Пневматические конструкции
Пневматическими конструкциями именуют мягкие оболочки, заданная форма и несущая свойство которых обеспечивается нагнетаемым в них воздухом. Материалом для пневматических конструкций помогают армированные и неармированные полимерные пленки, ткани, покрытые либо пропитанные полимерами, высокопрочные сетки и стальные канаты, и тонколистовой металлический и алюминиевый прокат.
В зависимости от метода приложения избыточного давления воздуха и связанного с этим соотношения главных геометрических размеров пневматические конструкции подразделяют на воздухоопорные, пневмокаркасные и комбинированные.
Воздухоопорные конструкции. К ним относятся мягкие оболочки, делающие ограждающие функции и сохраняющие заданную форму благодаря нагнетаемому в них воздуху под маленьким (0,1…1,0 кПа) давлением, при котором в оболочке смогут пребывать и трудиться люди.
Главными конструктивными элементами для того чтобы сооружения являются фактически оболочка 2, воздуходувная установка, тамбур-шлюз с двумя поочередно открываемыми проемами, опорный контур, включающий твёрдый бортовой элемент либо мягкий анкерные устройства и тросовый пояс разного типа. Значительно чаще воздухоопорные конструкции делают в виде цилиндрических сводов с разной стрелой подъема.
Торцовые части сводов смогут быть плоскими, сферическими и цилиндрическими. Для большепролетных сооружений применяют оболочки, усиленные облегающими сетками и канатами.
Воздухоопорные оболочки бывают одно-, двух- и трехслойные, трудящиеся по принципу послойного повышения давления без связывания отдельных слоев диафрагмами, либо образованные методом дополнительных тканевых либо пленочных подвесок. Оболочки смогут крепиться конкретно к почва либо опираться на стены.
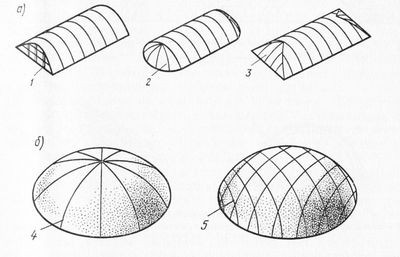
Рис. 1. Воздухоопорные конструкции: а — цилиндрические; б — сферические; 1, 2, 3 — с плоским, сферическим, цилиндрическим торцами; 4 — усиленный облегающими верёвками; 5 — то же, сферической сеткой
Пневмокаркасные конструкции. В отличие от воздухоопорных они имеют герметически замкнутые полости, в которых поддерживается относительно большое избыточное давление.
Элементы пневмокаркасных конструкций смогут быть линейными, плоскими и пространственными. Помимо этого, они разделяются на пневмо-стержневые (балки, стойки, арки и другие несущие элементы с громадным избыточным давлением) и пневмопанельные — ограждающие конструкции с маленьким избыточным давлением.
самый характерным примером пневмокаркасной конструкции может служить свод с несущим каркасом из пневмоарок и пневмопрогонов, покрытых тканевой ограждающей оболочкой. Пневмо-панели образуются воздухонепроницаемыми оболочками, связанными диафрагмами, а при солидном числе внутренних связей (нитей) возможно взять плоские пневмоматы, из которых формируют разные многоугольные конструкции.
Изогнутые пневмопанели образуют двухслойный пневмосвод.
Комбинированные пневмоконструкции. Они совмещают в себе свойства воздухоопорных и пневмокаркасных.
Конструкции имеют тканевое либо пленочное ограждение, поддерживаемое совокупностью пневмокаркасных элементов и одновременно избыточным давлением воздуха в нужном пространстве. Несложным примером комбинированной конструкции может служить коническая тканевая оболочка, поддерживаемая пневмостойкой, а при сильных ветровых нагрузок — избыточным давлением в нужном количестве.
Многие пневматические конструкции светопроницаемы, исходя из этого микроклимат в рабочем пространстве зависит от солнечной радиации. Для стабилизации теплового режима используется совокупность светорегулирующих рукавов.
