Технология изготовления комбинированного древесного пластика(кдп)
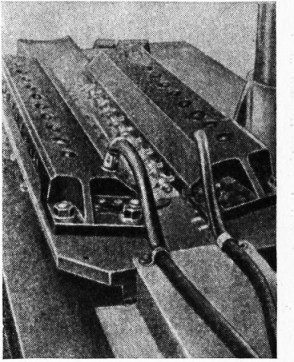
Технологический процесс изготовления комбинированного древесного пластика складывается из операций подготовки шпона и брусков, сборки пакетов, прессования, разделки и обрезки плит их на заготовки.
Подготовка брусков
Березовые чураки либо кряжи разделывают на бруски заданных размеров.
Учитывая, что разделанная на маленькие бруски древесина высыхает стремительнее, чем древесина в долгих заготовках, чураки либо кряжи разделывают на маленькие бруски и складывают их в сухом отапливаемом помещении в штабели с прокладками в соответствии с правилам укладки штабелей для сушки древесины.
При разделке древесины на бруски нужно учитывать пороки древесины. Древесина с пороками распиливается на бруски, предназначаемые для того чтобы комбинированного древесного пластика толщиной более 45 мм.
Бруски для этих плит выпиливаются с таким расчетом, дабы сучки и другие пороки пребывали в средней территории бруска, на расстоянии не меньше 120 мм от его финишей.
Краснина в брусках всецело удаляется методом строгания их на рейсмусовом либо фуговальном станке при поверхностном поражении древесины либо методом опиловки на круглопильном станке при глубоком распространении краснины.
Заготовленные бруски сортируют по ширине на группы так, дабы возможно было взять бруски заданной ширины.
В брусках прямоугольного сечения опиливается одна кромка, а вдруг брусок по ширине подходит к одной из групп,— его совсем не опиливают.
Бруски, имеющие обзол, обрезают либо строгают для придания им удаления коры и прямоугольного сечения.
Подготовленные бруски сортируют по толщине и подают отдельными партиями в камерные сушилки.
Бруски, высушенные на воздухе и имеющие влажность до 14%, употребляются без сушки для прессования плит комбинированного древесного пластика.
Режимы сушки, в зависимости от используемых начальной влажности и сушилок брусков, устанавливаются из расчета обеспечения влажности брусков по окончании сушки в пределах 10—14%.
При сушке бруски укладывают в штабели с сухими прокладками толщиной 25 мм и шириной 30—35 мм, выполняя соответствующие правила укладки. В любой штабель укладывают бруски одной толщины.
Бруски, предназначенные для того чтобы с несклеен-ными брусками, по окончании сушки направляются на сборку пакетов.
Склеенные бруски для прессования монолитных плит, и бруски с трещинами по окончании сушки поступают на обмазку (пропитку) смолой.
Для пропитки либо обмазки брусков используются бакелитовые смолы разных марок концентрацией 40—50%. Для пропитки брусков, имеющих трещины, и брусков с нестрогаными поверхностями используются смолы пониженной концентрации (40—45%).
Бруски со строгаными поверхностями и без трещин пропитываются смолой повышенной концентрации (45—50%).
Бруски пропитываются в ванне: их закладывают в контейнер в вертикальном положении, опускают в ванну со смолой и сразу же вынимают. По окончании стекания избыточной смолы с брусков их укладывают на вагонетку на рейках.
Пропитанные бруски сушат в камерных сушилках по режимам, снабжающим влажность брусков в пределах 10—14%.
Подготовка шпона
Для производства комбинированного древесного пластика используется сухой шпон толщиной от 0,55 до 1,2 мм.
Отобранный шпон пропитывается раствором спиртовой смолы марки СБС-1 либо СКС-1.
время раствора пропитки и Концентрация смолы шпона устанавливаются с таким расчетом, дабы содержание сухой смолы в пропитанном шпоне было не ниже 20%.
Пропитанный шпон сушится в камерных либо конвейерных сушилках по режимам, снабжающим влажность шпона в пределах 8—12%.
