Заточка и доводка режущих инструментов
Завершающими операциями изготовления режущего инструмента являются доводка и заточка. Не смотря на то, что эти операции выполняются заточниками, слесарь-инструментальщик обязан знать главные методы заточки и мочь заточить и довести самые простые и распространенные инструменты — резцы, сверла, развертки.
Возможно принять следующие варианты технологического процесса заточки инструментов: предварительная заточка кругами из зеленого карбида кремния в один момент твердосплавной пластинки и державки и доводка и окончательная заточка алмазными кругами;доводка и окончательная заточка алмазными кругами; обработка державки кругами из электрокорунда, предварительная заточка кругами из зеленого карбида кремния и доводка и окончательная заточка алмазными кругами.
Заточку твердосплавных инструментов кругами зеленого карбида кремния на неавтоматизированном оборудовании направляться проводить без охлаждения, а на автоматизированном — с охлаждением водным раствором нитрита натрия с подачей его в обязательном порядке в зону инструмента и контакта круга.
доводку и Заточку режущих инструментов реализовывают на точилах, универсальных и особых стайках, и на кругло-, плоско- и профилешлифовальных станках.
Точила предназначены по большей части для заточки резцов всех типов. При отсутствии особых заточных станков на точилах затачивают и сверла.
доводка и Ручная заточка резцов.
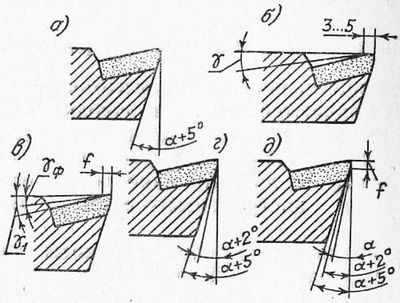
Рис. 1. Схема заточки резцов.
У резцов главную заточку реализовывают по задним поверхностям, а запасного — по передним, исходя из этого принята заточка двойных углов по передней поверхности, а тройных — по основной задней поверхности.
Перед-заточкой нужно проверить состояние заточного станка, на котором должны быть установлены защитный прозрачный экран, подручник и нужные шлифовальные круги, ванна с охлаждающей жидкостью и кнопки «Пуск—стоп». Зазор между подручником и шлифовальным кругом обязан составлять не более 2…3 мм.
По высоте подручник должен быть установлен так, дабы при заточке по пластинке режущая кромка была на высоте оси вращения шлифовального круга в горизонтальной плоскости. При заточке по державке на высоте оси вращения шлифовального круга обязана пребывать опорная поверхность державки.
Рис. 2. Точило.
Заточка резца по запасному задней поверхности (по державке) продемонстрирована на рис. 3. Резец располагают так, дабы угол между основной и вспомогательной поверхностями составлял приблизительно 90.
Заточка резца по передней поверхности приведена на рис. 3,в.
Заточку создают на длине 3…5 мм под углом у. Резец берут рукой за державку, а громадным пальцем левой руки прижимают его к шлифовальному кругу. Резец должен быть установлен так, дабы основная режущая кромка а была расположена параллельно плоскости вращения круга. Для предварительной заточки по пластинке используют шлифовальный круг из карбида кремния зернистостью 40…25, а для окончательной — в один момент поворачивая его около вершины по часовой стрелке приблизительно на 1/3 оборота,
2. Контролируют угол наклона режущей кромки к оси сверла. Сверло берут в левую руку, а шаблон — в правую и прикладывают долгую рабочую поверхность Б шаблона к боковой поверхности сверла; по плотности прилегания маленькой рабочей поверхности шаблона к режущей кромке А сверла определяют правильность заточки.
Угол наклона режущей кромки к оси сверла возможно проверить и угломером, предварительно установив его на угол 118°.
Рис. 3. Ручная заточка сверл.
3. Затачивают вторую режущую кромку. Приемы контроля и затачивания те же, что и для первой режущей кромки.
4 Контролируют величину угла заточки режущих кромок при вершине сверла и их длину. В левую руку берут сверло, а в правую — шаблон и устанавливают шаблон на режущие кромки сверла, строго совмещая долгую рабочую поверхность Б шаблона с осью сверла.
