Пайка волной припоя
На данный момент в индустрии еще активно используется пайка вручную, не обращая внимания на то, что каждый год должны быть сделаны миллиарды таких соединений. Данный процесс есть не экономичным и трудоемким.
Долгое время упрочнения были направлены на механизацию процесса пайки. Наконец, был создан механизированный способ пайки, что разрешает приобретать миллионы надежных соединений компонентов.
Как технологические параметры, так и совокупность пайки являются комбинацией факторов, каковые как совместно забранные, гак и любой но отдельности оказываот значительное влияние на надежность электрических межсоединений.
Данный параграф посвящен, по большей части, практическим правилам, каковые разрешают обеспечить надежность паяных соединений. Компоненты на плате должны размешаться равномерно, так, дабы избежать влаги и накопления пыли, а их форма не должна допускать накопления испарений и флюса в ходе пайки платы волной припоя.
Пайка, сушка, применяемые флюсы не должны загрязнять компоненты, оказывать влияние на трансформацию их формы либо характеристики. Помимо этого, флюс не должен попадать в толщу платы и затруднять обычную работу блока.
Материал платы обязан удовлетворять условиям работы при повышенной температуре при применении компонентов с громадным тепловыделением, а соединительные выводы либо провода должны размешаться как возможно ближе к стенке отверстия и токо-ведущей дорожке. Массивные компоненты должны быть надежно прикреплены к проводящей стороне платы.
Паяные соединения на плате должны выдерживать некое напряжение при действии ударной нагрузки, но разумеется, что существует некий предел, что будет зависеть от формы и массы компонентов, окружающих условий и числа выводов. В большинстве случаев, компоненты с коаксиальными выводами массой до 14 г смогут устанавливаться на плате без особой фиксации, но и в этом случае нужно учитывать конкретные условия.
Расстояние между проводящими дорожками, изгибами и т. д. должно быть выбрано таким, дабы не допустить образование мостиков припоя в ходе пайки погружением либо волной припоя. Помимо этого, нужно учитывать случаи, в то время, когда выводы компонентов смогут выступать либо перекрывать края проводящей дорожки.
В большинстве случаев механизированная пайка проводится в течение 1 … 2 с при температуре 250°; а вручную, паяльником, в течение 1 с при температуре около 320°С. Необходимо иметь в виду, что массивные выводы смогут за это время не достигнуть температуры пайки, в частности в ходе пайки волной припоя.
направляться кроме этого учитывать теплоемкость компонентов, каковые находятся в контакте с выводами.
Ультразвуковую очистку собранных плат необходимо создавать на заблаговременно выбранных и проверенных режимах, дабы избежать выхода и резонансных эффектов плат из строя. Очистку раствором трихлор-этилена кроме этого возможно создавать при условии, что все компоненты по техническим условиям смогут выдерживать подобные действия.
Исходя из этого на стадии проектирования блока нужно шепетильно проверить, смогут ли выбранные компоненты выдержать изгиб выводов, рабочую температуру пайки, воздействие флюса, растворителей либо ультразвуковую очистку.
В определенных случаях требуется удалить покрытие с предварительно луженых выводов компонентов, которое в большинстве случаев уже окислилось, и опять покрыть выводы припоем, для получения необходимой прочности и надёжности соединений.
Изучение некоторых типов выводов продемонстрировало, что покрытие припоем и окионая пленка отрываются при нагреве вывода от пайки волной припоя. При повторном лужении выводов компонентов погружением в тёплый припой возможно значительно улучшить плотность припоя на выводе, но для этого требуется действенная механическая очистка вывода перед повторным лужением.
Для образования хорошего металлургического соединения между выводом компонентов и слоем припоя поверхность должна быть очищена перед предварительным лужением либо пайкой волной припоя. Это относится как к чисто бронзовым, так и к золоченым либо предварительно луженым выводам.
На шепетильно очищенной и подготовленной поверхности образуется интерметаллическое соединение, покрытое узким, ровным и однородным слоем припоя. Неравномерная подготовка поверхности ведет к появлению недостатка соединения.
Очень много отказов связано с образованием не хорошо смачиваемых припоем площадок. Это ведет к образованию не сильный железных соединений и нехороших электрических контактов.
Их появление, в большинстве случаев, не связано с параметрами технологического оборудования, осуществляющего пайку волной припоя.
соединения и Печатные платы
Ниже приводятся кое-какие советы, нужные для пайки волной припоя:
— при проектировании плат следует по возможности равномерно распределить компоненты и параллельно располагать проводящие дорожки;
— избегать более трех проводящих дорожек, соединяющихся под углом менее 45°;
— сохранять однообразный размер проводящих дорожек и смотреть за тем, дабы они превышали диаметр выводов компонентов;
— избегать резких изгибов проводников;
— выводы компонентов должны быть отогнуты в направлении прохождения проводящих дорожек и после этого опять поджаты к плате;
— перед пайкой волной припоя проводить предварительное лужение;
— избегать Применения бронзовых контактный площадок излишней площади;
— избегать пересечения узкой проводящей дорожки с дорожкой, которая имеет вдвое громадную ширину.
