Восстановление направляющих каретки суппорта токарного станка
У направляющих каретки суппорта износ появляется на поверхностях 1, 2, 3, 4,7, и поверхности 1, 2, и изнашиваются больше в средней части. Они становятся вогнутыми и в следствии нарушается обоюдная параллельность этих поверхностей и параллельность оси отверстия под винт.
Повышенный износ поверхностей и влечет за собой наклон каретки в сторону фартука, как продемонстрировано пунктирными линиями на верхней части рис. 1, б.
Помимо этого, из-за неравномерного распределения упрочнений резания на поверхностях к неспешно происходит разворот каретки. Это со своей стороны приводит к неравномерному износу направляющих по длине.
Нарушается перпендикулярность поперечных направляющих и довольно продольных направляющих.
Нижняя поверхность, где крепится фартук, утрачивает параллельность продольным направляющим, перекашивается в поперечном направлении, в следствии чего фартук приобретает наклон к станине, в сторону уменьшения угла образуемого поверхностями станины и каретки для крепления коробки подач.
При ремонте нужно вернуть начальную (в пределах 0,03 мм на длину 300 мм) точность многих координат, а также: параллельность поверхностей 1, 2, 3 оси винта в горизонтальной и вертикальной плоскостях, параллельность поверхностей, плоскости для крепления фартука перпендикулярность поперечных направляющих, (по линии ее) направляющим; перпендикулярность поверхности плоскости для крепления коробки подач на станине (на рисунке не продемонстрировано); параллельность направляющих 7, 8, поверхности.
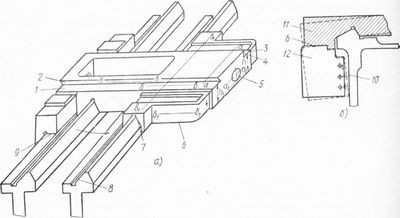
Рис. 1. Износ направляющих каретки суппорта токарного станка:
а — размещение направляющих, б — наклон фартука и каретки благодаря износа направляющих
Ремонт направляющих кареток рационально затевать с поверхностей 1, 2, 3, 4, а для выверки их к оси отверстия в него устанавливают контрольную оправку. Но геометрическая точность этих отверстий довольно часто выясняется нарушенной.
Исходя из этого целесообразно применять как базу грань, которая неизменно перпендикулярна оси отверстия для винта поперечной подачи, и плоскость.
Направляющие у каретки смогут быть отремонтированы такими методами:
— все направляющие строгают и шабрят либо ограничиваются одним шабрением либо шлифованием;
— поверхности, и восстанавливают строганием и компенсируют износ наделками из чугуна, латуни, текстолита, капрона, пластмассовых композиций и др.
Ниже рассматривается рациональный метод восстановления направляющих каретки скоростным фрезерованием и поверхностей, и пластмассовыми композициями.
Для ремонта пользуются приспособлением, воображающим двухступенчатое основание с Т-подвижными домкратами и образными пазами.
Приспособление располагают на столе вертикально-фрезерного станка, а каретку прикрепляют поверхностью к верхней ступени приспособления винтами через существующие отверстия для крепления фартука при помощи подвижных гаек, расположенных в Т-образных пазах.
Рис. 2. Установка каретки на приспособлении
После этого под продольные направляющие каретки подводят подвижные домкраты и регулируют винтами и с гайками так, дабы обеспечить нужный подпор, кроме деформацию каретки при закреплении ее зажимным устройством. Потом, посредством индикатора (на рисунке не продемонстрирован) выверяют поверхность каретки (разворотом приспособления на столе станка), дабы она размешалась параллельно перемещению стола в поперечном направлении, допуская отклонения до 0,03 мм на всей протяженности, наряду с этим ось отверстия окажется перпендикулярной направлению поперечного перемещения стола.
Затем приспособление закрепляют на столе станка посредством прижимов (на рисунке не продемонстрировано). По окончании закрепления приступают к обработке поперечных направляющих формы «ласточкина хвоста» скоростным фрезерованием.
Фрезерование создают заточенной в соответствии с углом направляющих торцовой фрезой, оснащенной режущими пластинками из жёсткого сплава. Скорость резания должна быть 3—4 м/с при подаче 200 мм/мин.