Рис. 2. Многослойные оболочки: а — с раздельным поддувом; б —с неспециализированным поддувом; в —с дополнительными подвесками-утеплителями
Рис. 3. Пневмокаркасный цилиндрический свод: 1 — пневмоарка; 2 — ограждающая тканевая оболочка; 3 — компрессор; 4 — опорный элемент; 5 — пневмопрогоны
Рис. 4. Комбинированная тентовая пневмоконструкция: а — в режиме обычной эксплуатации; б — при создании избыточного давления в нужном количестве; 1 — оболочка; 2— пневмостойка с оголовком
Из рассмотренных конструкций по большей части используются воздухоопорные оболочки. Их преимущества — быстрота монтажа (0,15…0,5 чел-ч/м2 покрытия), малая масса (2…3,5 кг на 1 м2 перекрываемой площади), небольшой транспортный количество, низкая удельная цена монтажа (8…20% неспециализированной цене сооружения), функциональная приспособляемость формы, сейсмостойкость, легкость транспортирования.
Одновременно с этим всем пневматическим конструкциям свойствен последовательность недочётов: небольшой (до 10 лет) срок работы, обусловленный старением полимерных материалов, негативные звуковые характеристики, потребность в вентиляторных либо компрессорных установках.
В качестве материала оболочек пневматических конструкций используют армированные полимерные пленки либо покрытые полимером ткани. Пленки приобретают из полиамидов, полиэфиров, полиэтилена, полипропилена, поливинилхлорида; для армирования применяют капроновые, лавсановые, железные и волокна и стеклянные сетки.
Ткани покрывают либо пропитывают поливинил-хлоридом, полихлоропреном, хлорсульфополиэтиленом, и этилен-пропиленовым и полиуретановым каучуками. Сами ткани смогут быть хлопчатобумажные, синтетические (полиамидные, полиэфирные, полиакриловые, поливиниловые и др.), неестественные (целлюлозные), стеклянные.
Покрытие наносится в заводских условиях (на каландрах) толщиной 0,5… 1 мм.
Неспециализированным преимуществом пленок являются воздухопроницаемость, тепло- и морозоустойчивость, биологическая и химическая стойкость, светопрозрачносгь, регулируемая в широких пределах, лёгкость и достаточная прочность. Главные недочёты — ползучесть, утрата эластичности при старении.
Для пневматических конструкций применяют полиамидные пленки разных марок. Пленки сваривают термическим методом, токами высокой частоты либо склеивают. Взяли распространение конструкционные полиэтилентерефталатные пленки.
Их отличают высокая (более 90%) степень пропускания солнечного света, достаточная прочность, относительно большой модуль упругости, хорошая сопротивляемость многократному изгибу и ударным воздействиям. Полотнища полиэтилентерефталатной пленки соединяются полиэфирным клеем, снабжающим работу соединений в промежутке температур от —150 до +100 °С.
Клеевые соединения прозрачны, водо-, масло- и морозостойки.
Однородные пленки в большинстве случаев используют с разными армирующими материалами — нитями либо сетками из синтетических, стеклянных, железных волокон. При армировании сохраняются оптические особенности пленок, увеличиваются их прочность на сопротивление и разрыв раздиру.
Полиамидные пленки, армированные волокнами и капроновыми сетками, помогают не только для пневмоконструкций, но, и для того чтобы, трудящихся в агрессивных средах. Их сваривают из отдельных полотнищ в громадные оболочки на особом оборудовании.
Тканевые материалы, используемые для пневмоконструкций, изготовляют из натуральных (лен, хлопок), неестественных (вискоза, стекловолокно) и синтетических (полиамиды, полиэфиры, поли-акрилаты) волокон. Тканевая база может иметь полотняное (одна нить) либо рогожное (две либо три нити) переплетения.
Для обеспечения воздухо- и водонепроницаемости тканевую базу покрывают с одной либо двух сторон синтетическими каучу-ками и эластичными полимерами (хлорсульфированный полиэтилен, пластифицированный поливинилхлорид). Покрывающие полимеры смогут быть светопроницаемы, окрашены в любой цвет.
Они должны быть морозостойки при температуре до —40 °С. Главные требования к тканеполимсрным материалам для пневмоконструкций — прочность, легкость, эластичность, долговечность, тепло- и морозоустойчивость, технологичность при обработке для изготовления конструктивных элементов.
Не считая пневматических сооружений пленки и ткани применяют для пневматической опалубки. Ее изготовляют по тому же принципу, что и воздухоопорные конструкции.
В оболочку подают воздушное пространство, и по окончании того как она принимает заданную форму, на нее укладывают арматуру и создают набрызг бетона. По другому варианту бетон и арматуру укладывают на горизонтально расположенную оболочку, а после этого нагнетают в нее воздушное пространство, по окончании чего конструкция занимает проектное положение на целый период твердения бетона.