Магнитные методы контроля
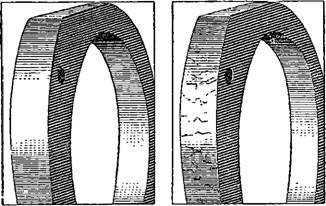
Магнитные способы возможно применять лишь при контроле подробностей из ферромагнитных материалов для обнаружения мест нарушения сплошности материала подробности, расположенных на поверхности и в подповерхностных слоях, а в отдельных случаях — и в подробности, т. е. трещин (усталостных, шлифовочных, закалочных, сварочных, ковочных, штамповочных), волосовин, закатов, расслоений (непараллельных поверхности), флокенов, надрывов, непроваров в сварных соединениях, неметаллических включений. Возможно применять эти способы для обнаружения ферритных включений в подробностях из аустенитных сплавов.
Магнитными способами возможно корректировать отдельные технологические процессы изготовления подробностей (шлифование, термическую обработку, сварку, ковку, штамповку, протяжку и др.).
Благодаря высокой чувствительности, объективности, быстроте и простоте операций, надёжности определения и чёткости дефектов магнитные способы взяли громадное распространение в индустрии. Их преимуществом есть кроме этого возможность контроля подробностей сложной любых размеров и формы.
Магнитные способы контроля развивают в двух направлениях: с применением в качестве индикаторов ферромагнитных порошков либо электромагнитных и электронных совокупностей. Разглядим магнитопорошковый, магнитоферрозондовый и магнитографический способы.
Магнитные способы контроля ферромагнитных подробностей основаны на явлении происхождения магнитного поля рассеяния на поверхности намагниченной подробности в местах размещения недостатков (нарушение сплошности материала либо наличие включений с другой магнитной проницаемостью). В случае если на поверхности намагниченной подробности создается магнитное поле рассеяния, значит в данном месте подробности, возможно, имеется недостаток.
Для намагничивания изделий возможно применять переменный, постоянный, выпрямленный одно-, двухполуперйодный трехфазный ток, и импульсный ток. Переменный ток самый действен для обнаружения поверхностных недостатков, поскольку воздействие магнитного поля ограничивается поверхностными слоями изделия.
Переменный ток нужен и для размагничивания подробностей. Для обнаружения подповерхностных недостатков предпочтительнее постоянный ток, поскольку создаваемое им магнитное поле попадает глубоко в изделие и более равномерно распределяется по всему сечению подробности.
Однополу-периодный выпрямленный ток действен для обнаружения подповерхностных и поверхностных недостатков при магнитопорош-ковом методе контроля. Выпрямленный двухполупериодный и трехфазный ток по характеру создаваемых магнитных полей близки к постоянному току.
Громадное значение для обнаружения недостатков имеет верный выбор- напряженности магнитного поля, которая зависит от расположения и формы предполагаемого недостатка, и магнитных черт материала контролируемого изделия. Через чур высокая напряженность магнитного поля может привести к осаждению ферромагнитного порошка по всей поверхности изделия и появление «фальшивых» недостатков, недостаточная напряженность ведет к уменьшению возможности обнаружения подповерхностных недостатков и понижению чувствительности способа при обнаружении небольших поверхностных недостатков.
Магнитопорошковый способ — один из самый распространенных способов магнитного контроля. Его применяют для обнаружения поверхностных нарушений сплошности шириной у поверхности 0,001 мм и более, глубиной 0,01 мм и более.
Чувствительность способа увеличивается при применении флуоресцирующего магнитного порошка (магнито-люминесцентный способ). В этом случае минимальная ширина у поверхности выявляемого недостатка 0,0005 мм, а протяженность его в глубь изделия 0,005 мм.
При контроле изделий магнитопорошковым способом магнитные поля рассеяния, появляющиеся на поверхности контролируемых изделий в местах нарушения сплошности, выявляют с применением ферромагнитного порошка. Над местом нарушения сплошности материала изделия накапливаются ферромагнитные частицы.
Площадь, занимаемая порошком, намного больше площади недостатка, исходя из этого возможно распознать весьма незначительные по размеру недостатки, что имеет громадное практическое значение.
Эффективность способа определяется свойством магнитных частиц перемещаться под действием магнитных полей рассеяния. В ходе нанесения на подробность ферромагнитные частицы находятся во взвешенном состоянии в воздухе («сухой» способ) либо в таких жидкостях, как минеральное масло, керосин либо вода, т. е. в виде суспензии («мокрый» способ).
Для повышения подвижности частиц сухого порошка его возможно 164 распылять в виде облака, наряду с этим изделие время от времени встряхивают.
