Ремонт насосов
Насосы в гидросистемах
Нясосы, нагнетающие масло в рабочие цилиндры, являются главными механизмами гидроприводов. В гидроприводах промышленного оборудования используются шестеренчатые, лопастные (пластинчатые), поршневые и другие насосы
Шестеренчатые насосы складываются из двух шестеренок (в основном наружного зацепления), вращающихся с малыми зазорами в корпусе.
Масло захватывается вращающимися зубчатыми шестернями из всасывающей территории впадинами зубьев; выступы зубьев, входя в зацепление, выталкивают масло из впадин зубьев в зону нагнетания. Для устранения излишнего давления, появляющегося между зубьями, в месте заклинивания жидкости, на торце корпуса (либо вкладышей), выполнена особая канавка, отводящая закрываемое масло в зону нагнетания.
Данный процесс происходит непрерывно.
Шестеренчатый насоо складывается из корпуса, к торцам которого прикреплены фланцы. На приводном валу помещена ведущая шестерня, соединяемая с ведомой.
Обе шестерни соединены с валиками и при помощи шпонок по скользящей посадке. От осевого смещения валики удерживаются пружинными кольцами. Цапфы валиков вращаются на игольчатых подшипниках в набором иголок.
На стыках крышек и корпуса поставлены прокладки из узкой бумаги, снабжающие герметичность соединения. Для предотвращения утечки масла по приводному валику через отверстие в крышке предусмотрен сальник.
Конструктивные изюминки шестеренчатых насосов очень разнообразны. Они различаются по производительности, давлению опорами скольжения и качения, по методу монтажа и др.
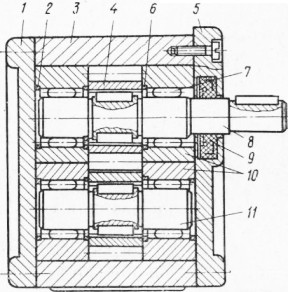
Рис. 1. Неспециализированный вил шестеренчатого насоса ГП-22
Ремонт шестеренчатых насосов
В шестеренчатом насосе изнашиваются по наружному и торцам диаметру шестеренки, и сопрягающиеся с ними внутренние другие детали и поверхности корпуса насоса. Шестеренки испытывают одностороннее давление жидкости, направленное из полости нагнетания в сторону всасывания.
Исходя из этого сопрягающиеся с ними внутренние поверхности корпуса приобретают односторонний износ, тем больший, чем выше давление жидкости. В то время, когда же работа ведется на загрязненном масле, улучшается износ зубьев шестеренок, и подшипников и поверхности приводного вала, сопрягающейся с сальниковой набивкой
Рис. 2. Схема к ремонту шестеренчатых насосов пластмассовыми композициями
Изношенные шестеренчатые насосы трудятся неровно. Их производительность существенно понижается и давление падает из-за повышенного протекания масла между внутренними поверхностями и зубьями колёс корпуса.
Внутренние поверхности корпуса при ремонте растачивают, снимая слой металла нужно не больше 0,2 мм, после этого их шлифуют. Ветхие шестеренки заменяют новыми — корригированными с припуском по торцам для шлифования торцов (при сборке) и с диаметром выступов, увеличенным на глубину расточки корпуса.
Возможно восстанавливать корпус шестеренчатого насоса пластмассовыми композициями. Для этого растачивают отверстие так, дабы появился зазор 2—3 мм, и изготовляют особые вставки, диаметр которых равен наружному диаметру устанавливаемых шестеренок.
Вставки устанавливают в отверстия для подшипников валов насоса и вместе с крышками и скрепляют с корпусом. Из пластилина делают воронки, закрывают пластилином нагнетания и отверстия всасывания и заполняют пространство между корпусом насоса и вставками пластмассовой композицией, образуя втулки.
По окончании отвердевания пластика отвинчивают центрирующие винты, очищают от пластилина, снимают крышки и и удаляют приливы пластика. Этим методом восстанавливают насосы, трудящиеся с давлением до 2,5 МПа (25 кгс/см2).
В случае если для шестеренчатого насоса изготовляют новые шестеренки то заготовки колес перед нарезанием зубьев в обязательном порядке прошлифо-вывают по наружному диаметру, имея в виду, что зазор между внутренней поверхностью и головками зубьев корпуса не должен быть больше 0,02 мм. Изготовляют шестеренки из цементируемой стали и закаливают до твердости HRC52—58.
Точность изготовления должна быть таковой, дабы биение колес не превышало 0,04 мм, а отклонение от параллельности между осью отверстия и зубьями — 0,03 мм.
При ремонте шестеренок с маленьким износом по их наружному и профилю зубьев диаметру (между зубьями сцепляющихся колес проходит щуп толщиной до 0,1 мм) ограничиваются шлифованием торцов колес; так же шлифуют до устранения следов износа сопрягающиеся с ними торцы вкладышей. Колеса со большим износом в большинстве случаев заменяют новыми.
Вместе с ними сменяют кроме этого приводной валик, уплотнение и подшипники.
Отремонтированные насосы прекрасно трудятся, в случае если в них соблюдены установленные зазоры между колесами, прокладками и корпусом. Суммарные зазоры между вкладышами и торцами колёс, и между головками зубьев колес и сопряженной с ними внутренней поверх, ностью корпуса допускаются 0,03—0,05 мм.
Диагностику зазоров реализовывают щупом и линейкой, определяют разность высоты между торцом зубчатого колеса и корпусом насоса, щупом контролируют зазор между рабочими профилями зубьев и зазор между сопряженными поверхностями шестеренок и корпуса насоса.
