Полуавтоматические линии по производству оконных переплетов
На Московском деревообрабатывающем комбинате № 3 оборудовано несколько полуавтоматических переменно-поточных линий по производству оконных и дверных блоков. Для перевода производства на поток установлена специализация номенклатуры изделий.
Первая полуавтоматическая поточная линия была установлена для изготовления деталей оконных переплетов.
В состав этой линии входят:
— рольганговый стол с автоматическим включением для подачи заготовок к маятниковой пиле;
—- маятниковая пила, автоматически работающая на поперечном раскрое заготовок;
— пассовый транспортер, передающий раскроенные детали на прирезной станок;
— автоподатчик;
— фуговальный станок;
— четырехсторонний строгальный станок, соединенный роликовым столом с двухсторонним автошппорезным станком;
— пассовый транспортер, подающий детали две горизонтально-сверлильных станка.
Вместо ранее занятых на этих операциях рабочих на линии работает всего пять человек в смену. Передача заготовок от станка к станку толкающая.
Производительность линии в смену при средней длине заготовки 1 м составляет 5760 деталей.
Вторая линия предназначена для сборки оконных переплетов из деталей, изготовленных на первой линии.
В состав этой линии входят: ленточный транспортер, станок для высверливания сучков в деталях переплетов, клеенамазочный станок, три механические ваймы для сборки элементов оконных переплетов, станок для зачистки с двумя косорасположенными валами, механический податчик для передачи деталей на фальцовочно-калибровые станки, станок для вырубки гнезд под петли в створках, станок-полуавтомат для завертывания шурупов. Принцип передачи заготовок толкающий.
Третья линия состоит из ленточного транспортера, галтовочного барабана для очистки петель от жира, станка для выборки гнезд под петли, двух станков-полуавтоматов для завертывания шурупов, механической ваймы для сборки оконных коробок. Готовые оконные переплеты и коробки поступают на сборочные столы, где их собирают в блоки.
Собранные блоки подвесным конвейером подаются в малярный цех. На этих двух линиях работают семнадцать рабочих.
Четвертая линия служит для изготовления деталей оконных коробок. Состоит она из маятниковой пилы для автоматического поперечного раскроя заготовок, автоподатчика к фуговальному станку, фуговального станка, фрезерного станка, четырехстороннего строгального станка и двухстороннего шипорезного станка.
Производительность линии в смену при средней длине заготовок 1 м составляет 3840 деталей. Работает на линии всего четверо рабочих вместо восьми.
Пятая поточная линия предназначена для производства погонажных изделий (наличников) с прирезкой их на ус с автоматическим нанесением олифы. В состав этой линии входит маятниковая пила для автоматического поперечного раскроя заготовок, прирезной станок, четырехсторонний строгальный станок, рейсмусовый станок, трехсторонний строгальный станок и односторонний шипорезный станок.
Внедрение поточной линии повышает производительность за счет автоматизации подачи, сокращения межстаночных перемещений деталей и сокращения расхода времени примерно в 1,5 раза.
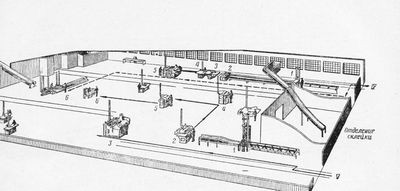
Рис. 1. Четвертая и пятая полуавтоматические переменно-поточные линии:
Автоматическая линия по обработке брусковых деталей, разработанная институтом Гипродревпром совместно с НИИдревмаш, является наиболее совершенной. Состоит она из станков и механизмов, расположенных в соответствии с технологией обработки в такой последовательности: автоматический питатель ПА-Б, двухсторонний фуговальный станок С2Ф4, второй двухсторонний фуговальный станок С2Ф4, транспортер, четырехсторонний строгальный станок, перекладчик, двухсторонний шипорезный станок, укладчик.
При обработке брусковых детален вначале вагонетка с прирезными заготовками поступает к автопитателю, представляющему собой наклонный цепной транспортер, посредством которого заготовки автоматически подаются к двухстороннему фуговальному станку С2Ф4. После строгания в угол на двух последовательно установленных фуговальных станках получается точная базовая поверхность, которая при последующем строгании на четырехстороннем строгальном станке дает возможность получить деталь необходимой точности.
Помимо строгания с четырех сторон, на четырехстороннем строгальном станке получается и нужный профиль детали. Затем на двухстороннем шипорезном станке производится зарезка шипов.
Для отбраковки деревянных заготовок по влажности на поточных полуавтоматических и автоматических линиях устанавливают автомат АКВ-1-М. Принцип работы автомата основан на просвечивании заготовок лучом электромагнитных волн.
Перемещающаяся по транспортеру заготовка пересекает направленный луч, поглощает часть электромагнитной энергии пропорционально своей влажности. Оставшаяся энергия улавливается приемным устройством, поступает на блок управления, усиливается и сравнивается с предварительной настройкой на заданную влажность.
Заготовка с повышенной влажностью поглощает больше электромагнитной энергии, вследствие чего она отбраковывается. Автомат может отбраковывать заготовки из древесины мягких пород толщиной 65 мм, из древесины твердых пород — толщиной 35 мм.
Для контроля качества обработки поверхностей древесины на автоматических, полуавтоматических и поточных линиях устанавливают автомат АКП-1. Он обнаруживает на строганой поверхности заготовок и деталей из древесины дефекты в виде отщепов, выкрашивающихся сучков и местных вырывов.
Дефектные детали автомат с конвейера выбрасывает и считает общее число прошедших деталей, число годных и забракованных деталей. Автомат снабжен световой сигнализацией.
Размеры проверяемых брусковых изделий могут быть: наименьшие 5X50X250 мм, наибольшие 60X150X2000 мм.
Рис. 2. Автомат для отбраковки деревянных заготовок по влажности АКВ-1-М:
1 — деревянные заготовки, 2 — подающие ролики, 3 — поглощение электромагнитной энергии, 4 — отбракованные заготовки
Рис. 3. Автомат АКП-1 для контроля поверхности древесины
Для контроля толщины и ширины дощатых и брусковых деталей на автоматических, полуавтоматических и поточных линиях устанавливают автомат АКШТ-1. Контроль одновременно осуществляется в одном, двух или трех сечениях электроконтактными датчиками, снабженными индикаторами для визуальных отсчетов.
Электромагнитные датчики автомата при помощи электронного усилителя управляют работой электромагнитного золотника, который приводит в действие пневматический цилиндр выброса забракованных деталей. Автомат устанавливают после четырехстороннего строгания изделий на роликовом транспортере.
Измеряют изделия по ширине до 200 мм, по толщине до 100 мм. Наибольший контрольный допуск 5 мм.
Скорость движения контролируемых деталей до 3 м/мин.
Рис. 4. Автомат АКШТ-1 для контроля ширины и толщины заготовок и деталей из древесины:
1 — деталь для контроля, 2 и 3 — электромагнитные датчики