«Исчезающие» модели и стержни
Большое количество труда затрачивается на изготовление древесных и железных моделей, служащих для получения разъемных песчано-глинистых форм. Помимо этого, их использование снижает точность приобретаемых отливок, поскольку для более легкого извлечения из формы они при изготовлении снабжаются формовочными уклонами, а при формовке — расталкиваются, что увеличивает размеры и объём полости литейной формы.
Принимая к сведенью отмеченные недочеты многократно применяемых древесных и железных моделей, литейщики стали применять так именуемые «исчезающие» модели, по которым возможно взять
лишь одну отливку. особые преимущества и Рациональность разовых моделей заключаются в том, что они позволяют применять неразъемные формы.
Такие формы снабжают высокую точность приобретаемых в них отливок.
В зависимости от способа уничтожения разовых моделей по окончании исполнения технологических функций их принято дробить на выплавляемые и выжигаемые.
Во время ВОВ в связи с необходимостью развития и создания новых конструкций авиационных двигателей появилась острая потребность в освоении производства сложных по конфигурации, правильных по размерам и геометрии отливок из не поддающихся обработке давлением (прокатке и ковке) и резанием жаропрочных сплавов.
Для получения таких отливок была создана ловая разработка литья по выплавляемым моделям применительно к условиям высокомеханизированного и автоматизированного производства, схема которой продемонстрирована на рис. 1.
Для изготовления разовых моделей в современных литейных цехах используют легкоплавкие (с температурой плавления 60-80°) модельные составы, в каковые входят торфяной воск, буроугольный битум, другие материалы и синтетический церезин. Модели либо их звенья приобретают методом запрессовки модельной массы в железные (металлические, алюминиевые) пресс-формы.
Учитывая незначительные размеры создаваемых отливок, много моделей объединяется на неспециализированном стояке. Полученные так модельные блоки покрывают 3—5 слоями огнеупорного раствора — суспензии с последовательной сушкой каждого слоя.
Наряду с этим любой слой суспензии, включающей пылевидный кварц (база) и этилсиликат (связующий материал), обсыпают небольшим, предварительно прокаленным кварцевым песком. Так, на модельном блоке образуется корковая огнеупорная форма с толщиной стены 3—6 мм.
По окончании выплавления из нее модельного блока, что значительно чаще производится в тёплой (90—95°) воде, пара корковых форм заформовывают большим кварцевым песком в железной опоке. Полученные так опочные формы прокаливают в электрической печи при температуре 850-900° для выжигания и упрочения остатков модельной массы.
На данный момент способом литья по выплавляемым моделям приобретают сверхсложные по конфигурации отливки для деталей авиационных двигателей, машин, швейных автомобилей, охотничьих ружей, текстильных автомобилей, центробежных насосов, паровых и газовых турбин из любых сплавов с большими габаритными размерами, достигающими 1 м, массой 0,02—140 кг, с отверстиями при минимальном диаметре до 2 мм, маленькой толщиной стенок, достигающей 0,3 мм.
Громадная точность разовых моделей, приобретаемых по шепетильно изготовленным железным пресс-формам, отсутствие в форме разъемов, и заливка расплава в тёплую форму снабжают высокую точность приобретаемых отливок, соответствующих 3—5-му классам механической обработки.
Pис. 1. Последовательность операций технологического процесса изготовления литья по выплавляемым моделям.
Способ литья по выплавляемым моделям дает громадной экономический эффект при получении очень сложных подробностей. Как пример возможно сослаться на опыт Подольского завода швейных автомобилей имени М. И. Калинина, где использование нового способа произвело коренную ломку разработки и дало очень большой экономический эффект.
Сетка челнока швейной машины, масса которой в готовом виде образовывает 20 г, ранее изготовлялась методом механической обработки — ее точили и фрезеровали из прутка автоматной стали массой 42 г. Переход с механической обработки прутка на литье по выплавляемым моделям устранил 27 операций механической обработки и сократил расход металла на 90%, высвободил на 44% оборудование, разрешил сократить производственные площади на 40%.
На данный момент на многих отечественных фирмах (Столичный, Минский, Горьковский автомобильные заводы и др.) удачно трудятся комплексно-механизированные и автоматизированные цехи, создающие правильные отливки способом литья по выплавляемым моделям. Это произошло благодаря выпуску отечественной индустрией автоматизированного оборудования для изготовление модельных составов, нанесения на модельные блоки огнеупорной суспензии и их обсыпки, и обжига форм.