Конфигурация выводов, продемонстрированная на рис. 1, есть оптимальной для пайки печатных плат волной припоя.
Незагнутые выводы, и выводы, загнутые под прямым углом, дают хорошие, ровные спаи. Выводы, загнутые под прямым углом на обратной стороне платы, снабжают наивысшую надежность соединения.
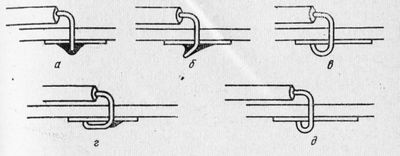
Рис. 1. Конфигурация выводов: а — вывод согнут под прямым углом к обратной стороне платы, слой припоя равномерный; б — вывод изогнут под углом к обратной стороне платы, слой припоя удовлетворительный: а — вывод изогнут по кругу, слои припоя удовлетворительны: г—вывод изогнут на протяжении обратной стороны платы, слои припоя ровные, хорошего качества; д — вывод изогнут U-образно. слои припоя неудовлетворительны.
Неприятности, которые связаны с механизированной пайкой, в большинстве случаев, аналогичны, независимо от того, проводится ли пайка струей припоя, волной припоя либо стеканием припоя с платы. Наряду с этим нужно учесть такие факторы, как угол трения, гравитационные силы и поверхностное натяжение, действующие на жидкий металл. Эти факторы тесно связаны с качеством подготовки поверхности материала и определяют
Погреишости, появляющиеся при применении механизированной пайки. самые характерными недостатками являются происхождение мостиков припоя, образование сосулек и т. д.
Механизированная пайка удачно соперничает с высококвалифицированной ручной пайкой при наличии условий для свободного образования однонаправленной волны припоя. В ходе наладки оборудования нужно отрегулировать форму волны припоя, дабы снизить либо устранить образование мостиков припоя, сосулек, обоюдного соединения, проводящих дорожек, перемычек, образование неровных избытков и кромок припоя.
Оптимальная температура при пайке волной лежит в диапазоне 250…265°С.
Удовлетворительным есть кроме этого способ нанесения флюса посредством волны флюса. Его преимущество если сравнивать с нанесением флюса формованием, накаткой либо вращающейся щеткой содержится в возможности прекрасно сочетать данный способ с существующими процессами производства и в простоте его обслуживания.
Этим способом возможно наносить флюс непрерывно либо дискретно. Оборудование легко в обслуживании.
Оно снабжает хорошее уровень качества нанесения флюса.
Выбор большой либо минимальной температуры предварительного нагрева зависит от применяемого жидкого флюса. Данный предварительный нагрев обязан обеспечить однородный прогрев печатной платы.
Таковой нагрев содействует испарению растворителя флюса, сокращает захват газов их поглощение и флюса слоями припоя, ликвидирует проколы в припое. Через чур сильный нагрев может повредить компоненты и привести к.образованию гребешков припоя, пузырьков и расслоению материала платы.
Для предотвращения коробления платы крайне важно применять регулируемые зажимы, каковые удерживали бы печатную плату по всем краям. Используемые устройства фиксации платы не должны нарушать волну припоя, в противном случае это может оказать влияние на результаты пайки.
Конвейер должен иметь регулируемую скорость, причем одно несущее устройство может переносить набор плат последовательно через посты флюсования, пайки и предварительного нагрева волной припоя при установленной заблаговременно скорости. Изменение данной скорости не должно быть больше 25 см/мин (рис.
2). При подходе к волне припоя конвейер должен иметь наклон.
Рис. 2. Зависимость частоты отказов от скорости перемещения конвейера.
Рис. 3. Зависимость частоты отказов от температуры волны припоя.
Для подачи волны флюса употребляется насосное устройство, которое снабжает постоянную подачу флюса соответствующей высотой волны над выпускным отверстием. Утраты на испарение либо неравномерность потока не должны приводить к образованию гребешков на волне флюса либо пропуску какого-либо участка печатной платы.
При пайке волной припоя тёплый жидкий припой обязан подаваться с постоянной скоростью в постоянном однонаправленном ламинарном потоке, причем над выпускным отверстием направляться всегда поддерживать полукруглую волну заданной высоты. Эта совокупность должна быть создана так, дабы припой смачивал все заданные участки печатной платы и снабжал получение паяных высококачественных соединений .
В зависимости от системы подогрева и ёмкости ванны температура волны припоя обязана сберигаться на уровне 250…265 °С и изменение температуры в волны должно быть сведено к минимуму (рис. 3).