Электроды с толстым или качественным покрытием
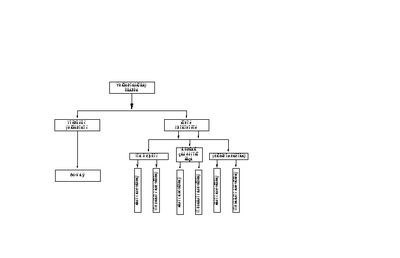
Эти электроды именуют кроме этого качественными. Их легко отличить по внешнему виду: слой покрытия имеет большую толщину, 1—3 мм; вес покрытия 15—60% и более от веса электродного стержня.
Покрытия, кроме стабилизации дуги, защищают сварочную ванну от вредного влияния атмосферного воздуха, улучшают состав, механические свойства и структуру наплавленного металла, снабжают достаточно устойчивое горение дуги.
Базой металлургического процесса при сварке, как и в сталеплавильных печах, есть сотрудничество между металлом и шлаком. Шлак при сварке образуется в основном из расплавленного покрытия электрода, в которое вводят в тонкоразмо-лотом виде разные минеральные вещества, руды, горные породы и т. п. Шлак, образующийся вместе с расплавленным металлом при плавлении электрода, защищает ванну от доступа воздуха; при затвердевании ванны шлак замедляет охлаждение.
При замедленном охлаждении разлагаются нестойкие соединения азота с яшлезом, причем освободившийся азот удаляется из металла, и содержание азота в металле понижается до допустимой нормы 0,01 — 0,03%. Содержание вредных примесей, в особенности фосфора и серы, в материалах для того чтобы доводится до вероятного минимума.
Все материалы должны строго контролироваться по содержанию серы и фосфора.
Существующие разнообразные качественные электродные покрытия смогут быть классифицированы по разным показателям, к примеру по характеру шлака. По составу шлаки, приобретаемые при расплавлении электродных покрытий, смогут быть поделены на кислые и главные.
Наиболее значимыми кислотными окислами в электродных обмазках являются: двуокись кремния Si02 и двуокись титана ТЮ2. Главными окислами являются Na20, CaO, MgO, MnO, FeO и др.
Окислы А1203, Fe203, Сг203 являются промежуточными, нейтральными либо амфогерными. Преобладание кислотных либо главных окислов делает шлак соответственно кислым либо главным.
Кислые шлаки смогут уменьшать содержание кислорода в наплавленном металле, что разъясняется следующим образом. Кислород содержится в расплавленном железе в форме закиси железа FeO, имеющей светло выраженный главный темперамент и реагирующей с кислотными окислами шлака, если они имеются в избытке; образуемые силикаты либо титанаты закиси железа 2Fe0-Si02 и 2FeO -Ti02 в ванне металла фактически нерастворимы.
В следствии происходит постоянный переход закиси железа из металла в шлак, т. е. экстрагирование закиси железа из металла шлаком. Подобный процесс раскисления металла кислым шлаком именуется диффузионным раскислением.
Громадное распространение имеют покрытия, дающие шлаки очень сильно главного характера с громадным содержанием окиси кальция СаО; эти шлаки снабжают получение наплавленного металла особенно большого качества. Шлаки главного характера не создают диффузионного раскисления металла, и для уменьшения содержания кислорода в ванне в обмазки приходится вводить сильные раскислители (кремний, титан) в форме ферросплавов.
По характеру металлургических реакций, протекающих в сварочной ванне, качественные электроды возможно поделить на две группы.
Для стремительного и энергичного проведения аналогичной реакции в обмазку вводят много окислы железа в форме металлических руд или металлической окалины либо же другие окислы, легко отдающие кислород и талантливые интенсивно окислять металл ванны, к примеру двуокись марганца Мп02 в виде минерала пиролюзита. Дополнительным источником углерода, сверх содержащегося по большей части металле, помогает в большинстве случаев ферромарганец, вводимый в большом количестве в подобные обмазки.
Протекающие в ванне экзотермические реакции освобождают большое количество тепла и дополнительно разогревают ванну.
Очень ответственны физические особенности шлака. Температура плавления шлака, как показывает практика, обязана пребывать в пределах 1100—1200 °С.
При температуре плавления стали 1400— 1500 °С шлак обязан владеть малой вязкостью, жидкотекучестью и большой подвижностью, что принципиально важно для верного формирования сварного шва. Значительное значение имеет темперамент затвердевания расплавленного шлака.
Шлаки не имеют строго определенной температуры плавления. При увеличении температуры вязкость шлака неспешно падает, а при понижении возрастает. Переход от жидкого состояния к жёсткому возможно
растянут на большой температурный промежуток, такие шлаки именуются долгими. В случае если же переход от жёсткого состояния к жидкому происходит в маленьком температурном промежутке, то шлаки именуются маленькими (рис. 43).
Опыт говорит о том, что при сварке отличных показателей при других равных условиях в большинстве случаев дают маленькие шлаки.
Одной шлаковой защиты не хватает, как бы ни была она идеальна. Для получения отличного наплавленного металла нужно легирование, т. е. введение в металл таких элементов, как марганец, хром, никель и т. д. самоё важное значение имеет легирование марганцем, которое в практике используется значительно чаще.
Легирующие элементы вводят в обмазку в виде тонкоизмельчен-ных ферросплавов, ферромарганца, ферросилиция, феррохрома и т. п. Ферросплавы, помимо этого, являются сильными раскис-лителями и уменьшают содержание кислорода в ванне, восстанавливая закись железа.
Кроме минеральных веществ для образования шлаков и ферросплавов для легирования и восстановления в обмазки довольно часто вводят органические вещества: целлюлозу, крахмал, декстрин, сахар, пищевую муку, древесную муку и т. п. Органические вещества под действием большой температуры при сварке разлагаются с образованием смеси газов, имеющих восстановительные особенности, ликвидирующие доступ кислорода к ванне; соединения железа с азотом в присутствии водорода либо газов, богатых водородом, как показывает практика, при сварке по большому счету не образуются. Введение органических веществ, в особенности целлюлозы, разрешает уменьшить количество обмазки на электроде, что особенно принципиально важно для электродов, предназначенных для сварки в вертикальном и потолочном положениях.
Для качественной обмазки серьёзен не только ее состав, но и количество, наносимое на электрод, поскольку конечный результат и ход металлургической реакции зависят от количества шлака, взаимодействующего с металлом.
Рис. 1. Диаграмма затвердевания шлаков