Директивами XXIV съезда КПСС предусматривается расширить выпуск автомобилей для литья по выплавляемым моделям если сравнивать с 1965 г. на порядок.
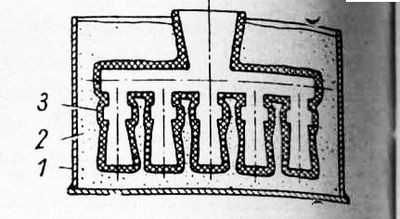
Рис. 2. Форма, полученная по выплавляемым моделям.
Пенополистирол владеет своеобразными особенностями, крайне важными для модельных материалов: он в 5о—100 раз легче дерева, легко режется тёплой проволокой. Склеивая отдельные его куски несложной формы, возможно приобретать модели разной, более сложной конфигурации, отличающиеся громадной точностью, поскольку формовочные уклоны для выжигаемых моделей не необходимы.
Технологический процесс получения отливок по газифицируемым моделям используется чтобы получить отливки массой до 3,5 т из чугуна, цветных сплавов и стали и имеет своеобразные изюминки (рис. 3): полистироловая модель отливки с приклеенными к ней пенополистироловыми элементами литниковой совокупности заформовывается простым методом в опоке песчано-глинистой формовочной смесью, а полученная форма с находящейся в ней моделью заливается расплавом.
Отливка образуется методом заполнения расплавом полости формы, взятой в следствии выжигания им пенополистироловой модели.
Совсем сравнительно не так давно было предложено при литье по газифицируемым моделям применять вместо песчаных смесей ферромагнитные наполнительные материалы — дробь и металлические пески. При таковой технолог;:.: модели из пенополистирола подвешиваются в опоке и засыпаются сыпучим ферромагнитным материалом.
Для лучшего воспроизведения контура модели в форме используется вибрация. Перед заливкой расплава в форме наводится магнитное поле, которое скрепляет частицы формовочного материала и удерживает их на протяжении заливки и кристаллизации расплава до образования на поверхности отливки прочной корки.
По окончании выключения магнитного поля формовочный материал снова делается сыпучим. Его по окончании извлечения отливки охлаждают и опять применяют.
Особенные преимущества нового процесса заключаются в отказе от выбивки форм и трудоёмкой набивки, и исключении операции изготовление песчано-глинистых смесей.
Рис. 3. Схема процесса получения отливки при литье по газофицируемым моделям:
а) — полистироловая модель с литниковой совокупностью; б) — подготовленная к заливке форма; в) — заливка формы расплавом; г) — полученная отливка.
Умело-промышленная проверка рассмотренного технологического процесса литья по газифицируемым моделям при применении ферромагнитных формовочных материалов на фабриках сельскохозяйственного машиностроения продемонстрировала, что масса отливок понижается за счет уменьшения припусков на механическую обработку на 15—30%, а себестоимость 1 т отливок — на 40—60 руб.
Выжигание полистирола при литье по газифицируемым моделям экономически не нужно. Учитывая это, одесский ученый А. Чудновский создал метод восстановления сгорающего полистирола.
Он внес предложение более экономичную разработку литья, при которой формы с пенополистироловыми моделями устанавливают в нагревательную печь для их выжигания, а образующийся наряду с этим газ направляют в змеевик, охлаждаемый проточной водой. По окончании конденсации газа образуется жидкость — стирол, которая является исходным продуктом чтобы получить пенополистирол.
Так, цикл замыкается. Реализация этого изобретения сделает процесс литья по газифицируемым моделям еще более экономичным.
Наровне с выплавляемыми и выжигаемыми — газифицируемыми моделями литейщики применяют разовые «исчезающие» стержни. Так, при получении отливок с каналами и отверстиями маленького диаметра, в то время, когда песчаные стержни не смогут быть использованы из-за трудности их удаления, используют железные целые стержни, сделанные из более легкоплавкого сплава, чем литейный сплав отливки.
По окончании образования и заливки формы прочной корки на оформленной стержнем поверхности отливки железные стержни расплавляются и так создают отверстия, отличающиеся ровной и чистой поверхностью.
В качестве материала стержней для металлических и чугунных отливок применяют латунь, алюминиевые сплавы и латунь.