Сначала за один либо два прохода до вывода износа обрабатывают в один момент поверхности, после этого, не изменяя положения фрезы, за один проход — поверхности.
В следствии достигается высокая точность выполнения в предела! 0,01—0,03 мм и уровень качества поверхностей по 7—8-м классам шероховатости.
Точность координат каретки восстанавливается машинально поперечные направляющие поверхности 1,2,3,6 оказываются взаимопараллельными осп для винта поперечной плоскости и подачи для крепления фартука, а также по размерам.
Поверхности, восстанавливают по окончании восстановления попе речных направляющих. Восстановление реализовывают пластмассовыми композициями либо железными накладками из пластмасс и металл jb.
Рис. 3. Герметизация направляющих каретки для заливки акрилопластом
Восстановление направляющих пластмассовыми композициями выполняется в таковой последовательности.
1. Ремонтируют поперечные направляющие каретки методами, вышеуказанными.
2. С поверхностей каретки, сопрягаемых с направляющими станины, сострагивают слой толщиной 2—3 мм. Шероховатость поверхности обязана соответствовать 1-му классу.
3. На каретке сверлят четыре отверстия, нарезают резьбу и устанавливают винты с гайками, такие же два винта устанавливают на задней стенке каретки (на рисунке не продемонстрировано). В средней части направляющих сверлят по отверстию диаметром б—8 мм.
4. На отремонтированные направляющие станины бруском хозяйственного мыла наносят узкий равномерный изоляционный слой.
5. Предварительно простроганные направляющие каретки обезжиривают тампоном из яркой ткани, намоченном в ацетоне, и просушивают в течение 15—20 мин.
6. Каретку устанавливают на отремонтированные направляющие станины, прикрепляют заднюю прижимную планку, устанавливают фартук, коробку подач, ходовой винт, валы и поддерживающий кронштейн (на рисунке не продемонстрирован), располагающийся на правом финише станины. валов осей и Параллельность винта направляющим станины предварительно выверяют.
7. Устанавливают приспособление для проверки перпендикулярности направляющих каретки и приспособление для проверки параллельности осей винтов и валов направляющим. Это приспособление скреплено с универсальным мостиком.
8. Устанавливают уровни, располагая их так, как продемонстрировано на рисунке.
9. Регулируют положение каретки посредством четырех винтов. Наряду с этим по показаниям индикатора устанавливают перпендикулярность поперечных направляющих каретки направляющим станины.
По уровню определяют перпендикулярность поверхности каретки для плоскости и крепления фартука коробки подач на станине. Уровнем устанавливают параллельность плоскости каретки под фартук направляющим станины.
Приспособлением контролируют соосность отверстий для ходового винта и вала самохода в фартуке и коробке подач.
10. По окончании того как все положения выверены и регулировочные винты и затянуты контргайками, снимают ходовой винт, фартук и вал самохода.
После этого герметизируют пластилином станины и поверхности каретки со стороны фартука и задней прижимной планки. По краям каретки делают из пластилина воронки и 5, а около просверленных отверстий в средней части направляющих — воронки.
11. Приготовляют раствор акрилопласта и заливают в среднюю воронку одной из направляющих , пока уровень жидкого пластика в крайних воронках не сравняется с уровнем в средней воронке.
Так же заливают вторую направляющую.
12. Выдерживают каретку на станине в течение 2—3 ч при температуре 18—20 °С.
13. Снимают каретку с направляющих станины, очищают от пластилина, удаляют приливы пластика, делают канавки для смазки, заделывают стопорами либо акрилопластом отверстия установочных винтов.
Рис. 4. Регулировка положения каретки винтами:
1 — приспособление для проверки отклонения от .перпендикулярности направляющих каретки. — индикатор. 3, 4 — уровни. 5, 6 — установочные винты, 7 — универсальный мостик, 8 — приспособление для проверки отклонений от параллельности осей винтов, 9 — фартук, 10— каретка, 11 — вал, 12 — ходовой винт, 13 — коробка подач
Рис. 5. Проверка направляющих консоли на собранном фрезерном станке:
а — проверка отклонений направляющих от параллельности оси, б — проверка отклонений от перпендикулярности поверхности стола направляющим консоли