Контроль изготовления форм
Данный производственный участок особенно серьёзен, поскольку в основном тут определяется уровень качества отливок. На данной технологической операции нужно выдерживать все требования по приготовлению связующего, определению вязкости суспензии, выдерживать предусмотренную зернистость обсыпочного материала.
Величина зерна на протяжении обсыпки изменяется, часть более больших зерен возрастает, поскольку на сыром модельном блоке удерживается в первую очередь небольшая фракция обсыпочного материала. Исходя из этого таковой материал нужно освежать иногда добавками свежего песка.
Нужно кроме этого выдерживать время сушки отдельных слоев оболочки и смотреть за тем, дабы при предстоящих технологических операциях не случилось растрескивания керамических форм.
Свойства материалов, применяемых при изготовлении керамических форм, воздействуют на прочность, газопроницаемость и на тепловое расширение форм. Отклонение особенностей исходных материалов от установленных инструкцией прямым образом отражается на качестве форм при последующих операциях.
Исходя из этого нужно верно измерять прочность при изгибе, газопроницаемость и крайне редко тепловое расширение керамических форм и потребовать поставки лишь качественных исходных материалов.
Прочность при изгибе высушенных керамических форм гарантирует сохранность ее при операциях удаления модельного состава, установки на прокаливание и при транспортировке. Прочность прокаленной керамической формы гарантирует выдерживание допускаемого гидростатического давления заливаемого металла.
Газопроницаемость снабжает хорошее поверхности заполнение и качество отливок форм жидким металлом.
Определение прочности при изгибе керамических форм. Предел прочности при изгибе керамических форм определяют многими методами.
Диттрих и Крингс определяли его при помощи приложения давления на внутреннюю поверхность оболочки (до ее разрушения), выполненной в виде полого шара, куба либо цилиндра. Шефард и Левич изгибали до разрушения плоский пример, изготовленный по принятому в производстве методу получения оболочковой формы.
Фишер и Дитерт испытывали образцы в виде кубиков из затвердевшей суспензии. У керамических огнеупорных изделий прочность на сжатие определяют в большинстве случаев по стандарту CSN 726013.
В литье по выплавляемым моделям чаще всего определяют прочность оболочки на намерено изготовленных примерах. Образцы имеют форму пластинок, их изготовляют многократным нанесением суспензии на выплавляемую модель либо на полосу жести.
Состав суспензии, обсыпочный параметры и материал сушки каждого слоя должны соответствовать принятому технологическому процессу. Образцы извлекают из модели механическим методом либо модель расплавляют.
Высушенные либо прокаленные керамические образцы устанавливают на две горизонтальные цилиндрические опоры ровной стороной. Расстояние между опорами в большинстве случаев неизменно.
К примеру в средней части со стороны обсыпанного песком слоя прикладывается нагрузка до его разрушения. Скорость нагружения примера должна быть равномерной и иметь определенную величину.
В ЧССР принята скорость нагружения 1,5 Н/с.
На этом приборе испытываемые образцы — пластинки поднимаются на двух опорах. Упираясь в середине о расположенную неподвижную призму, они ломаются.
Другие устройства имеют иную схему нагружения. Так, к примеру, в приборе для определения прочности при изгибе керамических материалов по CSN 51030 производства компании Netzsch Geratban, Selb (ФРГ) испытываемый пример — пластинку нагружают снизу подвижной призмой.
Размеры керамических образцов для опробования в различных государствах разны: в ЧССР применяют пластинки размером 100X25X5 мм, в Англии 102,4?25,4?3,2 мм, в ГДР 40?10 мм.
Прочность при изгибе керамических форм определяют в большинстве случаев при обычной температуре. Такое опробование при необходимости возможно проводить при повышенных температурах.
Практическое значение имело бы измерение прочности при 1200—1400° С, но это сделать весьма тяжело.
Диттрих и Крингс определили, что при нагреве до 500° С прочность керамики медлительно увеличивается; большая прочность наблюдалась при 500— 700° С. После этого наступает понижение прочности и при 900° С прочность такая же, как и при обычной температуре.
Прочность при изгибе керамических образцов при увеличении температур выяснил В. Доелман. Образцы — пластинки размером 25,4 X 31,8X X5,6;‘мм [изготовляли нанесением суспензии на железную пластинку, покрытую модельным составом.
Образцы испытывали на приборе для опробования песчаных образцов. Умелые пластинки с опорным устройством вставляли в рабочее пространство трубчатой электрической печи сопротивления.
Рис. 1. Прибор для определения прочности при изгибе керамической оболочки (ЧССР)
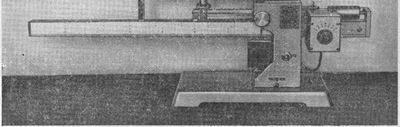
Рис. 2. Прибор для определения прочности при изгибе керамической оболочки
Рис. 3. Схема установки примера для определения прочности при больших температурах
Так как газопроницаемость керамических форм, применяемых в литье по выплавляемым моделям, если сравнивать с газопроницаемостью классических песчано-глинистых форм есть несоизмеримой, ее нельзя измерять на стандартном приборе для измерения газопроницаемости песчано-глинистых формовочных смесей. Исходя из этого направляться изыскивать другие методы измерения и создавать другие устройства.
