Классификация покрытых электродов
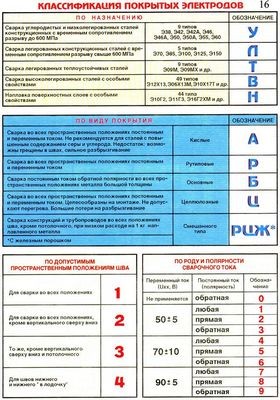
На данный момент у нас для сварки углеродистых и легированных конструкционных сталей используют электроды по ГОСТу 9467—60, в базу которого положены механические особенности наплавленного металла либо сварного соединения, делаемых электродом. Помимо этого, ограничивается содержание фосфора и серы в наплавленном металле.
Тип электрода обозначается буквой Э; следующее за буквой число обозначает нижнее значение предела прочности. ГОСТ предусматривает типы электродов от Э34 до Э145; в случае если по окончании числа направляться буква А, то это указывает, что электрод снабжает повышенные значения пластических особенностей наплавленного металла либо сварного соединения.
Электрод типа Э34 дает малую пластичность и наименьшую прочность металла и относится к электродам с узким стабилизирующим покрытием, допускается лишь в производстве менее важных сварных конструкций; Э42 и Э46 пригодны для важных конструкций из углеродистых сталей, Э50 и Э55 — для среднеуглеродистых и низколегированных сталей; Э60, Э70, Э85, Э100, Э125 и Э145 — для легированных сталей повышенной прочности, причем для типов Э85—Э145 сварное соединение по окончании сварки проходит термическую обработку. Типы Э34—Э70 имеют стержень из проволоки Св-08; Э85—Э145 — из легированной проволоки.
Но электрод одного и того же типа, к примеру Э42, возможно взять с разными покрытиями, придающими электроду значительные технологические изюминки, не отмеченные в ГОСТе. Исходя из этого сохраняется еще марка электродов, устанавливаемая изготовителем электродов и вносимая в паспорт электрода.
Обозначения марок совсем произвольны, и марка может различаться, к примеру, только числом наносимого покрытия при том же составе.
На базе состава покрытия совершена классификация качественных электродных покрытий: ( 1- Руднокислые покрытия содержат окислы марганца и железа (в большинстве случаев в виде руд), кремнезем, много ферромарганца; для газовой защиты территории сварки в покрытие вводят органические вещества (целлюлозу, древесную муку, крахмал и пр.), каковые при нагревании разлагаются и сгорают с образованием смеси защитных газов.
При плавлении электрода идет интенсивная экзотермическая реакция углерода и марганца кислородом окислов, разогревающая сварочную ванну и снабжающая ровную поверхность наплавленного металла с маленькой чешуйчатостью. При громадном содержании марганцевой руды образующийся дым вреден для сварщика и при недостаточной вентиляции может неспешно отравлять его соединениями марганца.
Электроды активно используются в производстве всевозможных изделий из низкоуглеродистых и низколегированных сталей, но на последовательности фирм СССР использование этих электродов ограничено либо не разрещаеться из-за их токсичности.
2. Рутиловые покрытия приобретают большое использование в связи с развитием в Советском Альянсе добычи минерала рутила, состоящего преимущественно из двуокиси титана ТЮ2. В покрытия, кроме рутила, введены кремнезем, ферромарганец, карбонаты кальция либо магния.
Покрытия по технологическим качествам близки к руднокислым, дают лучшее формирование, выделение и меньшее разбрызгивание газов, считаются менее вредными для сварщика. Наплавленный металл соответствует электродам типа Э42 и Э46; электроды смогут использоваться для более важных конструкций из низкоуглеродистых и низколегированных сталей.
3. Фтористо-кальциевые покрытия складываются из магния и карбонатов кальция, ферросплавов и плавикового” шпата. Покрытия именуются кроме этого главными, поскольку дают маленькие шлаки главного характера, а электроды с таким покрытием именуются кроме этого низководородистыми, поскольку наплавленный металл содержит водорода меньше, чем при вторых покрытиях.
Газовая защита ванны обеспечивается окисью и двуокисью углерода, образующимися при разложении карбонатов под действием большой температуры. Электроды чаще употребляются на постоянном токе обратной полярности (плюс на электроде).
Наплавленный металл по составу соответствует спокойной стали, отличается чистотой, малым содержанием кислорода, водорода и азота; понижено содержание фосфора и серы, повышено — марганца (0,5—1,5%) и кремния (0,3—0,6%). Металл устойчив против старения, имеет высокие показатели механических особенностей, а также ударной вязкости, и часто по механическим особенностям превосходит главной металл.
Электроды с этим покрытием рекомендуются для самые ответственных конструкций из углеродистых и легированных сталей.
Электроды с фтористо-кальциевым покрытием в течении многих лет являются наилучшими по качеству наплавленного металла. Чувствительны к наличию окалины, ржавчины, масла на кромках главного металла и в этих обстоятельствах дают поры, как и при отсыревании электродов.
Свойства наплавленного металла возможно поменять в широких пределах, меняя количество ферросплавов в покрытии. Широко известен электрод этого типа, маркируемый УОНИ-13; он имеет пара разновидностей; УОНИ-13/45, УОНИ-13/55 и т. д.; второе число показывает предел прочности наплавленного металла.
4. Органические покрытия складываются из органических материалов, в большинстве случаев из оксицеллюлозы, к которой добавлены шлакообра-зующие материалы, двуокись титана, силикаты и пр. и ферромарганец в качестве раскислителя и легирующей присадки. Электроды пригодны для сварки во всех пространственных положениях на постоянном и переменном токе; малочувствительны к состоянию поверхности и качеству сборки металла, в особенности пригодны для работы в монтажных и полевых условиях.
