Способы изготовления керамических стержней
Керамические стержни изготовляют разными методами, к примеру сухим либо полусухим прессованием, прессованием под большим давлением, прессованием под максимально большим-давлением и при громадной скорости (прессование взрывом), изостатическим прессованием, изостатическим горячим прессованием, литьем, центробежным литьем, вибрационным уплотнением, шприцеванием под давлением (запрессовкой) и в некоторых случаях (при изготовлении трубочек из кварцевого стекла) вытяжкой.
В соответствии с литературным данным керамические стержни изготовляют практически всеми методами, каковые употребляются для того чтобы в других отраслях индустрии (выдавливанием, трамбовкой, литьем и т. п.).
Выбор разработки изготовления стержней определяется в основном формой стержней и их требуемым числом.
Изготовление стержней надувкой, либо выстреливанием. В работе приведена смесь для того-чтобы, складывающаяся из жидкого силиката и кварцевого песка натрия.
Сперва стержни отверждают углекислым газом, после этого отвержденные стержни пропитывают гидролизованным раствором этилсиликата 40 в спиртовой среде и совсем высушивают. По данным другого источника стержни изготовляют подобным методом, но вместо кварцевого песка применяют цирконовый.
Надувкой, либо выстреливанием, возможно изготовлять небольшие стержни несложной формы с низкой размерной точностью.
Изготовление стержней запрессовкой. Состав для стержней складывается из молотого огнеупорного материала и пластических связующих. Смесь размешивается в смесителе с подогревом при помощи паровой рубахи.
По окончании охлаждения отвердевшую массу измельчают, вакуумируют и выдавливают шприц-машиной. По окончании охлаждения массу разламывают на гранулы, пригодные для заполнения запрессовывающих станков.
Запрессованные гранулы некое время охлаждаются в пресс-форме, по окончании чего стержень отправляют на тепловую обработку для удаления из них пластификаторов. Стержень медлительно с тщательным соблюдением режима нагревают до температуры около 320 °С в течении 72 часов в зависимости от формы и величины изделия.
Огнеупорная смесь наряду с этим методе изготовления имеет частицы величиной максимум 0,1 мкм. Органическое связующее, правильнее, пластификатор, имеет точку плавления до 200 °С при давлении пара 133 Па (1 торр).
Пластификаторами смогут быть нафталин, камфара либо парадихлорбензен, каковые используют числом jg_32%. По окончании удаления этого связующего стержни при необходимости обрабатывают, зачищают и обжигают при соответствующей температуре в зависимости от состава смеси (в большинстве случаев при 1200 °С).
По окончании обжига стержни шлифуют и полируют.
Запрессовкой возможно приобретать и тонкостенные стержни со стенками толщиной 0,2—9,5 мм независимо от сложности формы. Производительность от 20 до 200 запрессовок.
Так как стержни по окончании запрессовки не всегда прочные, то их прокаливают в профилированных сушителях либо укладывают на песчаную постель, к примеру из корунда. Последним методом изготовляют стержни в НИИ керамических смесей (Градец Краловы) с точностью ±1%.
Стержни с узкими размерными допусками приобретают обработкой предварительно либо совсем обожженных стержней. Шлифованием получают размерной точности в пределах до 0,02 мм с чистотой поверхности 1—1,2 мкм.
Изготовление стержней прессованием. Сухие либо полусухие смеси прессуют значительно чаще на простых прессах либо прессах с изо-статическим прессованием при давлении 20—150 МПа. Формы изготовляют из спеченных карбидов вольфрама.
Стержневую прессуемую смесь, которая складывается из огнеупорной составляющей связующего и смазки, засыпают в пресс-форму в виде гранул. В качестве связующего и смазки применяют воски, поливиниловый спирт, стеарины, полиэтиленпарафин, декстрины и т. п. Сухое прессование считается (согласно данным технической температуры) самоё эффективным и производительным методом формообразования огнеупорных материалов.
Полусухое прессование отличается от сухого тем, что прессуемая смесь содержит 5— 25% жидкости; давление запрессовки в пределах 3,5—17,5 МПа. Такое довольно низкое давление разрешает применять пресс-формы из закаленной стали.
Процесс прессования полусухих весов легко механизируется.
При изостатичесром прессовании давление равномерно распределено на все части прессуемых стержневых смесей. Исходя из этого пресс-формы возможно изготовлять из эластичных материалов, к примеру резины.
Данный метод изготовления стержней еще лишь начинается и его тяжело механизировать.
Для получения окончательной формы стержни в большинстве случаев обрабатывают. Температуру обжига стержней принимают в зависимости от состава стержневой смеси, требований к стержням в пределах 850—1780 °С.
