Ремонт деталей поршневых и кривошипно-шатунных механизмов
Поршневая несколько подробностей входит в состав механизмов преобразования вращательного перемещения в поступательное.
К главным подробностям поршневой группы относится цилиндр складывающийся из так называемой внутренней втулки и рубашки либо гильзы, и поршень с поршневыми кольцами. Поршень соединен с шатуном при помощи поршневого пальца, второй финиш шатуна имеет вкладыш, что соединяет шатун с коленчатым валом.
В ходе эксплуатации благодаря износа возрастает зазор между стенками поршня и цилиндра; поверхность цилиндра получает нецилиндричность и некруглость, на стенках цилиндра образуются задиры. Поршневые кольца становятся менее упругими, возрастает зазор в замках, т. е. в местах, где находится стык финишей.
В следствии всего этого в полости цилиндра значительно уменьшается компрессия, т. е. степень сжатия газов, поскольку газы просачиваются между стенку-нами цилиндра и поршня. Из-за износа нарушается кроме этого посадка поршневого пальца в головке шатуна и бобышках поршня и посадка головки шатуна на шейке вала, что влечет за собой происхождение стука в сопряжениях.
Ремонт подробностей поршневых и кривошипно-шатунных механизмов довольно часто обходится дороже, чем изготовление новых. Исходя из этого в каждом конкретном случае делают выводы о целесообразности и способе ремонта.
Громаднейший эффект достигается заменой изношенных подробностей новыми запасными частями. Наряду с этим понижается время простоя автомобилей из-за ремонта, понижается трудоемкость и увеличивается уровень качества ремонта.
Но во многих случаях и особенно при ремонте больших компрессоров, пневматических молотов и других (и при отсутствии запасных частей) подробности поршневых и кривошипно-шатунных механизмов приходится ремонтировать. При таких условиях рационально пользоваться способами, рассмотренными ниже.
При ремонте подробностей поршневой группы нужно строго выдерживать технические требования на ремонт.
Ремонт цилиндров
Изношенные цилиндры принято ремонтировать по совокупности ремонтных размеров. При восстановлении цилиндра в сопряжении цилиндр — поршень производится механическая обработка отверстия цилиндра под больший ремонтный размер и соответственно подбирается новый поршень, диаметр которого больше диаметра прошлого.
Ремонтные размеры цилиндров, в большинстве случаев, устанавливаются фабриками-изготовителями. Эти размеры для цилиндров двигателей идут с градацией 0,5—1,0 мм в зависимости от диаметра цилиндра.
В случае если, к примеру, начальный (номинальный) диаметр цилиндра равен 101,57+°06 мм, то его первый ремонтный размер будет 102,07+° °® мм, второй — 102,57+0’06 мм и т д. до последнего пятого размера 104,07+0’06 мм. Последний ремонтный размер должен быть таким, дабы цилиндр был достаточно прочным.
Восстановление рабочей поверхности цилиндра по совокупности ремонтных размеров имеет то преимущество, что многократно употребляется корпус цилиндра (либо блок цилиндров). Изготовление же нового цилиндра требует громадных трудовых затрат.
Рис. 1. Поршневая несколько подробностей
Цилиндры, износ которых вышел за пределы последнего ремонтного размера, в отдельных случаях возможно вернуть последующей запрессовкой и растачиванием гильзы. Гильзу запрессовывают в расточенный корпус с натягом, после этого обрабатывают ее отверстие до номинального размера отверстия цилиндра.
В случае если в цилиндре уже имеется гильза и она изношена, то ее растачивают до ближайшего ремонтного размера на расточном либо токарном станке.
По окончании расточки создают хонингование цилиндров. Припуски на хонингование должны составлять 0,06—0,09 мм.
При отсутствии на предприятии хонинговального станка отделочную операцию отверстия цилиндра возможно выполнить на токарном либо сверлильном станке, используя шлифовальную головку.
По окончании окончательной обработки внутренняя поверхность цилиндра должна иметь 9-й класс шероховатости.
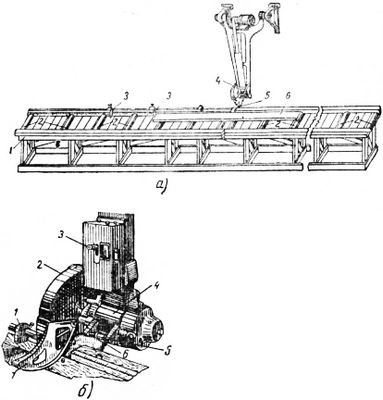
Рис. 2. Поршень
Ремонт поршней
У поршней в следствии эксплуатации изнашиваются отверстия и канавки под поршневой палец, и образуются трещины на донышке и риски на поверхности поршня.
Отверстия для поршневого пальца развертывают вручную особой разверткой в маленьких поршнях и растачивают на расточном станке у поршней громадных размеров. Расточку возможно делать и на токарном станке, в случае если применить особое приспособление.
Выбор посадки поршневого пальца в отверстие поршня — с натягом либо зазором — зависит от условий и конструкции поршня, в которых он трудится.
Места на цилиндрической поверхности поршня, где имеются задиры либо наплывы, и днище запиливают личным напильником, позже зачищают и полируют мелкозернистой наждачной бумагой.
Поршни с трещинами в большинстве случаев выбраковывают. Большому износу подвержены поршневые канавки, каковые восстанавливают проточкой на токарном станке до ремонтного размера.
Ремонт поршневых пальцев и поршневых колец
У поршневых пальцев изнашивается наружная поверхность, сопрягаемая со бобышкой поршня и втулкой шатуна. Предельно допустимый зазор между втулкой и пальцем в зависимости от типа автомобилей образовывает от 0,1 — до 0,15 мм, а зазор по окончании ремонта обязан составлять 0,002—0,025 мм.
