Основные методы проверки кузнечно-прессового оборудования на точность
Способы проверки на нормы и точность точности для каждого вида кузнечно-прессового оборудования, производимого в Советском Альянсе, устанавливаются соответствующими Национальными стандартами (ГОСТ). В силу изюминок того либо другого вида оборудования эти способы смогут различаться друг от друга.
Но наиболее значимые виды испытаний однообразны для всех либо большинства типов автомобилей и выполняются одним и тем же методом. Ниже рассмотрены кое-какие из них.
Рис. 1. Контроль отверстия калибром
Проверка плоскостности поверхностей. Чтобы проверить плоскостность той либо другой поверхности, к ней по разным направлениям прикладывают поверочно гранью линейку у щупом контролируют просвет между поверочной гранью линейки и по верхностью.
Уровень качества поверхность определяется большой величи ной просвета, образующегося на то? либо другой базе. В большинстве случаев данный просвет не должен быть больше 0,06—0,08 mv на длине 1000 мм.
Допускается толь ко вогнутость поверхности, т. е. просвет должен быть в середине линейки, ее качание недопустимо.
Проверка горизонтальности поверхностей. Для проверки горизонтальности той либо другой поверхности к ней прикладывают линейку, на которой устанавливают рамный уровень. По показаниям уровня делают выводы о горизонтальности поверхности.
Для определения отклонения поверхности от горизонтальной плоскости под опустившийся финиш линейки под-кладывают прокладки , пока линейка не займет горизонтального положения. В большинстве случаев допускается отклонение от горизонтали до 0,1 мм на 1000 мм длины.
Проверка вертикальности поверхностей. Отклонение от вертикальности поверхностей контролируют посредством рамного уровня, измеряя его посредством прокладок.
В большинстве случаев отклонение поверхности от вертикали не должно быть больше 0,1 мм на 1000 мм длины.
Проверка параллельности рабочих поверхностей. Для проверки параллельности рабочих поверхностей (направляющих и других элементов автомобилей) на одну из них устанавливают подставку с индикатором.
Индикатор перемещают в продольном и поперечном направлениях и следят за его показаниями. Громаднейшее отклонение в большинстве случаев не должно быть больше 0,1—0,2 мм на 1000 мм длины.
Проверка осей и перпендикулярности поверхностей. Для проверки перпендикулярности каких-либо поверхностей на одной из них устанавливают контрольную плиту.
По плите перемещают угольник, на котором крепится индикатор, его измерительный штифт касается второй поверхности, перпендикулярность которой контролируют. Смотря за показаниями индикатора и отмечая его громаднейшие отклонения, оценивают неперпендикулярность поверхностей.
Подобно проверяется перпендикулярность оси к поверхности. К примеру, для проверки перпендикулярности оси перемещения бабы паровоздушного молота к поверхности штамподержателя на нее ставят угольник, при перемещении бабы смотрят за показаниями индикатора.
В большинстве случаев допуск на неперпендикулярность не превышает 0,1—0,2 мм на длине 1000 мм.
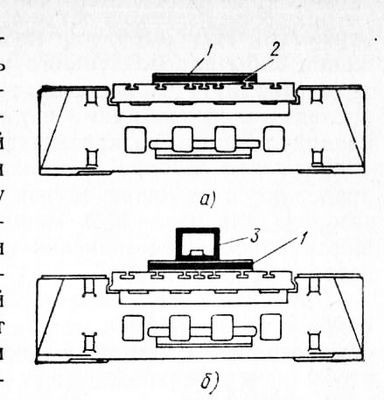
Рис. 2. Схема испытаний на точность:
а — плоскостности поверхностей, б — горизонтальности поверхностей; 1 — линейка, 2 — щуп, 3 — рамный уровень
Проверка зазоров в направляющих. Зазоры в направляющих контролируют посредством щупов.
Обычная величина зазоров для разных автомобилей разна. Контролируют мельчайшее и громаднейшее значения каждого зазора, и суммарный зазор в направляющих.
Проверка биения маховиков. В большинстве случаев контролируют биение маховиков в радиальном и осевом направлениях.
Диагностику реализовывают посредством индикатора. Его устанавливают так, дабы измерительный штифт касался поверхности обода маховика либо его торцовой плоскости.
Биение определяют величиной отклонения показаний индикатора за полный оборот маховика.
При проведении испытаний на точность нужно иметь в виду следующее неспециализированное правило: в случае если по конструктивным изюминкам автомобили не удается произвести замер на длине, к которой отнесен допуск, то его направляться пересчитать на громаднейшую длину, на которой удается ‘произвести замер. Наряду с этим в случаях, в то время, когда по окончании пересчета допуск получается менее 0,01 мм, его направляться принимать равным 0,01 мм.
Нормы точности устанавливаются следующими стандартами:
— для паровоздушных молотов — ГОСТ 8662—83;
— для винтовых фрикционных прессов (молотов) — ГОСТ 7209—79;
— для гидравлических прессов — ГОСТ 10233—75; для пневматических молотов — ГОСТ 6808—76; для кривошипных прессов — ГОСТ 9766—75; для кривошипных горизонтально-ковочных автомобилей неспециализированного назначения с одной подвижной матрицей — ГОСТ 10016—80.
Рис. 3. Проверка вертикальности (а) и параллельности (б) поверхностей:
1 — рамный уровень, 2 индикатор, 3 — подставка
Рис. 4. Проверка перпендикулярности оси перемещения бабы паровоздушного молота опорной поверхности штамподержателя:
1 — штамподержатель, 2 — угольник, 3 — баба, 4 — индикатор
Рис. 5. Проверка зазоров между направляющими станины и ползуна винтового фрикционного пресса (молота)
Рис. 6. Проверка биения маховика в радиальном и осевом направлениях