Обрубка и очистка отливок
По окончании выбивки из форм отливки обрубают и очищают. Процесс обрубки содержится в отделении от отливки доходов, литников, выпоров и в удалении заливов (облоев) по месту сопряжения полуформ либо в области стержневых знаков.
Обрубку создают вручную с помощью пневматических зубил, ленточных и дисковых выпивал, прессов и газовой резки. В некоторых случаях прибыли отделяют на токарных станках.
Литники от чугунных отливок отделяют вручную, прибыли и литники от металлических отливок — автогенной резкой. Ленточные и дисковые пилы обширно применяют для обрубки отливок из алюминиевых, магниевых и бронзовых сплавов.
Как правило литники от чугунных отливок отделяют ручным молотком в период, в то время, когда отливка еще сохраняет большую температуру, т.е. сразу же по окончании выбивки отливок из форм до удаления стержней.
Обрубка есть неотёсанной обработкой. По окончании нее все отливки пеогают зачистке с целью удаления небольших заливов, остатков “пнбылей и литников.
Зачистку создают переносными, маятниковыми и стационарными обдирочными станками, шарошками, пневматическими зубилами, электроконтактным методом либо газопламенной обработкой.
В зависимости от твердости отливок для зачистки используют крупнозернистые шлифовальные круги: корундовые для вязких сплавов (стали, латуни, алюминиевых) и карборундовые для жёстких сплавов. В цехах массового производства операцию зачистки реализовывают на многошпиндельных автоматах и полуавтоматах.
Рис. 1. Схема полуавтомата для зачистки отливок: 1 — шлифовальный круг; 2 — поворачивающийся стол; 3 — отливки; 4 — зажимное устройство
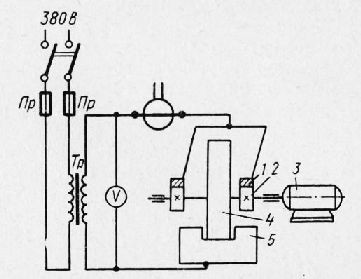
Рис. 2. Схема установки для электроконтактной зачистки отливок: 1 — бронзово-графитовые щетки; 2 — контактные кольца; 3 — двигатель; 4 — диск металлической; 5 — отливка
Зачистка электроконтактным методом основана на оплавлении заливов и заусенцев при взаимодействии поверхности отливок со металлическим диском, вращающимся со скоростью около сорока метров/сек; к диску и отливкам подводят электрический ток. Данный вид зачистки высоко производителен, содействует автоматизации и механизации процесса, усиливает санитарно-гигиенические условия труда.
При зачистке газопламенными горелками происходит оплавление заливов, заусенцев, засоров и шлаковых включений. Газопламенные горелки, как уже указывалось, употребляются кроме этого Для прибылей и удаления литников.
Таким методом, в главном зачищают металлические отливки.
Барабаны периодического действия используют в цехах мелкосерийного производства; в массовом производстве рациональнее использовать барабаны постоянного действия.
Отливки, подлежащие очистке, загружают в барабан. При вращении барабана отливки трутся, подвергаются сотрясениям, переворачиваются, в итоге удаляется приставшая к поверхности отливок формовочная смесь.
Для ускорения улучшения и очистки качества ее вместе с отливками в барабан загружают звездочки из белого чугуна. Острые грани звездочек скоблят поверхность отливок, содействуя более полной очистке их.
В зависимости от толщины и размеров стенок отливок, а кроме этого от рода сплава, длительность очистки в барабанах образовывает 30-90 мин (громаднейшую продолжительность очистки в барабанах требуют металлические отливки).
Многие отливки очищают в барабанах круглого сечения, как в более вместительных; отливки и тонкостенные отливки, имеющие громадную длину, целесообразнее очищать в барабанах прямоугольного сечения. В этих барабанах очистка производится в основном звездочками, поскольку в них нет трения и перемещения отливок.
Барабаны постоянного действия имеют два кожуха. звёздочки и Отливки непрерывно поступают во внутренний кожух; за время перемещения отливок к второму финишу барабана они очищаются.
Звездочки, не доходя до конца барабана, проваливаются во внешний кожух и спиральными направляющими снова подаются к загрузочному окну.
Для очистки отливок обширно применяют гидропескоструйные и дробеструйные аппараты разной конструкции. В таких аппаратах на поверхность отливки под давлением воды либо воздуха соответственно подается песок либо дробь.
дробь и Песок владеют громадной скоростью перемещения и громадной кинетической энергией. Они очищают поверхность отливок тем стремительнее, чем замечательнее струя. Дробеструйную и гидропескоструйную очистку реализовывают в барабанах, на поворотных столах, в особых камерах.
Выбор того либо иного оборудования зависит от их сложности и номенклатуры отливок. Необходимо заметить, что дробеструйной очистке нельзя подвергать отливки из мягких сплавов, поскольку это ухудшает уровень качества их поверхности.
Для очистки отливок из алюминиевых сплавов применяют кусочки алюминиевой проволоки.
Очистка чугунных и металлических отливок ускоряется при применении дробеметной очистки вместо дробеструйной. Воздействие дробеметов основано на применении дробеметной головки, вращающейся со скоростью до 3000 об/мин.
Выбрасываемая громадной центробежной силой дробь направляется к поверхности отливки и очищает ее.
Рис. 3. Дробеметная головка: 1 — воронка; 2 — труба; 3 — распределительное колесо; 4 — рабочее колесо; 5 — неподвижная коробка; 6 — отверстие;.
7 — лопатки рабочего колеса; 8 — болты
Электрохимическая обработка осуществляется кроме этого в каустической соде при 420-480 °С, плотности тока 5-8 а/дм2 и напряжении 2,5-3,5 в. Режим выдержки предусматривает смену направления тока. Отливки в течение 7-8 мин являются катодом, 3-4 мин — анодом и 3-4 мин — снова катодом.
По окончании таковой обработки отливки промывают в холодной (3-4 мин) и горячей (0-10 мин) воде.
Линия запланирована на очистку 8-10 т/ч чугунных отливок весом от 0,2-до 40 кг.