При сборке насосов используют для уплотнения бумажные прокладки, каковые рекомендуется пропитать нитролаком. В случае если шестеренчатый насос собирают без таких уплотняющих прокладок, необходимо шепетильно пригнать (шабрением, шлифованием либо вторыми методами) сопрягаемые поверхности подробностей, снабжая надежную герметичность соединений между крышками и корпусом.
Ремонт пластинчатых (лопастных) насосов
Пластинчатые насосы производят разных размеров и типов, отличаются они по давлению и производительности от до 12,5 МПа (от 50 до 125 кгс/см2). На рис.
58 продемонстрирован насос, предназначенный для подачи чистых минеральных масел в гидросистемы оборудования под Давлением 125 кгс/см2. Насос типа БГ12-2 постоянной производительности представляет собой объемную ротационную машину пластинчатого типа двойного действия.
Устроен насос следующим образом. В крышке и чугунном корпусе установлен статор, имеющий в криволинейную профилированную поверхность, по которой скользят десять сдвоенных лопаток, вольно перемещающихся в радиальных пазах ротора.
Ротор посажен на шлицы вала, вольно вращающегося на шарикоподшипниках.
Для распределения уплотнения и потоков масла торцов статора и ротора помогают диск и плоский диск с шейкой. Плоский диск имеет два главных всасывающих окна для всасывания рабочей жидкости в камеры между лопатками и два вспомогательных окна для всасывания рабочей жидкости в камеры под лопатками.
Для повышения площади всасывающие окна соединяются отверстиями, сделанными в статоре, с глухими главными и запасными всасывающими окнами диска с шейкой, за счет чего обеспечивается всасывание рабочей жидкости с двух сторон ротора.
Рис. 3. Пластинчатый насос типа БГ12-2
Диск с шейкой плавающего типа имеет не считая всасывающих еще главные окна для нагнетания рабочей жидкости из камер между лопатками и вспомогательные для нагнетания рабочей жидкости из-под лопаток. Плоский диск кроме всасывающих окон имеет еще глухие главные и вспомогательные нагнетательные окна, так что нагнетание производится с двух сторон ротора.
Ввиду того, что в полости всасывания пространство под лопатками соединяется с линией всасывания, обеспечивается разгрузка лопаток от гидравлического упрочнения, прижимающего лопатки к статору. Прижим лопаток к статору в полости всасывания осуществляется центробежной силой.
В начале работы прижим диска с шейкой осуществляется пружинами 10, а в ходе работы — и давлением масла.
Для предотвращения утечек в насосе применена манжета во фланце и круглые кольца.
Нарушение обычной работы лопастных насосов проявляется в понижении их производительности, подъёмах давления и произвольных падениях подаваемой появлении и жидкости стука и повышенного шума. Громаднейшему износу в большинстве случаев подвергаются ротор, лопатки, диски, и шарикоподшипники, манжета и др.
Статорные кольца особенно очень сильно изнашиваются в местах перехода от одного радиуса к второму, где образуются ступени и задиры. Ремонт статорных колес сводится к шлифованию их внутреннего профиля.
Так как по окончании установки отремонтированных этим методом колец падает производительность насосов, стремятся заменять изношенные статорные кольца новыми. Новые кольца изготовляют из стали ШХ15 либо стали ХВГ.
Термообработкой им придают твердость до HRC60-64.
Изношенный ротор целесообразно не заменять, а ремонтировать, поскольку изготовление нового ротора сопряжено со серьёзными трудностями. Ремонт содержится в восстановлении параллельности стенок пазов, шлифовании изношенных шеек и торцов.
Пазы с износом не более 0,05 мм ремонтируют вручную при помощи абразивного порошка с последующей доводкой шлифовальной пастой. Предельная допустимая непараллельность стенок пазов 0,02 мм.
При большем износе стенок пазов их параллельность восстанавливают обработкой узким абразивным кружком на станке с доводкой вручную. направляться иметь в виду, что при большом возрастании ширины пазов приходится увеличивать ширину лопаток и в следствии увеличивается давление лопаток на статор, ускоряя его износ.
Изношенные шейки ротора восстанавливают хромированием. Шейки возможно ремонтировать и шлифованием, компенсируя уменьшение их размеров установкой дисков (изготовляются из латуни ОФЮ-1, АЖ9-4 и др.), шепетильно подгоняемых к прошлифованным шейкам.
В один момент с шейками шлифуют торцы ротора. Наряду с этим выдерживают допуск на соосность шеек не больше 0,02 мм.
Допустимое биение торцов 0,015—0,02 мм на радиусе в 40 мм.
Существенно изношенные лопатки заменяют новыми, изготовленными в соответствии с техническими условиями.
Так, ремонт лопастных насосов есть достаточно трудоемким и исходя из этого во многих случаях не редкость более выгодно заменить изношенные насосы новыми. Ремонт целесообразно создавать лишь при необходимости устранения малых недостатков, к примеру, в то время, когда ослабляется сальниковое уплотнение либо в то время, когда необходимо поменять шарикоподшипники.
Отремонтированный насос, испытывают на стенде либо конкретно на станке, обкатывая его на холостом ходу в течение -20 мин. При отсутствии неисправности испытывают насос под нагрузкой, неспешно повышая давление до номинального и после этого превышая на 30%.
Наряду с этим большом давлении контролируемый насос обязан трудиться не более 3—5 мин. При опробовании насоса замеряют производительность при разных давлениях и тем самым определяют К п’Д., применяя для этого особое приспособление.