Дают удовлетворительный наплавленный металл, соответствующий электродам типов Э42—Э50. Активно используются в Соединенных Штатах на монтажных работах; начинают использоваться и у нас.
Приведем пара составов электродных покрытий.
Электроды ОММ-5 — руднокислого типа, предназначены для сварки низкоуглеродистых сталей. Электроды типа Э42 допускаются для изготовления всевозможных важных конструкций из низкоуглеродистых сталей, трудящихся с приложением статических, динамических и переменных нагрузок при обычных, повышенных и пониженных температурах.
Стержень электрода из проволоки Св-08 либо Св-08А. Состав обмазки ОММ-5 приведен ниже.
Титановый концентрат, т. е. обогащенная руда, состоит в основном из минерала ильменита, представляющего собой тита-нат закиси железа FeO -ТЮ2. Марганцевая руда состоит преимущественно из пиролюзита — перекиси марганца.
Полевой шпат — природный минерал — силикат алюминия, калия и натрия. Ферромарганец, используемый для электродных обмазок, в среднем содержит около 70% Мп.
Титановая руда, марганцевая руда, жидкое стекло и полевой шпат, сплавляясь и взаимодействуя с ферромарганцем и металлом, образуют при сварке шлак. Двуокись ‘итана из титановой руды делает шлак маленьким.
Кислород в закиси железа титановой руды и марганцевой руде окисляет ферромарганец с выделением большого количества тепла, разогревает и разжижает шлак, заставляет кипеть ванну.
Щелочи жидкого стекла и полевого шпата повышают устойчивость дуги. Окислы марганца в шлаке уменьшают утрату марганца ванной. Ферромарганец раскисляет и легирует наплавленный металл, восполняя утраты марганца и пара повышая его содержание.
Крахмал, разлагаясь, образует предохранительную газовую оболочку около дуги.
Рутил — природный минерал, состоящий преимущественно из ТЮ2; магнезит — минерал преимущественно из MgC03; декстрин — производное крахмала, добавляется в маленьком количестве для увеличения пластичности обмазочной пасты, что облегчает работу обмазочных прессов. Примером электродов фтористо-кальциевого типа могут служить электроды УОНИ-13 (табл.
4).
Механические особенности сварного соединения характеризуются большой вязкостью и “прочностью, к примеру для УОНИ-13/45 и УОНИ-13/55 ударная вязкость образовывает 25—30 кГм/см что есть очень высоким значением и на большом растоянии превосходит значения ударной вязкости главного металла.
Электроды рекомендуются для сварки в нижнем положении, но вероятна кроме этого сварка в вертикальном и потолочном положениях. Ток постоянный, полярность обратная, т. е. плюс на электроде.
При работе на переменном токе нужно использование осциллятора. Существуют разновидности электродов УОНИ-13, в обмазку которых додают сильные ионизаторы, что позволяет трудиться на переменном токе без осциллятора.
Уровень качества сварки электродами УОНИ-13 направляться признать выдающимся, показатели механических особенностей сварного шва и наплавленного металла получаются довольно часто выше показателей главного металла.
Назначение отдельных компонентов покрытия УОНИ-13 мо“ет быть растолковано следующим образом. Главная составная часть мрамор СаС03 при нагревании разлагается на окись кальция СаО, идущую в шлак, и газ С02, частично восстанавливающийся до СО.
Двуокись углерода С02 создаёт окисляющее воздействие и связывает водород, попавший в зону сварки в пар Н20. Газы С02 и СО фактически нерастворимы в металле.
С02 заполняет территорию сварки, вытесняя из нее воздушное пространство и создавая предохранительную воздух- Окислительное воздействие С02 на металл компенсируется наличием сильных раскислителей в сварочной ванне. Плавиковый шпат CaF2 снижает вязкость шлака и температуру плавления.
При нагревании CaF2 частично разлагается, освобождающийся фтор образует с водородом весьма прочный фтористый водород, не растворяющийся в металле.
Покрытие негигроскопично, не включает компонентов, содержащих водород, и при изготовлении прокаливается при температуре 300—400° С. В следствии содержание водорода в наплавленном металле сводится к нулю, ликвидируя источник трещин и образования пор, оно многократно меньше, чем при рудно-кислых покрытиях. Кварц вводят в покрытие для уменьшения выгорания и разжижения шлака кремния в металле.
ферросилиций и Ферромарганец вводят для легирования металла. Ферротитан с содержанием около 23% Ti вводят как модификатор и сильный раскислитель наплавленного металла; титан в ходе сварки выгорает полностью и в составе наплавленного металла фактически не обнаруживается.
Вес приведенных качественных покрытий образовывает 30—40% веса электродного стержня. Для составления обмазочной пасты к сухой смеси додают 30% водного раствора жидкого стекла плотностью 1,40 либо 12—13% в пересчете на сухой остаток.
Существуют особые электроды, дающие повышенную производительность по наплавленному металлу. Для данной цели в покрытие электродов добавляется металлический порошок, изготовляемый на особых фабриках.
Количество вводимого порошка железа изменяется в различных электродах от 5 до 50% веса электродного стержня и более; вес покрытия может быть около 100—180% веса стержня. Коэффициент наплавки увеличивается до 12—20 г/а-ч против простых значений 8—10 г/а-ч; производительность наплавки возможно увеличена в 1,5—2 раза при том же токе.
Использование высокопроизводительных электродов с металлическим порошком до тех пор пока мало; одна из обстоятельств в том, что довольно часто решающим причиной есть скорость расплавления не электродного, а главного металла.