Сушка форм и стержней
Операция сушки увеличивает длительность технологического цикла изготовления отливок, исходя из этого стремятся вести сушку форм и стержней с большой скоростью. Скорость сушки определяется температурой нагрева.
Чем выше температура сушки, тем больше скорость испарения жидкости с стержней и поверхности форм, тем стремительнее идут процессы отвердевания связующих и тем меньше длительность сушки. Но, для предупреждения разрушения связующих температуру сушки нельзя повышать беспредельно.
Температура сушки форм должна быть ниже температуры, при которой глина теряет связующую свойство, т.е. ниже 400 °С. На практике температура сушки форм редко превышает 350 °С.
Температура сушки стержней определяется природой связующего. Минимальную температуру сушки имеют стержни, изготовленные на патоке либо канифоли; большую — на глине.
Продолжительность сушки зависит от стержня стенок и толщины формы, газовой среды и влажности смеси, а кроме этого от степени уплотнения формы.
Чем толще стены форм и массивнее стержни, тем продолжительнее сушка при постоянной температуре. К примеру, сушка форм в камерных печах продолжается от 6 до 40 ч, а стержней — от 1 до 10 ч. С повышением влажности смеси длительность сушки возрастает.
Уменьшение плотности формы незначительно снижает скорость сушки. Состав же смеси и ее газопроницаемость фактически не воздействуют на продолжительность сушки.
Формы и стержни сушат в три этапа. В первоначальный этап сушки реализовывают медленный осмотрительный прогрев всей толщи формы (стержня) до 100° С. Потому, что мокрая смесь владеет большей теплопроводностью, чем сухая, то стремятся удержать влагу в стержне (форме).
Для этого сохраняют в печи мокрый нагретый воздушное пространство, уменьшая его циркуляцию. Наличие жидкости в поверхностном слое предотвращает растрескивание его под действием интенсивного парообразования во внутренних частях формы.
Второй этап сушки пребывает в стремительном подъеме температуры формы (стержня) до большого уровня и выдержке при данной температуре в течение нужного времени. Мокрый воздушное пространство в данный период удаляется из сушила и поверхность форм (стержней) обдувается тёплыми сухими газами.
По мере испарения жидкости температура стержня (формы) увеличивается до температуры печных газов; в связующих происходят нужные трансформации (окисление, плавление, обезвоживание), повышающие прочность стержней и форм.
Третий этап сушки содержится в довольно медленном охлаждении сухих форм (стержней) до температуры 50-70 °С, при которой они извлекаются из печи. Уменьшение скорости охлаждения разрешает предотвратить растрескивание поверхностных слоев стержня и их осыпание, но увеличивает длительность процесса.
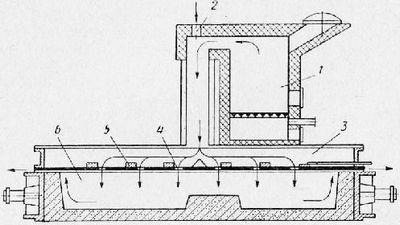
Рис. 1. Схема установки для поверхностной подсушки форм: 1 — топка; 2 — отверстие для подвода дополнительного воздуха; 3 — распределительная камера; 4 — отверстие; 5 — шибер; 6 — полость формы
В некоторых случаях нет необходимости создавать целую сушку форм. Высокий уровень качества отливок обеспечивается и тогда, в то время, когда формы прослушиваются лишь на глубину 10-40 мм от поверхности соприкосновения с металлом, т.е. в то время, когда производится поверхностная подсушка.
Поверхностную подсушку форм применяют в литейных цехах мелкосерийного производства. Продолжительность данной операции образовывает всего 25-30 мин.
Поверхностную подсушку используют, в то время, когда по окончании окончания подсушки форма относительно быстро заливается металлом. В другом случае внешние слои формы снова увлажняются за счет жидкости, сохранившейся в глубинных слоях формы.
Поверхностную подсушку форм реализовывают с помощью переносных сушил. самая совершенная установка, созданная для данной цели на заводе «Станколит», приведена на рис.
57. Еще более рациональна поверхностная подсушка с помощью инфракрасных лучей. При соответствующем подборе мощности
установки с инфракрасными лучами смогут удачно соперничать с переносными сушилами. Подсушка форм инфракрасными лучами удачно используется в крупносерийном производстве.
Сушку форм в большинстве случаев реализовывают в камерных печах периодического действия. Прогрессивным методом есть сушка форм под повышенным давлением.
Сущность этого метода пребывает в том, что в герметично закрытую литейную форму через полость прибыли нагнетают тёплый воздушное пространство под давлением 600-700 мм вод. ст. Проходя через слой уплотненной формовочной смеси, тёплый воздушное пространство высушивает форму.
Данный метод в 3-5 раз более производителен, чем сушка в печах периодического действия, требует меньшего расхода энергии, исключает перегрев поверхности формы и делает ненужным наблюдение за сушкой.
Сушку стержней реализовывают в камерных печах периодического действия либо в конвейерных печах постоянного действия. Камерные печи используют в цехах единичного и мелкосерийного производства, а конвейерные — в крупносерийном и массовом производствах.
Рис. 2. Вертикальное конвейерное сушило:
Рис. 3. Схема сушки стержней токами высокой частоты: 1 — стержень; 2 — электрод; 3 — железная плита на ленте транспортера
Применяют два вида конвейерных печей — вертикальные и горизонтальные.
Вертикальные конвейерные сушила используют для некрупных стержней; производительность их 1-2 т/ч средних стержней. Производительность горизонтальных сушил от 5 до 10 т/ч стержней; они пригодны для сушки больших стержней.
Вертикальные и горизонтальные конвейерные сушила являются печами с принудительной циркуляцией газов. Сушка стержней в них осуществляется с применением плоских и фасонных плит.
Стабильное уровень качества сушки, удобство транспортирования стержней, экономия площади — таковы главные преимущества конвейерных сушил перед камерными.
В индустрию внедрена механизированная сушка стержней токами высокой частоты. Принципиальная схема установки приведена на рис. 3. Данный метод пригоден для сушки плоских стержней, изготовленных из безмаслянных смесей.
Равномерность прогрева стержня, сокращение цикла сушки, уменьшение расхода энергии, улучшение условий труда — таковы главные преимущества этого метода сушки перед вторыми.