Преимущества магнитопорошкового способа: возможность контроля любого , изделия, изготовленного из ферромагнитного материала; обнаружение с достаточной степенью надежности всех нарушений сплошности материала изделия, расположенных на поверхности либо вблизи нее; высокая чувствительность; высокая методики производительность и простота контроля; возможность применения портативного оборудования.
МагнитОпорошковый способ допускает контроль подробностей, по окончании оксидирования, окраски либо нанесения гальванического покрытия (цинка, кадмия, хрома и др.) при условии, что толщина немагнитного покрытия не превышает 80 мкм. При более толстых покрытиях над недостатком создается весьма не сильный поле рассеяния.
Магнитопорошковым способом не советуют осуществлять контроль сварные швы ферромагнитных изделий, полученные с применением электродов из аустенитной стали, поскольку ферромагнитный порошок может осаждаться на границе аустенит-ного шва (мнимые недостатки).
Недочёты магнитопорошкового способа: возможность контроля лишь изделий из ферромагнитного материала; необходимость применения особого оборудования; невозможность обнаружения недостатков, расположенных на глубине более 2 мм от поверхности, и недостатков под немагнитными покрытиями толщиной более 80 мкм при применении магнитной суспензии. На возможность обнаружения недостатка воздействуют многие факторы, а также его очертания, глубина и ориентация залегания.
Магнитноферрозондовый способ создан при изыскании несложных способов обнаружения ферромагнитных включений в неферромагнитных материалах. В следствии были созданы магниточувствительные датчики — феррозонды, разрешающие измерять однородные и неоднородные магнитные поля.
Способ контроля основан на измерении и обнаружении магнитных полей, среди них и полей рассеяния, появляющихся в зоне недостатков, посредством феррозондов — магнитодинамиче-ских магнитометров. Магнитометр — это прибор, разрешающий обнаруживать и измерять, магнитные поля, и определять степень намагниченности ферромагнитного тела по создаваемому им в пространстве магнитному полю.
Преимущество способа — возможность посредством феррозондов, используемых в дефектоскопии, выявлять и измерять весьма не сильный магнитные поля маленьких размеров.
С применением феррозондов возможно:
— выявлять нарушения сплошности в изделиях и ферромагнитных материалах из них, причем не только поверхностные и подповерхностные, как при магнитопорошковом способе, но и удаленные на 10—15 мм от поверхности изделия, что есть значительным преимуществом данного способа;
— осуществлять контроль и сортировать металлические подробности (среди них и машинально) по твердости (по окончании термической обработки) ;
— осуществлять контроль толщину цементованного, азотированного и поверхностно-закаленного слоя изделия;
— делать выводы о прочности кристаллической решетки жёсткого раствора, дисперсионном твердении и т. п.;
— приобретать качественную и количественную характеристики магнитных особенностей материала изделия, по которым возможно делать выводы о структуре и механических особенностях при магнитострук-турном анализе;
— измерять толщину стенок сложных листов и отливок громадной площади из неферромагнитных материалов;
— определять наличие магнитной фазы в немагнитных сплавах, ферромагнитных примесей и темперамент их распределения в цветных сплавах или других немагнитных материалах, выявлять остаточный аустенит;
— определять степень размагниченности изделий, подвергаемых магнитному контролю либо шлифованию на плоскошлифовальных станках с магнитными столами.
Магнитографический способ контроля рекомендован для обнаружения мест нарушения сплошности материала в сварных швах трубопроводов, листовых конструкций и резервуаров из ферромагнитных материалов. В качестве индикаторов магнитных полей рассеяния используют магнитную ленту.
В зависимости от используемого типа магнитографического дефектоскопа возможно осуществлять контроль сварные швы с толщиной свариваемого материала до 16 мм. Этим способом прекрасно выявляют поверхностные трещины.
Внутренние недостатки (газовые и неметаллические включения, непровары и т. п.) выявляют , если их размеры составляют примерно 8—10% толщины контролируемого шва.
Магнитографический контроль пребывает в намагничивании территории контролируемого сварного шва для над недостатком магнитного поля рассеяния, «записи» магнитного поля недостатка на магнитную воспроизведения и ленту «записи» на ленте. При воспроизведении «записанных» на ленте магнитных полей определяют размеры и расположение недостатков.
Для намагничивания, в большинстве случаев, используют постоянный ток, поскольку нужно выявлять по большей части внутренние недостатки. Напряженность магнитного поля в большинстве случаев выбирают экспериментально для четкого обнаружения характерных недостатков минимально допустимых размеров.