Получение отверстий большой длины
Во всех областях машино- и приборостроения применяются детали, имеющие глубокие отверстия. Массовыми потребителями деталей с глубокими отверстиями являются общее и специальное машиностроение, судостроение, авиастроение, нефтяное и химическое машиностроение, приборостроение и др.
Детали с глубокими отверстиями встречаются самой разнообразной формы. Производятся они различными методами, с различной точностью и чистотой обработки, из различных материалов и имеют большой диапазон диаметров и длин.
Большинство металлических и неметаллических деталей, имеющих глубокие отверстия, изготовляется без применения глубокого сверления. Чаще всего глубокие отверстия выполняются металлургическими методами: методами литья, гибкой или завивкой листового материала с последующей сваркой в трубы, различными методами прокатки, волочением, экструзией и др.
На рис. 1 в качестве примера показан корпус стеклоочистителя трактора К-700, имеющий два глубоких отверстия. Корпус стеклоочистителя изготовлен литьем под давлением из сплава марки ЦАМ4-1.
Для получения глубоких отверстий малых диаметров и глубоких отверстий в труднообрабатываемых материалах в последнее время успешно применяют физико-химические процессы: электроэрозионный, анодномеханический, ультразвуковой и др.
На рис. 2 приведены три полых цилиндра, имеющих глубокие отверстия диаметром 20-80 мкм. Отверстия в них получены электроэрозионным методом.
Материал цилиндров — твердый сплав марки ВК20.
В отличие от сверления, многие из указанных методов не требуют для изготовления отверстий относительного вращения заготовки и инструмента, а поэтому позволяют довольно просто получать цилиндрические отверстия не только круглого сечения, но и других профилей.
Применение сверления вместо других упомянутых выше методов образования глубоких отверстий производится либо тогда, когда оно является наиболее производительным, либо тогда, когда сверление обеспечивает наиболее полные требования точности или чистоты обработки. В ряде случаев глубокое сверление, особенно скоростное, превосходит по производительности и качеству выполнения операции все другие существующие технологические процессы.
Самым распространенным методом обычного (неглубокого) сверления является сверление так называемыми спиральными сверлами.
Однако этот метод успешно применяется только при глубине сверления, равной не более 3-5 диаметрам сверла. При сверлении же более глубоких отверстий приходится применять прерывистый процесс, так как необходимо часто выводить спиральное сверло из отверстия для очистки от стружки, смазки и охлаждения.
Подобная работа, даже если она производится автоматически, резко снижает производительность сверления.
Важным фактором, от которого зависит непрерывность протекания процесса сверления, является отвод образующейся стружки.
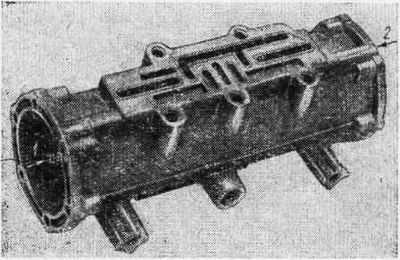
Рис. 1. Корпус стеклоочистителя трактора К-700
Рис. 2. Твердосплавные цилиндры с глубокими отверстиями 0 20-80 мкм
Рис. 3. Спиральное сверло с каналами для подвода охлаждающей жидкости при глубоком сверлении
Рис. 4. Сверло конструкции СКБ-8 1 — 2 — глубокие отверстия и 3,1 мм, длиной 70 мм
Рис. 5. Схемы отвода стружки из зоны резания при глубоком сверлении: а — наружный отвод стружки; б — внутренний отвод стружки: 1 — заготовка; 2 — стебель; 3 — стеблевой суппорт; 4 — насос; 5 — резервуар для охлаждающей жидкости; 6 — стружкоприемиик; 7 — люнет; 8 — сверло; 9 — патрон; 10 — маслоприемник
Чем больше глубина сверления, тем затруднительнее отвод стружки из зоны резания. Спиральные сверла не обеспечивают надежного стружкоотвода. Имеющиеся конструкции спиральных сверл (рис.
3) с внутренними канавками для подвода к режущим кромкам смазочно-охлаждающей жидкости весьма сложны в изготовлении и не получили широкого распространения в промышленности.
В настоящее время некоторое распространение получили сверла конструкции СКБ-8 (рис. 4), отличающиеся от обычных стандартных сверл более крутыми канавками для отвода стружки.
По своему виду данное сверло напоминает бурав для сверления древесины. Стружкоотвод у сверл подобного типа лучше, чем у обычных спиральных сверл, но не гарантирует от возможных заклиниваний удаляемой стружки.
