Коррозия и эрозия материалов и методы защиты
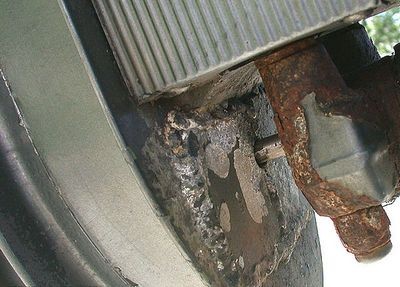
Коррозией именуется процесс сплавов и разрушения металлов в следствии химического и электрохимического сотрудничества их с внешней средой.
Материалы конструкций современных летательных аппаратов, вспомогательного оборудования и двигательных установок во многих случаях находятся в условиях действия активных агрессивных сред, напряжений, других факторов и высоких температур. В этих условиях появляются и протекают химические и электрохимические процессы, которые связаны с сотрудничеством внешней среды и металла, что приводит к разрушению и ведет к понижению эксплуатационной надежности конструкций.
Наряду с этим разрушающийся металл переходит в разные химические соединения в виде окислов, гидратов окисей, солей, именуемых продуктами коррозии.
Самый распространенными примерами коррозии помогают образование ржавчины либо окалины на железе, окиси алюминия на алюминиевых сплавах, углекислой меди на изделиях из бронзовых сплавов и т. д.
Коррозия была и все еще остается сильным бичом металлов. Она уносит каждый год миллионы тысячь киллограм железных материалов.
Но эти утраты не смогут полностью характеризовать ущерб, наносимый коррозией в важном и особом машиностроении, где вредное воздействие ее оценивается не столько весовыми показателями утраты металла, сколько потерей механических и физических особенностей материалов и понижением конструкции и эксплуатационной надёжности деталей в целом, происходящих в следствии кроме того незначительных, в случае если делать выводы по весу уничтоженного металла, коррозионных процессов.
Процессы коррозии классифицируются по сущности протекающих явлений, по виду агрессивной среды и по характеру разрушения. По сущности протекающих явлений различают два вида коррозии: химическую и электрохимическую.
Химическая коррозия есть следствием прямых химических реакций, появляющихся между агентами и металлом внешней среды. Электрохимическая коррозия связана с наличием электролитов, образованием гальванических элементов, либо пар и происхождением в них электрического тока.
Рис. 1. Главные виды коррозионного разрушения: 1 — равномерная коррозия; 2 — местная коррозия; 3 — межкристаллитная коррозия; 4 — коррозионное растрескивание
По виду агрессивной среды различаются:
1. Атмосферная коррозия, протекающая в условиях простой атмосферы с свойственными ей изюминками: наличием влаги и кислорода, а в промышленных районах и городах — сернистых газов, аммиака и т. п. Коррозия в морской воздухе характеризуется присутствием в среде ионов Cl.
2. Почвенная коррозия, протекающая в условиях почвенной жидкости и блуждающих электрических токов.
3. Жидкостная коррозия, развивающаяся в жидких агрессивных средах, к примеру в растворах кислот, щелочей, солей и т. д.
4. Газовая коррозия, протекающая в газовой среде при большой температуре.
По характеру разрушения различается четыре главных вида коррозии (рис. 169):
1) равномерная;
2) местная: точечная и язвенная;
3) межкристаллитная, либо интеркристаллитная;
4) коррозионное растрескивание.
Равномерная коррозия характеризуется развитием процесса по всей поверхности металла приблизительно с однообразной скоростью, в следствии чего слой продуктов коррозии получается более либо менее однообразным по толщине.
Местная коррозия протекает избирательно и характеризуется разрушением отдельных участков поверхности металла. Наряду с этим очаги коррозии смогут быть точечными либо язвенными.
Местная коррозия оказывает более негативное влияние на эксплуатационную надежность изделий, чем равномерная, потому, что приводит к неравномерному разрушению металла и образование концентраторов напряжений.
Межкристаллитная коррозия начинается по границам зерен сплава и ведет к нарушению связи между кристаллитами. Она приводит к значительному ухудшению механических особенностей изделия и есть очень коварной, поскольку снаружи практически ничем не проявляется.
Данный вид коррозии возможно обнаружен по потере изделием железного звука, по понижению электропроводности, и по прочности и уменьшению пластичности.
Коррозионное растрескивание есть следствием совместного действия на металл агрессивной среды и механических растягивающих напряжений. Оно начинается при долгой работе изделия в тяжелых условиях коррозии под напряжением.
Оценка коррозии осуществляется методом определения весовой степени разрушения и потери металла его.
Утраты металла по весу (коррозионные утраты) являются количеством металла, перевоплощённое в продукты коррозии за этот временной отрезок. Как правило для оценки интенсивности коррозии пользуются понятием скорости коррозии, являющейся весовое количество вещества, уничтоженного в единицу времени, отнесенное к единице корродирующей поверхности.
Скорость коррозии выражается в г/м2 час, либо в г/см2 час, либо в мг/см2 час.
Во многих случаях, в особенности при оценке скорости равномерной коррозии, и для сравнения коррозионной стойкости разных металлов, для оценки коррозионных утрат пользуются показателем глубины коррозии, воображающим собой толщину уничтоженного слоя металла, выраженную в миллиметрах, за этот отрезок времени, к примеру за год.
В случаях местной и межкристаллитной коррозии, и при коррозионном растрескивании более объективной и верной есть оценка процесса коррозии по понижению механических особенностей, потому, что она показывает яркое влияние коррозии на эксплуатационные особенности деталей и материалов.
Вместе с тем коррозионные утраты, выраженные скоростью коррозии либо показателем глубины коррозии, являются наиболее значимым критерием для сравнительной оценки коррозионной стойкости материалов при опробовании их в разных средах и при различных температурах.
В зависимости от характера продуктов коррозии утраты металла смогут определяться убылью в весе либо, напротив, привесом. Убыль в весе определяется в любых ситуациях, в то время, когда продукты коррозии или растворимы в агрессивной среде, или легко отделяются от поверхности металла, а привес — при, в то время, когда продукты коррозии тяжело отделимы от металла.
Свойство материала сопротивляться коррозии оценивается баллом коррозионной стойкости.