По плотности прилегания режущих кромок к рабочей их длине и поверхности шаблона (она должна быть однообразной) определяют правильность заточки сверла.
5. Контролируют задние углы а, образующиеся при заточке наклоном задних поверхностей. При верной заточке режущих кромок точки Б задних поверхностей должны быть немного ниже вершин А режущих кромок.
6. Контролируют угол наклона поперечной кромки. Для сверл диаметром до 15 мм он обязан составлять 50°, а более чем 15 мм — 55°. Проверка угла наклона поперечной кромки шаблоном продемонстрирована на рис.
108, о, где 1 — сверло; 2 — шаблон; А — режущая кромка; Б — поперечная кромка.
Уровень качества заточки рекомендуется осуществлять контроль сверлением. В случае если углы наклона режущих кромок к оси сверла и протяженность кромок однообразны, то стружка будет выходить из отверстия по двум спиральным канавкам, а вдруг углы неодинаковы, то стружка будет выходить из одной канавки.
Доводка разверток. Из всех концевых инструментов лишь развертки доводятся слесарем-инструментальщиком, что разъясняется высокой шероховатостью и точностью их рабочих поверхностей.
Из ручных способов доводки разверток наиболее высокий уровень качества снабжает обработка посредством разжимного чугунного кольца.
Развертка с надетым на нее чугунным кольцом устанавливается в центры и через хомутик приобретает вращение от шпинделя станка. На разжимное кольцо наносится доводочная паста.
При продольном перемещении и вращении развёртки чугунного кольца происходит доводка по наружному диаметру развертки.
На некоторых фирмах доводку либо калибровку разверток реализовывают методом продавливания их через особое калибровочное кольцо. Такие кольца для доводки цилиндрических разверток изготовляют из стали У12 твердостью HRC 62…64.
Процесс доводки содержится в следующем. Новая развертка без фасок диаметром, равным номинальному плюс 0,03…0,06 мм, продавливается под прессом через калибровочное кольцо соответствующего размера.
В следствии уплотнения материала на цилиндрической части зубьев образуется фаска шириной 0,03…0,05 мм.
Рис. 5. Доводка развертки.
Таковой метод доводки благодаря наклепу упрочняет режущие кромки, снабжает равномерность высоты зубьев калибрующей части развертки и повышает производительность труда слесаря-инструментальщика.
Регулировка разверток. Разжимные ручные развертки диаметром от 6 до 50 мм предназначены для простого развертывания отверстий.
Размеры изношенной разжимной развертки возможно вернуть методом ее регулирования, в ходе которого диаметр инструмента может изменяться на 0,15…0,5 мм.
Корпус разжимной развертки изготовлен полым, а его рабочая часть имеет от 3 до 6 (через 2—3 зуба) продольных прорезей. Регулировка осуществляется вращением винта, что перемещает шарик на протяжении конического отверстия корпуса и так разжимает развертку.
По окончании регулировки развертка доводится до нужного размера.
Изготовляются раздвижные регулируемые разверт-и преимуществом которых являются намного большие пределы регулирования диаметров (0.5…3 мм). Большая часть машинных разверток владеет одним неспециализированным недочётом — по мере износа их нереально регулировать по диаметру.
Дабы иметь такую возможность, используют сборные развертки с разными способами крепления быстрорежущих и твердосплавных вставных зубьев.
Рис. 6. Регулировка разверток.
Громадный интерес воображают развертки с механическим креплением пластинок жёсткого сплава. В пазы корпуса вставляются твердо сплавные пластинки и прижимаются к стенке паз рифленым клином.
На финише этого клина имеется заплечик, которым пластинка удерживается от неремеще. ния на протяжении оси под действием осевых сил при развертьь вании. По мере износа пластинка выдвигается по осно-ванию паза, имеющему подъем в 5°, что компенсирует износ по диаметру.
Износ торца пластинки компенсируется перестановкой клина на одно рифление в осевом направлении.
Приведенная конструкция развертки имеет заднее направление, которое может обеспечить более правильную обработку отверстий.