Сверление металла
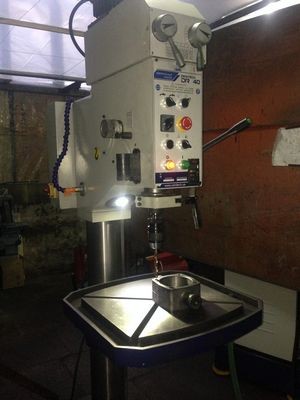
Пожалуй, тяжело себе представить изготовление и сборку какого-либо механизма без того, дабы не появилась необходимость в дальнейшей обработке и сверлении отверстий. Да и в других направлениях слесарного производства, будь то сантехнические работы либо установка бытового газового оборудования, прокладка трубопровода либо ремонт автомобиля, вряд ли возможно обойтись без таковой слесарной операции, как сверление всевозможных отверстий.
Как уже говорилось, совершенным приспособлением для сверления отверстий (и их предстоящей обработки) есть сверлильный станок. Сделаем маленькое отступление и обратимся к истории: как показался сверлильный станок?
В отличие от своих более сложных собратьев-станков — токарного и фрезерного — сверлильный станок был изобретен задолго перед тем, как люди по большому счету определили о существовании железа, не говоря уже о том, дабы обучиться его обрабатывать. Первым сверлильным станком было по сути приспособление, благодаря которому люди в глубокой древности добывали пламя и проделывали отверстия в орудиях труда и охоты.
Оно воображало собой простой охотничий лук, тетива которого в середине была один раз обернута около того предмета, которому и требовалось придать вращение. В большинстве случаев, это была заостренная палка из дерева жёсткой породы, которая упиралась своим острым финишем в углубление, сделанное в лежащей под ней плошке из той же породы дерева.
Придерживая рукой верхний финиш вертикальной палки, человек двигал лук в плоскости, перпендикулярной к данной палке и приводил ее посредством тетивы в стремительное вращение, которого не было возможности бы добиться, вращая ее руками. Совершенно верно таким же образом проделывались отверстия сперва в не через чур плотных кусках камня, а позже, в то время, когда человек обучился закреплять на финише вращающейся палки жёсткие каменные наконечники — ив прочных породах.
Со временем приспособление усовершенствовалось, оказались новые методы зажима нижней плашки и вращающегося «сверла», устройства для усиления прижима их друг к другу (для повышения силы трения), новые методы приводить «сверло» во вращение. Так за большое количество столетий неспешно изменялся сверлильный станок, пока не купил современный вид.
Сейчас сверлильный станок складывается из штатива и подвижного стола на котором крепится шпиндель с патроном. Он бывает вертикально-сверлильным и горизонтально сверлильным, но слесари, в большинстве случаев, предпочитают устанавливать в собственных домашних мастерских как раз вертикально-сверлильные станки.
Но кроме того при наличии в вашем арсенале сверлильного станка, нужно кроме этого иметь и переносной инструмент для сверления (электрическую дрель): она используется в том случае, в то время, когда нужно просверлить отверстие в месте, недоступном для станка.