Намазывают шпон смолой марки С-1 и сушат по режимам, принятым на фабриках.
Сборка пакетов
Перед сборкой пакетов бруски контролируют по толщине. Для сборки пакета на один промежуток (этаж) пресса допускается отклонение в толщине брусков не более чем на 5 мм.
Пакеты укладывают между железными прокладками. Чтобы не было приклеивания пакетов к прокладкам рубахи пакетов набираются из непропитанного шпона.
Пакеты собирают так, дабы волокна древесины во всех слоях размешались перпендикулярно долгой стороне прокладки. Количество шпона, укладываемого в пакет, должно быть распределено поровну между верхней и нижней частями пакета.
Число слоев шпона определяют расчетом, исходя из средней упрессовки древесины 45%.
Пример. Толщина прессуемых плит 50 мм, средняя толщина брусков 37 мм, толщина шпона 1,2 мм.
Так как упрессовка древесины зависит от ее влажности, количество шпона в пакете проверяется промерами толщины готовых плит и в зависимости от результата число слоев шпона возрастает либо значительно уменьшается.
Пакеты набираются на всю длину прокладки. Время от времени на прокладке возможно собирать пара пакетов однообразной толщины.
Шпон укладывается со стыковкой по боковым кромкам ровным рядом.
По окончании комплекта нужного числа слоев шпона в нижней части пакета на него укладываются три последовательности брусков с плотной стыковкой по боковым кромкам. Бруски должны укладываться без перекосов и не должны свисать со шпона.
Правильность укладки проверяется угольником.
Последовательности брусков должны быть ровными. При комплекте брусков между последовательностями закладывают линейки толщиной 5—8 мм, каковые убирают с пакета по окончании укладки всех брусков.
По окончании укладки брусков на них набирают верхнюю часть пакета из шпона. Верхний слой (рубаха) равно как и нижний, набирают из непропитанного шпона.
По окончании сборки пакет закрывают верхней железной прокладкой и подают в пресс.
При комплекте пакетов с непропитанными брусками между ними и пропитанным шпоном укладывают с каждой стороны брусков по одному слою шпона, покрытого смолой марки С-1.
шпон и Непропитанные рубашки, покрытый смолой марки С-1, входят в неспециализированное число слоев набираемого в пакет шпона.
При комплекте пакета с пропитанными брусками между ними и пропитанным шпоном покрытый смолой марки С-1 шпон не укладывается.
Прессование
Собранные пакеты загружаются в пресс, температура плит которого не должна быть больше 60°.
По окончании центровки и загрузки пакетов плиты пресса смыкаются и дается удельное давление по площади брусков 50—75 кг/см2. В один момент с давлением включается пар.
В то время, когда температура плит пресса достигнет 140°, начинается отсчет времени выдержки (не ранее чем через 40 мин. по окончании подачи давления). Отсчет ведется из расчета 3 мин. на 1 мм конечной толщины прессуемой плиты.
За 10 мин. до окончания выдержки пар перекрывается и выпускается из плит. По окончании выдержки в плиты подается вода для охлаждения.
В случае если температура плит образовывает 35°, то дается дополнительная выдержка из расчета 0,5 мин. на 1 мм толщины плиты.
Неспециализированное время охлаждения, включая выдержку, должно быть не меньше 1 час. 30 мин. для плит толщиной 50 мм и 1 час.
40 мин. для плит толщиной 55—60 мм.
По окончании охлаждения плиты пресса опускают и выгружают спрессованный материал.
Обрезка плит
Плиты разрезаются на заготовки на обрезных станках, по окончании чего заготовки покрываются смолой марки СБС-1 либо СКС-1 40%-ной концентрации либо расплавленным парафином.
Смолой заготовки покрываются методом погружения в ванну либо нанесения смолы на поверхность заготовок кистью. Покрытые смолой заготовки раскладывают на рейки и подсушивают до получения жёсткой пленки.