При ремонте изношенные пальцы довольно часто заменяют новыми, потому, что трудоемкость их изготовления мала, и пригоняют по восстановленным отверстиям в втулке и поршне шатуна. Время от времени пальцы хромируют по наружному диаметру для того, чтобы они соответствовали повышенному размеру.
В случае если поршень заменен новым, необходимо исходить из того, что его отверстие под поршневой палец имеет номинальный размер.
Из всех подробностей шатунно-поршневой группы громаднейшему износу подвергаются поршневые кольца и особенно верхнее компрессионное кольцо. Об иЗносе колец делают выводы по зазорам между канавкой и кольцом и в стыке.
Поршневые кольца, в случае если зазор между канавкой и кольцом больше 0,3—0,4 мм, а в стыке больше 3—4 мм, в большинстве случаев заменяют.
Кольцо, утратившее упругость, кроме этого заменяют. Для определения упругости поршневого кольца пользуются таблицами и специальным прибором, показывающими соотношение между силой сжатия и зазором, что обязан оказаться наряду с этим сжатии.
Рис. 3. Поршневые кольца:
а — форма замка кольца, б — схема закрепления заготовки кольца для обработки по внутреннему диаметру, в — закрепление кольца для обработки по наружному диаметру, г — измерение зазора в замке шупом
В ремонтной практике поршневые кольца в большинстве случаев изготовляют так: обтачивают чугунный пустотелый цилиндр, после этого его разрезают на кольца с припуском для обработки колец по внутреннему диаметрам и наружному, и по высоте. Из каждого кольца вырезают маленькой участок, образуя сквозную щель, разрешающую кольцу сжиматься и создавать стык.
В стыке устраивается так называемый замок, мешающий просачиванию газов. Его делают или с косым вырезом под углом 45°, или с прямым вырезом в накладку.
Второй метод более надежный, но направляться иметь в виду, что у колец малого диаметра нельзя делать замок в накладку, поскольку его узкие части тогда легко обламываются. Кольца диаметром 300 мм и более сжимают практически до соприкосновения поверхностей выреза (торцов) и спаивают, после этого их совсем протачивают по внутреннему диаметрам и наружному.
Затем кольца распаивают.
Поршневые кольца растачивают и обтачивают на размер на особых оправках, по окончании того как у колец сделан вырез, устроен замок и совсем обработаны торцы. На одной оправке кольцо растачивают в размер, на другой оправке его совсем обрабатывают снаружи.
Закрепление поршневого кольца в оправках создают через фланцы и винтом.
Зазор между канавкой и кольцом по высоте в отремонтированных сочленениях колеблется от 0,06 до 0,12 мм и зависит от типа автомобили. Контролируют зазоры шупом.
Поршневые кольца громадных размеров пригоняют к канавкам шабрением с последующей притиркой торцов по плите. В случае если имеется возможность, то лучше шлифовать кольца на плоскошлифовальном станке.
Маленькие кольца пригоняют шлифованием.
Поместив кольцо в восстановленном цилиндре, определяют зазор в замке щупом. Последние операции — его зачистка и пригонка замка — личным напильником, или оселком.
При установке колец на поршень нужно добиться равномерного размещения замков по периметру цилиндра, что еще надежнее предотвращает прорыв находящихся в цилиндре газов либо пара.
Ремонт шатунов
В двигателях, паровых машинах и компрессорах используются различные виды шатунов, но условия, в которых они все трудятся, предъявляемые к ним требования по большей части однообразны.
Рис. 4. Шатун:
а — набор подробностей шатуна, б — проверка параллельности осей верхней и нижней головок шатуна; 1— стержень, 2—болты, 3 — поверхности разъема громадной головки, 4 — гайки, 5 — шплинты, 6,9 — половинки громадной головки, 7—вкладыши, 8— прокладки, 10 — втулка, 11— малая головка шатуна. 12 — призма, 13 — опорная площадка, 14 — контрольная плита, 15 — щуп, 16 — оправки
Шатун складывается из последовательности подробностей, каковые в работе изна-тиьшшся. Стержень изгибается либо скручивается, повреждаются поверхности разъема громадной крышки и головки шатуна.
Смогут изнашиваться вкладыши либо втулки 10, поверхности посадочного отверстия в малой головке 11, внутренняя поверхность громадной головки под вкладыши.
В случае если стержень шатуна изогнут либо скручен не очень сильно, его выправляют на прессе.
Для проверки шатунов на скручивание и изгиб используют особое приспособление, главными частями которого являются контрольная плита с оправками и и призма. В верхнюю головку устанавливают оправку и надевают шатун нижней головкой на оправку.
На цилиндрические выступы оправки устанавливают призму, имеющую три опорные площадки. В случае если стержень шатуна не изогнут и не скручен, оси отверстий головок должны быть параллельны, наряду с этим все три опорные площадки будут соприкасаться с плитой.
Вероятный зазор между какой-либо из опорных площадок и плитой контролируется щупом. Допустимая величина зазоров в каждом конкретном случае указывается в инструкционной карте.
Не разрешается править шатуны в сборе.
Шатуны с маленьким износом поверхностей отверстий громадной головки и крышки ремонтируют так: опиливают, фрезеруют либо пришабривают по плите поверхности разъема с учетом того, что в следствии последующего растачивания внутренних цилиндрических поверхностей диаметр этих отверстий пара увеличится; поверхности разъема со большими повреждениями возможно вернуть наплавкой с последующим фрезерованием. При износе баббита вкладышей создают перезаливку и после этого вкладыши растачивают.
Изношенное отверстие головки растачивают до следующего ремонтного размера и изготовляют новую втулку.