Существуют неспециализированные правила сверления (как на станке, так и посредством дрели):
— в ходе разметочных работ центр будущего отверстия в обязательном порядке направляться отметить кернером, тогда при работе сверло устанавливается в керн, что содействует большей точности;
— при выборе диаметра сверла направляться учитывать его вибрацию в патроне, в следствии чего отверстие получается пара большего диаметра, чем сверло. Отклонение это достаточно мало — от 0,05 до 0,3 мм — и имеет значение в том случае, в то время, когда требуется особенная точность;
— при сверлении сплавов и металлов в следствии трения температура режущего инструмента (сверла, зенкера) существенно увеличивается, что ведет к стремительному его износу. Чтобы повысить стойкость инструментов, при сверлении применяют охлаждающие жидкости, в частности воду;
— затупленные режущие инструменты не только образуют некачественные отверстия, но и сами стремительнее выходят из строя, исходя из этого их направляться вовремя затачивать: сверла — под углом (в вершине) 116-118 градусов, конические зенкеры — 60, 90, 120 градусов. Заточку создают вручную на заточном станке: сверло приставляют к кругу заточного станка одной из режущих кромок под углом 58-60 градусов и медлено поворачивают его около собственной оси, после этого таким же образом затачивают вторую режущую кромку. Наряду с этим нужно следить, дабы обе режущие кромки были заточены под однообразным углом и имели однообразную длину;
— для сверления глухих отверстий на многих сверлильных станках имеются механизмы автоматической подачи с лимбами, каковые и определяют движение сверла на нужную глубину. В случае если же ваш станок не оснащен таким механизмом либо вы сверлите ручной дрелью, то возможно применять сверло со втулочным упором;
— в случае если вам необходимо просверлить неполное отверстие, расположенное у края подробности, то наложите на подробность пластину из для того чтобы же материала, целый пакет укрепите в тисках и просверлите отверстие. Пластина после этого снимается;
— в то время, когда нужно просверлить отверстие в полой подробности (к примеру, в трубе), отверстие предварительно забивают древесной пробкой. В случае если труба громадного диаметра, а отверстие требуется сквозное, то приходится сверлить с двух сторон.
В этом случае, дабы уменьшить разметку и сделать ее самая точной, возможно воспользоваться особым приспособлением. Оно складывается из двух совсем однообразных призм, между которыми зажимается труба.
Любая призма имеет совершенно верно выверенные друг против друга зажатые в их противоположных вершинах встречные винты-кернеры. Призмы также совершенно верно выставлены посредством боковых щек.
В то время, когда труба зажимается между призмами, на ней остаются маленькие, расположенные приятель наоборот приятеля лунки от винтов-кернеров.
По окончании сверления по таковой разметке отверстия в трубе будут соответствовать друг другу с намного большей точностью;
— взять ступенчатые отверстия возможно двумя методами. Первый: сперва сверлится отверстие мельчайшего диаметра, после этого (на нужную глубину) — отверстие большего диаметра и последним просверливается отверстие громаднейшего диаметра; второй метод — с точностью до напротив: сперва на нужную глубину сверлят отверстие громаднейшего диаметра, после этого — меньшего, и в конце — мельчайшего диаметра;
— в случае если необходимо просверлить отверстие на криволинейной плоскости либо плоскости, расположенной под углом, то сперва необходимо осуществить (выпилить, вырубить) площадку, перпендикулярную к оси будущего отверстия, накернить центр, а после этого сверлить отверстие;
— отверстия диаметром более чем 25 мм сверлят в два приема: сперва просверливают отверстие сверлом меньшего диаметра (10-20 мм), а после этого рассверливают сверлом нужного диаметра;
— при сверлении подробностей имеющих громадную толщину (при глубоком сверлении), в то время, когда глубина отверстия более пяти диаметров сверла, его необходимо иногда вынимать из отверстия и выдувать стружку, в противном случае инструмент может заклинить;
— композиционные (складывающиеся из нескольких разнородных слоев) материалы тяжело сверлить в первую очередь вследствие того что при обработке на них появляются трещины. Избежать этого возможно весьма несложным методом: перед сверлением таковой материал необходимо затопить и заморозить — трещины в этом случае не покажутся;
— высокопрочные материалы — сталь, чугун — простые сверла не берут. Для их сверления у домашних слесарей громадной популярностью пользуются сверла с наконечниками из так именуемого победита.
Он был взят в Российской Федерации во второй половине 20-ых годов XX века, он складывается из 90% кобальта и карбида 10% вольфрама. Для данной же цели возможно обзавестись и алмазным сверлом, наконечник которого изготовлен с применением синтетических алмазов, — оно заметно увеличивает скорость сверления металла.