Дабы при обжиге не происходило громадных объемных трансформаций и дабы стержни легко удалялись из отливок выщелачиванием, их обжигают при температуре 1200—1250° С 135]. Последующую отработку, к примеру полирование, в большинстве случаев создают по окончании предварительного спекания.
Сухое прессование разрешает приобретать без дополнительной обработки цилиндрике стерженьки диаметром 1,3—4,0 мм с размерной точностью —0,025 мм. К сожалению, данный метод пригоден лишь для стержней несложной формы.
Более сложные стержни возможно изготовлять обработкой предварительно обожженных стержневых заготовок. При прессовании полусухих смесей точность стержней ниже.
Изготовление стержней литьем. Суспензии огнеупорных материалов в воде смешивают с веществами, увеличивающими жидко-подвижность суспензии и разрешающими заливать их в гипсовые формы.
Эти вещества — жидкое стекло, ортофосфаты, хлорид алюминия и т. п. Требуемая величина рН выдерживается при помощи соляной кислоты либо кислого углекислого аммония. Данный метод изготовления стержней запатентован как метод RAM.
Смесь (консистенции глины для гончарного круга) вводится в стержневые гипсовые коробки и иногда подпрессовывается. Стержневые гипсовые коробки вставляют в металлические обечайки и делают в них отверстия засунутыми хлопчатобумажными пробками.
При прессовании выдавливаемая из стержневой массы вода через эти пробки удаляется наружу и обезвоженная стержневая смесь затвердевает в гипсовом стержневом коробке.
Таким методом экономически целесообразно изготовлять только простые стержни. Для сложных стержней требуются дорогие стержневые коробки с выталкивателями, дабы возможно было извлекать стержни без повреждений.
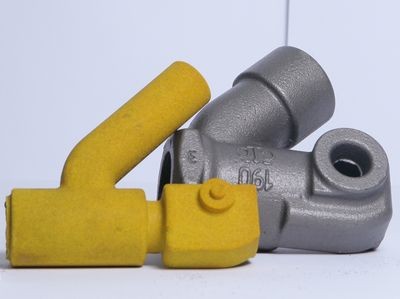
Смесь по окончании заполнения ею стержневого коробки возможно вакуумировать с целью предупреждения образования в ней воздушных пузырей.
Стержни возможно изготовлять кроме этого литьем в железных либо в пластмассовых стержневых коробках. В случае если связующим в стержневой смеси есть алкозоль гидролитических продуктов этилсиликата 40, то концентрация в связующем должна быть более 20%.
В качестве гелеобразователя — катализатора пригоден алюминат кальция числом до 10% от массы огнеупорного материала. Необработанные стержни имеют точность ±0,75% и громадную газопроницаемость (пористость около 25%).
В случае если же связующим есть гидрозоль кремнезема, то самоё технологичным гелеобразующим катализатором есть маленькая присадка амина, к примеру, диэтилентриамина (0,05% от количества применяемого огнеупорного материала). Отверждения смеси возможно достигнуть ее замораживанием при низких (до 6 °С) температурах.
Метод пригоден для изготовления несложных стержней малыми сериями. Его применяют литейные цехи правильных отливок.
Изготовление стержней виброуплотнением. Данный метод изготовления стержней подобен прессованию.
Громаднейшее уплотнение стержневой смеси достигается при частоте 2,5—4,0 кГц. В соответствии с патенту керамические стержни приобретают заливкой стержневой суспензии из огнеупорных материалов с гидролизованным этилси-ликатом в выплавляемые модели, служащие необычными стержневыми коробками.
После этого модели с залитой керамической массой подвергают вибрации. По окончании затвердевания получается стержень.
Изготовление стержней выдавливанием. Этим методом изго-готовляют по большей части стержни цилиндрической формы. По литературным данным, данный метод применяет компания Austenal (США).
К выдавливаемым, правильнее, вытягиваемым стержням относят кроме этого трубочки из кварцевого стекла. Их применяют в качестве стержней при получении отверстий диаметром 0,5—2,5 мм.
Эти трубочки смогут быть изогнутыми и соединенными (пайкой либо сваркой) в сложнейшие стержни для получения искривленных и лабиринтных каналов в отливках. Их удаляют из отливок достаточно легко выщелачиванием в расплавленном едком натре.
Трубочки из аморфного кварцевого стекла изготовляет национальное предприятие Kavalier Sazava (ЧССР).
Преимущества применения вставляемых керамических стержней обеспечиваются не только их особенностями, высокой хорошей чистотой и размерной точностью поверхности, но и опытом их применения при формовке.