Шепард и Левич, к примеру, определяли газопроницаемость керамического примера созданием в него вакуума. Поверхность измеряемого примера была равна 1,77 см2.
Комитет по формовочным материалам BICTA создал способ опробования газопроницаемости керамических форм в холодном состоянии при помощи конусной пробы, которая разрешает измерять газопроницаемость с точностью ±10%. Выплавляемая модель, так называемый Лидбеттеровский конус, является цилиндром , переходящий в конус.
Диаметр основания конуса 50,8 мм, высота 76,2 мм; диаметр цилиндрической части 57,15 мм, высота 25,4 мм. Цилиндрическая часть — пустотелая с внутренним диаметром 50,8 мм и высотой 25,4 мм. На конусную пробу наносят нужное число слоев суспензии, обсыпают ее и сушат.
Модель выплавляют и полученный пустотелый керамический пример прокаливают. После этого обрезают абразивным инструментом цилиндрическую часть примера, совершенно верно выдерживая высоту конусной части.
Микрометром замеряют среднюю толщину оболочки и устанавливают пример в кольцевой паз приспособления для измерения газопроницаемости. Кольцевой паз заполнен ртутью, которая снабжает герметичность.
Верхний уровень ртути устанавливается на соответствующей высоте от основания конуса.
В Англии стандартным производственным способом есть определение газопроницаемости посредством конусной пробы.
Об измерении газопроницаемости керамических форм при повышенных температурах указано в работе И. Доелмана. Керамический пример является шаром , от которого отходит керамическая трубка.
Шар вводят в нагретое рабочее пространство электрической печи сопротивления. Открытый финиш трубки, находящийся вне печи, соединяют с прибором для измерения газопроницаемости формовочных смесей.
С подобным прибором трудились кроме этого В. Диттрих и В. Кринге, в то время, когда определяли газопроницаемость керамических форм, изготовленных из молохита и циркона при 900 и 1200 °С. Результаты их измерений при температуре 900 °С приведены на диаграмме.
На данной диаграмме видно, что газопроницаемость формы с повышением температуры значительно уменьшается.
В Англии для измерения газопроницаемости керамических форм в тёплом состоянии применяют керамическую пробу, воображающую собой полый керамический шар с отводной трубкой из плавленого кварца. Трубку шлангом подсоединяют к измерительному прибору, а шаровую пробу нагревают в электропечи.
Моделью для керамической формы помогает пластмассовый шарик (для пинг-понга), к которому приклеивают трубку из плавленого кварца. По окончании прокаливания шарик сгорает.
Измерение теплового расширения. Тепловое расширение керамической формы есть ответственной величиной вследствие того что объемные трансформации керамических форм смогут быть обстоятельством брака и дефектов продукции.
Величина теплового расширения зависит в первую очередь от состава огнеупорных материалов и от режима прокаливания форм. Особенно принципиально важно верно выбрать величину припуска на усадку при изготовлении мастер-модели (в соответствии с известными коэффициентами усадки сплавов, из которых изготовляют отливки).
Нужно учитывать изменение количества формы при кристаллизационных превращениях огнеупорных материалов в промежутке температур прокаливания, сообенно кварца, что самый обширно применяют в литье по выплавляемым моделям. Одна из первых компаний, занимающаяся литьем по выплавляемым моделям (компания Austenal), ввела определение теплового расширения керамических форм в контрольные способы.
Рис. 4. Зависимость газопроницаемости от температуры
Рис. 5. Прибор для определения теплового расширения керамических материалов (тип BS 1902, 1966)
Для измерения теплового расширения керамических форм применяют в большинстве случаев дилатометры горизонтального типа. Таковой прибор обрисован в работе.
Согласно данным автора работы, данный метод пригоден идя измерения теплового расширения при температуре до 1150 °С.
Метод измерения теплового расширения керамических форм был введен в Англии как контрольный. Керамический пример для опробования имеет форму цилиндра длиной 75 мм, его приготовляют заливкой суспензии в бумажную трубку.
Устройство для измерения теплового расширения сконструировано компанией British Ceramic Research Association. Его описание дано в британском стандарте BS 1902 от 1966 г. Это прибор горизонтального типа, его схема представлена на рис.
106.
Керамический пример вставляют в дилатометр в трубочке из кварцевого стекла. Удлинение примера фиксируется цифровым индикатором со шкалой, поделённой на десятые и тысячные доли миллиметра.
Опытный образец нагревают с определенной скоростью (скорость нагрева, установленная британским стандартом SAZ, равна 6° в 60 секунд) и через маленькие промежутки времени регистрируют данные и температуру цифрового индикатора. Такая схема определения теплового расширения керамических форм рекомендуется до температуры не выше 1100 °С.
Опробование при температуре выше 1100 °С требует электрического метода регистрации трансформации длины примера. Подобный прибор обрисован в работе.
Горизонтальный дилатометр с программным тепловым режимом изготовляет компания Netzsch-Geratbau GmbH (ФРГ).