Пайка в печах с восстановительной атмосферой
Пайка ведется в особых печах с электрическим обогревом в воздухе газов, владеющих восстановительными особенностями по отношению к окислам главного металла. Довольно часто в качестве восстановительного газа используется водород, исходя из этого метод данный время от времени именуют пайкой медью в воздухе водорода, либо водородной пайкой.
Метод, в большинстве случаев, не требует применения флюса, что есть ответственным его техническим преимуществом, удешевляющим пайку и снижающим трудоемкость процесса, поскольку не нужно операции нанесения флюса на удаления остатков и место пайки флюса по окончании процесса пайки.
Собранные подробности с припоем, помещенным около шва, проходят через электрическую печь с восстановительной воздухом, которая защищает металл от окисления, восстанавливает имеющиеся окислы и усиливает смачивание металла припоем. Расплавляющийся припой смачивает поверхность металла, расплывается по ней и действием капиллярных сил всасывается в шов, сплавляясь с главным металлом..
После этого подробности поступают в камеру охлаждения с восстановительной воздухом, где остывают до температуры, при которой подробность, выданная из печи, при соприкосновении с атмосферным воздухом не окисляется, цвет металла не изменяется, и паяные подробности выходят из печи с чистой, яркой поверхностью.
Процесс пайки очень экономичен, снабжает плотность и прочность соединений, точность размеров, хороший вид и позволяет прочно соединить металлы разных толщин, а в известных пределах — и разнородные металлы.
В массовом производстве используются печи туннельного типа, довольно часто с конвейерами, проходящими через печь. Собранные подробности с припоем укладывают на конвейер и подают в камеру предварительного подогрева, где они неспешно нагреваются до температуры пайки.
После этого подробности поступают в рабочую камеру, где находятся столько времени, сколько нужно для осуществления процесса пайки, полного расплавления припоя, восстановления окислов, всасывания припоя в смачивания и зазор соединения припоем всей поверхности пайки. На это требуется в общем итоге пара мин..
По окончании процесса пайки подробности из рабочей камеры поступают в камеру охлаждения, где неспешно температура их понижается до температуры, разрешающей выдать их из печи без опасности окисления атмосферным воздухом. При пайке медью температура в рабочей камере поддерживается в пределах 1100—1200 °С (в среднем 1150 °С).
Защитный газ подается в избытке и формирует в печи некое избыточное давление, ликвидирующее возможность проникновения вовнутрь печи наружного атмосферного воздуха и опасность взрыва, избыток газа выходит через контрольные трубки и сгорает, соприкасаясь с наружным воздухом.
Первоначально в качестве защитного газа для печей использовался технически чистый водород. Данный газ дает хорошие результаты, но не всегда имеется на месте; он достаточно дорог и очень взрывоопасен, образуя с воздухом смесь громадной взрывчатой силы.
На данный момент пользуются более недорогими и менее взрывоопасными смесями, как к примеру диссоциированным аммиаком, дающим при разложении смесь из 25% водорода и 75% азота. Эта смесь менее взрывоопасна, чем чистый водород и во многих случаях стоит дешевле водорода.
Используют кроме этого смешанный газ, производимый химической индустрией для производства аммиака и воображающий собой смесь водорода с азотом. Особенно обширно пользуются на данный момент природными газами, в большинстве случаев воображающими по составу более либо менее чистый метан СН4.
Ввиду взрывоопасности чистого метана его предварительно обрабатывают с целью получения менее взрывоопасной смеси. Сущность обработки содержится в том, что в метан додают некое количество воздуха, сжигаемого при входе в камеру с метаном.
В следствии получается газовая смесь достаточно сложного состава, содержащая, наровне с метаном, водород, окись углерода, азот и углекислоту. Изменяя количество вводимого воздуха, возможно взять газовую смесь, владеющую достаточными восстановительными особенностями и одновременно с этим фактически практически надёжную в отношении взрыва.
Припой для пайки в водороде возможно в виде проволоки, фольги, порошка либо пасты. Значительно чаще используется фольга и проволока (рис. 241). Для металлических подробностей припоем в большинстве случаев помогает чистая электролитическая медь марки Ml либо М2.
Электролитическая медь очень жидкотекуча в восстановительной воздухе, дает прочное чистое соединение, не требует применения флюса, за исключением некоторых не хорошо смачиваемых сортов стали.
Флюсы требуются при содержании в стали более 1—2% хрома марганца, кремния, алюминия и ванадия, образующих окисные пленки, не восстанавливаемые газовой воздухом и ухудшающие смачивание. Никель, напротив, усиливает смачивание и есть желательным элементом в сталях для пайки.
Время от времени в качестве припоя употребляется латунь, которая в большинстве случаев требует применения флюса для растворения окисления и уменьшения цинка появившейся окиси. В ходе пайки бронзой может увеличиваться температура плавления ее благодаря испарения части цинка.
С флюсом латунь растекается практически так же прекрасно, как и чистая медь.
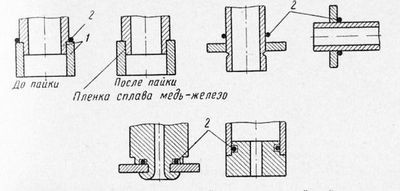
Рис. 1. Формы соединении для водородной иаики: 1 — сталь; 2 — кольцо бронзовой проволоки
Для пайки меди, бронзовых сплавов, чугуна и нержавеющих сталей, не допускающих большого нагрева, используются легкоплавкие серебряные либо бронзовые припои, причем припои для тёмных металлов не должны иметь фосфор.
Для алюминиевых сплавов и пайки алюминия используются особые алюминиевые припои с температурой плавления около 620 °С со большим содержанием кремния в сочетании со особыми легкоплавкими флюсами. Нормально температура рабочей камеры печи превышает температуру плавления припоя на 50—80 °С.
Для главного металла, на что перегрев не оказывает вредного действия, при тщательном контроле нагрева температуру возможно повышать на 200—250 °С, что позволяет существенно форсировать процесс и повысить производительность печи.
При пайке медью рекомендуются зазоры не больше 0,02—0,1 мм, где вероятно направляться использовать плотную посадку соединяемых частей. При пайке легкоплавкими припоями рекомендуются зазоры в пределах 0,025—0,075 мм.
При пайке низкоуглеродистой стали медью прочность соединения на растяжение образовывает около сорока килограмм/мм2; для сталей повышенной прочности смогут быть достигнуты более высокие значения.
В зоне пайки происходит обоюдная диффузия припоя в главный металл и главного металла в припой. медь и Железо имеют ограниченную обоюдную растворимость, в пределах около 4% при температуре плавления меди.
При понижении температуры растворимость меди в железе и железа в меди понижается. Железо выпадает в мелкодисперсном виде, часть же его по окончании охлаждения остается в меди в виде переохлажденного жёсткого раствора.
Количество железа, оставшегося в растворе, зависит от скорости охлаждения: чем выше скорость, тем больше железа остается в растворенном виде (в среднем 1—2%).
Наличие железа в растворе, а также в свободном мелкодисперсном состоянии повышает прочность сплава и механическую прочность пайки, появившегося в месте пайки, приблизительно в 2 раза превышает прочность чистого припоя — меди. Прочность пайки легкоплавкими бронзово-цинковыми либо серебряными припоями на 10—15% ниже прочности пайки чистой медью.
Для процесса пайки используются электрические печи сопротивления с нихромовыми нагревателями, с автоматическим регулированием электрической мощности и температуры.