых каналов.
В условиях массового и крупносерийного производств многие отливки из алюминиевых сплавов изготовляют в железных формах (кокилях). Низкая температура литья этих сплавов и наличие пленки А1203, образующейся на поверхности отливок, увеличивают стойкость кокилей и, следовательно, экономическую целесообразность их применения.
Для алюминиевых сплавов свойственны расширяющиеся литниковые совокупности, предусматривающие отделение взвешенных неметаллических включений. Частенько в шлаковиках устанавливают сетки (стеклоткань, титановая, металлическая, из стержневой смеси), усложняют каналы устройством шлаковыпоров, разных поворотов, применяют кусковые фильтры.
В некоторых случаях предусматривают два последовательности шлаковиков.
Для предотвращения захвата воздуха при заполнении высоких (300 мм) форм используют многоярусные и щелевые литниковые совокупности, разрешающие взять самоё благоприятное распределение температуры по высоте отливки.
Алюминиевые сплавы склонны к образованию усадочной пористости, устранение которой в отливках достигается установкой массивных доходов, холодильников, а для важных подробностей — кристаллизацией в автоклавах под давлением сжатого воздуха.
Очистку отливок создают на гидропескоструйных установках. В зависимости от состава сплава отливки проходят определенный режим термической обработки.
Характерным есть кроме этого пропитка пористых отливок разными лаками.