На практике глубокие отверстия сверлятся обычно непрерывно с принудительным либо наружным, либо внутренним отводом стружки. Принудительный отвод стружки осуществляется обычно жидкостью, подводимой в зону резания под давлением.
Весьма редко вместо жидкости применяют сжатый воздух. Для создания циркуляции жидкости применяется специальная оснастка и оборудование.
На рис. 5 показаны упрощенные схемы обоих методов глубокого сверления.
При наружном отводе стружки (рис. 5, а) жидкость поступает от насоса через внутреннюю полость стебля и сверла в зону резания и вместе со стружкой отводится через зазоры между сверлом со стеблем и поверхностью образующегося глубокого отверстия в стружко-приемник.
Стружкоприемник задерживает стружку, а жидкость стекает в отстойник резервуара. В резервуаре (баке) жидкость очищается от механических примесей, охлаждается и вновь насосом направляется через трубопровод (гибкий шланг) и стебель сверла в зону резания.
При внутреннем отводе стружки (рис. 5, б) жидкость направляется насосом в специальное устройство — маслоприемник.
Из маслоприемника жидкость поступает в зону резания через зазоры между наружной поверхностью стебля со сверлом и образующейся поверхностью глубокого отверстия. Затем стружка вместе с жидкостью вымывается в стружкоприемник через внутреннюю полость сверла и стебля.
Далее путь жидкости до насоса аналогичен описанному выше.
Таким образом, современный процесс глубокого сверленияв общих чертах характеризуется как непрерывный процесс образования в сплошном материале заготовки отверстий с относительной длиной более 3-5 диаметров сверления с применением специальных сверл, оснастки и оборудования, обеспечивающих принудительный отвод стружки из зоны резания.
При глубоком сверлении различают сплошное и кольцевое сверление.
При сплошном сверлении (рис. 6, а) весь материал, расположенный в объеме будущего отверстия, измельчается в стружку. При кольцевом сверлении, которое иногда называют трепанацией, в стружку переводится только кольцевая полость (рис. 6, б).
В центре образующегося отверстия остается стержень (или керн), используемый иногда в качестве заготовки для различных деталей.
Если сверление сквозное, то высверливаемый стержень.
Рис. 6. Разновидности глубокого сверления: а — сплошное сверление; б — кольцевое сверление
Рис. 7. Поковка и.высверленный стержень при двустороннем глубоком сверлении
Глубокое сверление занимает особое место среди операций, применяемых при обработке деталей, имеющих большую относительную длину. Специфичность этой операции заключается как в том, что инструмент должен прокладывать себе путь в сплошном материале, не имея заранее подготовленной опоры и жесткого направления, так и в том, что от качества проведения глубокого сверления существенно зависит структура последующего технологического процесса.
Типичным для глубокого сверления также является невозможность непосредственного наблюдения за ходом процесса и трудность выполнения данной операции на универсальном оборудовании без его основательной подготовки.
полностью отделяется от заготовки в конце прохода. Если же сверление глухое, то его необходимо удалять специальными приемами.
В большинстве случаев при необходимости сверления глухих отверстий предпочитают применять только сплошное сверление. Когда же необходимо просверлить сквозное отверстие очень большой относительной длины или сверлить детали из труднообрабатываемых материалов, применяют двустороннее сверление.
На рис. 7 показана крупная стальная поковка, предназначенная для двустороннего кольцевого сверления, а слева от нее расположен высверленный стержень, полученный при сверлении подобной заготовки.
На торце заготовки показана полость, превращаемая при кольцевом сверлении в стружку.
Запроектированный технологический процесс глубокого сверления обычно оценивается по трем показателям:
1) по производительности;
2) по соответствию качества выполнения отверстия техническим требованиям на операцию;
3) по общей стоимости изготовления детали с глубоким отверстием.
Перечисленные дефекты, кроме эллиптичности, являются следствием уводов сверла от заданного направления. Под уводом оси отверстия в данном сечении или на торцах заготовки после сверления (растачивания) понимают отклонение оси полученного отверстия от оси отверстия, намеченного чертежом.
На рис. 8 показаны детали с правильно просверленным отверстием (рис. 8, а) и отверстиями с дефектами, полученными при глубоком сверлении (рис.
8, 6-8, и).
При выполнении любой технологической операции могут быть получены дефекты, в ряде случаев приводящие к неисправимому браку. Дефекты, которые могут сопровождать операцию глубокого сверления, весьма разнообразны и им поэтому посвящен следующий параграф данной главы.
От качества сверления, а следовательно, и от назначения припусков на последующие операции зависит дальнейший процесс обработки не только отверстия, но и всей детали в целом. Поэтому стоимость выполнения операции глубокого сверления необходимо рассматривать не изолированно, а с учетом стоимости всей обработки детали.