Выбор метода формовки
В формовочном отделении выполняются операции формовки, сборки, заливки, выбивки и охлаждения отливок, трудоемкость которых образовывает до 60% от общей трудоемкости изготовления отливок. Исходя из этого проектированию формовочного отделения уделяется особенное внимание.
Современные проекты должны предусматривать автоматизацию и максимальную механизацию как отдельных операций, так и всего комплекса работ, делаемых в отделении, связанных технологически и организационно. В таковой связи находятся операции формовки, сборки, выбивки и заливки опок.
Нарушение одной из операций неминуемо ведет к остановке всего участка, а во многих случаях к непроизводительным работам и потерям на вторых участках производства отливок.
Кроме этого шепетильно должны прорабатываться транспортные устройства, снабжающие формовочный участок стержнями, смесью, оснасткой и др.
Технико-экономические показатели формовочного отделения, выбор оборудования и организация работы прежде всего зависят от метода изготовления форм, которому уделяется особенное место при проектировании.
Главными факторами, снабжающими выбор способа формовки, являются темперамент производства, развес, класс и габариты точности отливок, род металла, вид производственной программы и мощность проектируемого цеха. В зависимости от указанных параметров используется способ формовки в разовые песчаные формы, литье в кокиль, центробежное, литье под давлением, по выплавляемым моделям и корковое.
Литье в разовые песчаные формы может производиться в сырые и сухие формы. Использование сырых форм разрешает быстро сократить цикл производства отливок, расход горючего, капитальные вложения, повысить производительность при выбивке и формовке.
Сырые формы используются для отливок весом до 500—1000 кг несложной и средней сложности. В массовом и крупносерийном производстве отливки весом до 500 кг рекомендуется создавать в сырые формы, в одном цехе — в независимых потоках развесом до 8,8—50 и 50— 500 кг.
Главным условием для сырой формы есть плотность набивки и минимальное металлостатическое давление. Сырая прочность формы, полученная на прессовых и встряхивающих автомобилях, выдерживает железный напор, создаваемый столбом металла высотой 700—800 мм.
В сырых формах изготовляют небольшие и средние отливки с маленьким числом и весом стержней.
В сухие и поверхностно подсушиваемые формы отливают крупные отливки и средние со большими по количеству и весу стержнями, громадным количеством механической обработки, требующие чистоты поверхности и высокого качества металла. При выборе способа производства отливок направляться иметь в виду, что использование сухих форм приводит к потребности в сушильных печах, удлиняет цикл изготовления отливок, увеличивает парк опок, площади цеха, что в конечном счете удорожает отливки.
Литье в кокиль обширно употребляется в сельскохозяйственном машиностроении, станкостроении, производстве кузнечно-прессового оборудования, авиационной и автотракторной индустрии, вагоностроении, для отливок массового, крупносерийного и серийного производства из тёмных и цветных сплавов. Если сравнивать с песчаной формой литье в кокиль снижает трудоемкость изготовления отливок на 30—40, а себестоимость — на 15—25%.
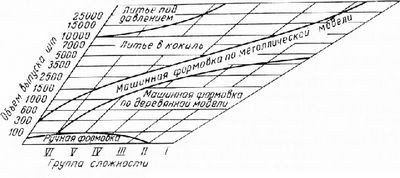
Рис. 1. Диаграмма для выбора оптимального метода изготовления отливок
Литье под давлением используется в крупносерийном и массовом производстве небольших и средних по весу отливок из цветных сплавов и снабжает 3—5-й классы точности, 5—7-й классы чистоты поверхности и минимальную толщину стены отливки 1 мм. Этим методом изготовляются подробности правильных устройств, радио- и электроаппаратуры, самолетов, автомашин, бытовых изделий и др.
Экономия металла если сравнивать с песчаной формой достигает 50% и понижение трудоемкости до 5 раз, а если сравнивать с литьем в кокиль расход металла понижается на 30% и трудоемкость до 2 раз. На данный момент данный метод используется для литья последовательности больших подробностей, а также блоков цилиндров двигателей автомобиля.
Не обращая внимания на высокие технические большую производительность и показатели отливок процесса, использование литья под давлением ограничивается большой длительностью и стоимостью оснастки ее изготовления.
На рис. 1 представлена диаграмма для выбора оптимального метода изготовления отливок из легких сплавов.
На данной диаграмме нанесены границы рентабельного способа применения литья под давлением, в кокиль и различных вариантов литья в песчаные формы в зависимости от размера партии и группы сложности.
Литье по выплавляемым моделям используют для изготовления небольших и сложных подробностей с громадным количеством механической обработки и из дорогих сплавов, тяжело поддающихся механической обработке. Если сравнивать с литьем в песчаные формы литье по выплавляемым моделям снабжает понижение веса отливок на 30—50% и в 3—4 раза сокращает количество механической обработки.
С громадным эффектом данный метод используется для отливки турбинных лопаток разных типов, подробностей швейных автомобилей, ружей и др. На данный момент по выплавляемым моделям возможно делать отливки весом от 1 г до 100 кг с толщиной стенок от 0,15 до 1 мм и больше, но чаще всего этим способом изготовляют отливки весом 50—500 г и длиной до 100 мм.
Началом проектирования формовочного отделения есть разбивка заданной номенклатуры на анализ и весовые группы весовых групп с целью выбора рационального способа изготовления форм. Причем анализ производится с учетом веса отливок, конфигурации, серийности производства и класса точности.
На основании анализа для каждой весовой группы устанавливается рентабельный метод изготовления форм и разрабатывается техдокументация по принятому процессу.
При анализе номенклатуры направляться учитывать не только экономичность изготовления отливки в литейном цехе, но и себестоимость изготовления подробности в целом. Во многих случаях отливка возможно неэкономичной, но понижение трудоемкости механической расхода и обработки металла в конечном счете снижает себестоимость изготовления подробности.
При выборе способа формовки направляться иметь в виду, что главная масса отливок (около 90%) на данный момент изготовляется в песчаных разовых формах. Разъясняется это маленькой ценой изготовления формы, доступностью и большими запасами формовочных материалов, накопленным обширным опытом, наличием площадей, разработкой и усовершенствованием новых технологии и машин.
Способ литья в разовые песчаные формы одинаково пригоден как для массового и серийного, так и для личного производства отливок любой размеров и сложности. Исходя из этого преобладающим остается производство отливок из тёмных сплавов в разовые песчаные формы.
При выборе способа литья в песчаные формы для каждой весовой группы подбирается размер опок, причем раскладка модели на подмодельной плите для каждого размера опок обязана производиться так, дабы коэффициент металлоемкости формы стремился к максимуму.
Коэффициент металлоемкости, т. е. отношение суммарного веса металла в форме к весу формовочной и стержневой массы в опоке, зависит от сложности, габаритов отливки и толщины тела и фактически равен от 0,25 до 1,2.
Имея оптимальный размер опок, подбирают тип автомобилей. На каждую формовочную машину рекомендуется выбирать один, громаднейший размер опок.